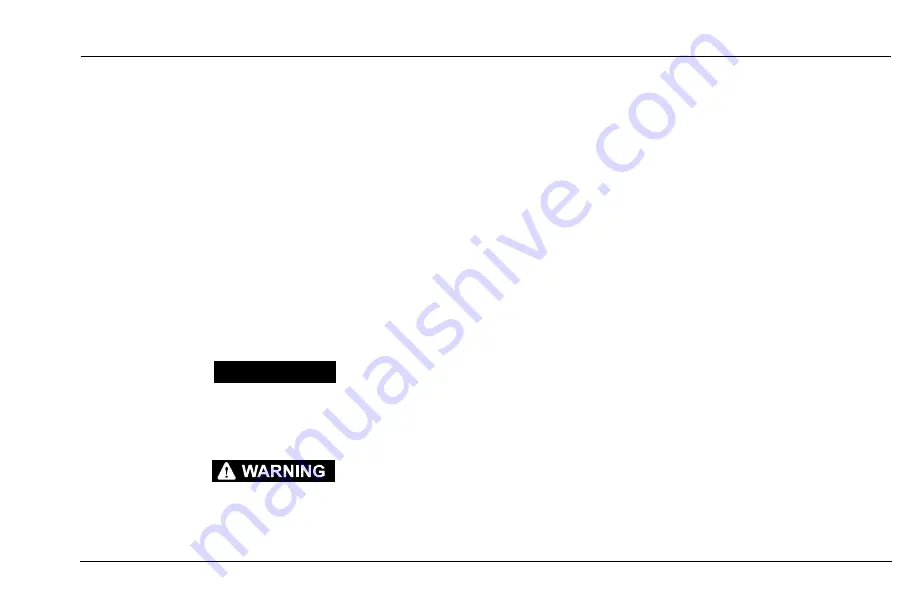
SECTION 4 - EMERGENCY PROCEDURES
LIFTPOD by JLG
1001070465
4-1
SECTION 4. EMERGENCY PROCEDURES
4.1
GENERAL INFORMATION
This section explains the steps to be taken in case of an emer-
gency situation during operation.
Manual Descent Crank
The platform manual descent crank is provided to:
• Allow the platform operator to lower the platform in the
event that the cordless drill or powerpack batteries run out
of sufficient charge to lower the platform;
• Allow ground personnel to lower the platform in the event
that the platform operator cannot lower the platform once
elevated.
NOTICE
THE CRANK IS DESIGNED FOR DESCENT IN CASE OF LOSS OF POWER
ONLY. IT MUST NOT BE USED TO ELEVATE THE PLATFORM OR FOR
GENERAL OPERATIONS.
IF THE BATTERIES ARE DISCHARGED WHILE THE UNIT IS ELEVATED,
DO NOT CLIMB OUT OF THE PLATFORM. USE THE MANUAL DESCENT
CRANK.
Discharged Battery
If the battery should run out of charge before the platform has fully
descended:
1.
Remove the cordless drill and place it inside the plat-
form. If the optional powerpack is installed, remove it
and place it sideways against the back panel in the plat-
form (see Figure 4-1.).
2.
Remove the manual descent crank from the mounting
clips inside the platform.
3.
Engage the hexagon at the top of the driveshaft with the
socket end of the manual crank.
4.
Push down on top of the handle to disengage the drive-
shaft lock and wind anti clockwise until the platform
comes to rest against the stops on the base.
Go to Discount-Equipment.com
to order your parts