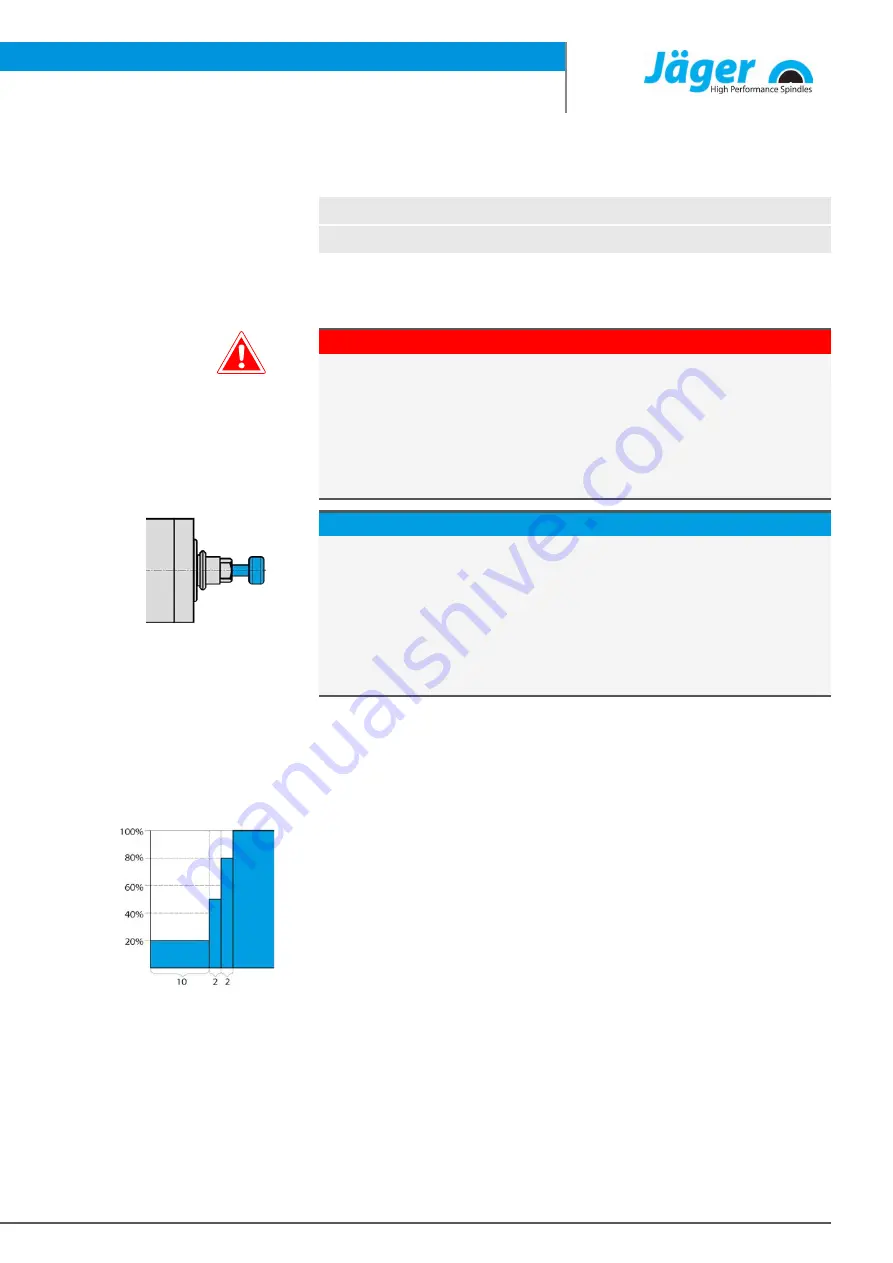
Commissioning
Item no. 10408021, Revision 02
29 ( 44 )
8.4.3
Setting values
For guidelines on air quality,
see "Air purity classes (ISO
8573-1)
" section.
Ü
Keep to the following values:
Taper cleaning
4,5 - 6 bar
Pneumatic system for tool change
≥ 6,0 bar
9
Commissioning
DANGER: Due to flying parts.
If the speed is selected incorrectly, the HF spindle or the tool may be de-
stroyed and their fragments may be flung out.
u
Note the maximum speed for the selected tool.
u
Note the maximum speed for the HF spindle.
u
The maximum permissible speed of the HF spindle for commissioning /
processing is always the
lowest
specified speed.
Example of design: Inserting the
shank
Note: Ensure functionality.
u
Never operate the HF spindle without a clamped tool shank.
If no tool shank is clamped:
q
The clamping system is damaged by the centrifugal forces.
q
The clamping system is shifted.
q
The balance of the HF spindle is affected.
q
The bearing is damaged.
Ü
Turn the shaft of the spindle at least ten times by hand.
Ü
Before storing and before commissioning only clean the cooling duct with
compressed air.
9.1
Running-in schedule
Duration of load (minutes)
Max. load (%)
Ü
Put the HF spindle into operation with a clamped tool (without machining)
for approx. 10 minutes.
Ü
The speed in this case should be no more than 20% of the maximum per-
missible speed for the HF spindle.
Ä
See definition: Max. permissible speed
Ü
Allow the HF spindle to run for approx. 2 minutes at a maximum of 50% of
the maximum permissible speed.
Ü
Operate the HF spindle for approx. 2 more minutes at a maximum of 80%
of the maximum permissible speed.
The HF spindle is now ready for operation.