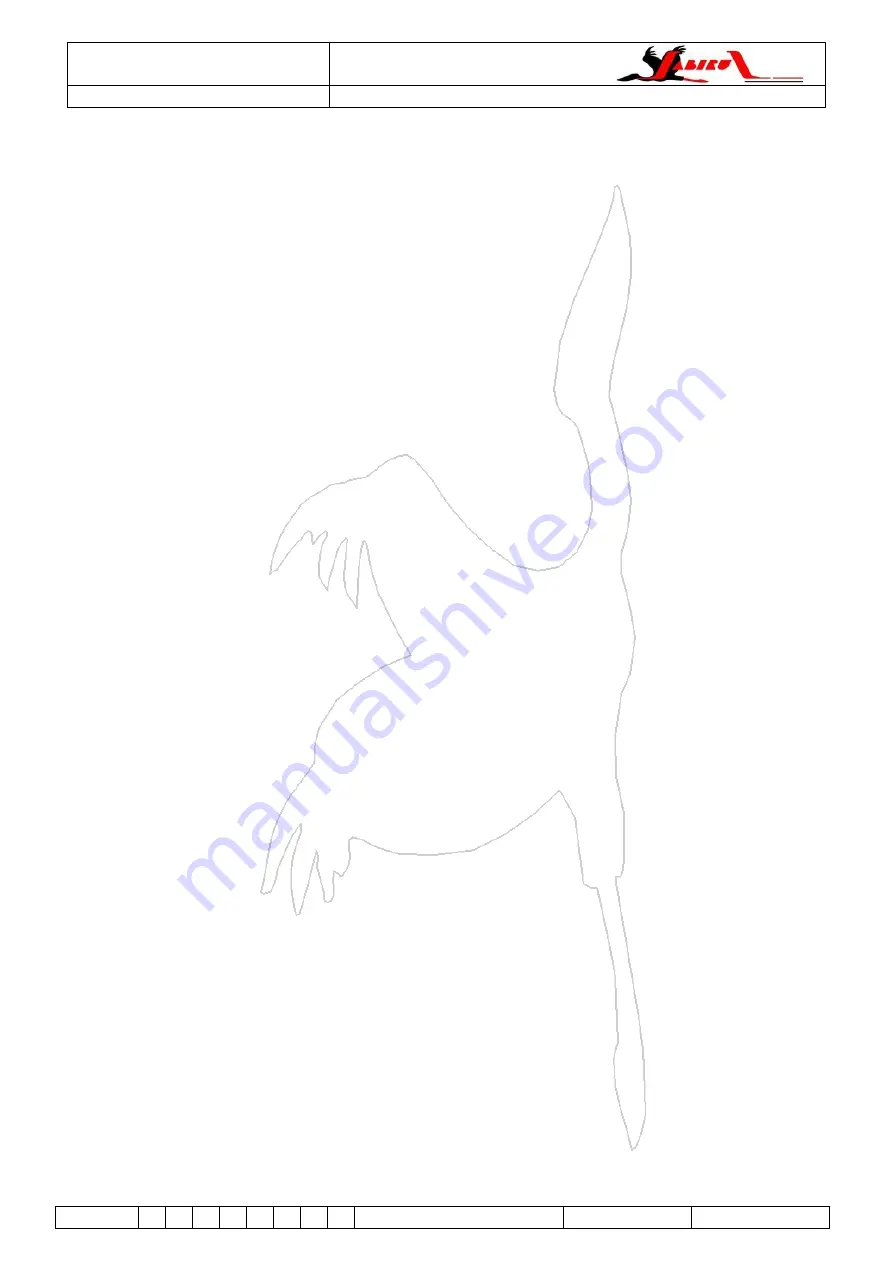
Aircraft Service Manual
Jabiru Aircraft
Pty Ltd
JTM001-1
J120, J160, J170, J200/J400, J230/J430, J250/J450 Variants
REVISION
1
Dated: Nov 2011
Issued By: SW
Page: 40 of 233
Jack the aircraft and pull the un-loaded main undercarriage leg fwd and aft to check for looseness.
Repeat for the second leg.
Inspect the nose leg, steering links, tension links & fairings. Check for dents, bends, cracks,
corrosion, damaged or missing hardware and signs of rubbing etc. Wriggle the trailing arm front
suspension and check for any slop or wear in the pivot bushings of the suspension.
Check for smooth rotation with no bearing “rumble” or slop. Replace worn or damaged bearings.
Inspect the nose gear housing & bushes for wear
– ensure there is no excess vertical or horizontal
slop in the fit of the leg to the housing.
Inspect the main gear struts, clamps, bolts & nuts. Check for rubbing, cracks, corrosion, missing or
damaged hardware and any other damage.
Replace the main gear bolts at the life indicated in Section 4.2 or earlier if the airframe is subject to
rough runways, taxiways or training operations.
Check the tyre pressure and the condition of tyres & tubes. Examine tyres for wear, cuts, bruises
and slippage
Apply the hand brake. Standing in front of the aircraft, pull firmly on the propeller
– placing hands
immediately beside the spinner. Rock the aircraft forward and aft, left and right while observing the
nose leg and both main legs. Any excess movement, noise or vibration which is apparent during this
test can indicate deterioration in the undercarriage legs, fastenings or mechanism and must be
corrected.
Inspect all rod ends to ensure condition, freedom of movement and secure lock-nuts.
Visually inspect nose leg steering “soft link” (where equipped). Ensure the rubber is in good
condition and that all the parts and hardware are not damaged or corroded.
Check brake master cylinder and refill with automotive brake fluid
(DOT 3 or DOT 4)
Bleed the brake
system of any trapped air whenever there is a spongy response on the brake lever.
Check that discs are straight, not excessively corroded and not worn outside of limits.
Check for brake fluid leaks, chafing or other damage to brake hoses. Ensure that the brake linings
have sufficient wear remaining to reach the next scheduled maintenance. Check brake assemblies
& master cylinder for rubbing, damaged or missing hardware or corrosion. Carry out a brake
operational check. Refer to Section 8.19 for filling and bleeding of the brake system.
CAUTION
The JABIRU uses automotive brake fluid (DOT 3 or DOT 4). DO NOT use Aircraft hydraulic fluid
(mineral based) or damage to the brake system will result.
4.11 AIRFRAME 100-HOURLY
As all possible circumstances cannot be listed here, the following is provided as guidance only. A
critical, trained eye is required and inspections should include, but not be limited to, the following.
Inspect the aircraft exterior for cracks, dents, abrasions, corrosion or signs of fretting or rubbing.
Check for missing or damaged hardware.
Check for whitening of unpainted fiberglass areas (an indication of damage).
Check for movement of wing attachments and threaded bushes, movement of undercarriage
attachments, loosening of firewall/engine attachments.
For each wing, hold the tip and shake up-and-down and fore-and-aft. If there is any slop in the wing
or strut attachments it will be evident by feel and audibly. Any slop in these connections must be
addressed.
Inspect windows and windshield for cracking and scratches.
Inspect doors & seals for condition. Check for cracks and signs of rubbing or degradation.
Inspect seatbelts & shoulder harnesses for condition. Ensure all latches function correctly and do
not have excess slop. Check joint pin between shoulder and lap belts and ensure it is secure and
the connection solid.
Inspect the seat structure. Check for cracks or damage. Remove the seat covers and pull fore and
aft on the top of the seat back, watching for signs of de-lamination or other damage to the seat back.
Inspect instruments & markings for security and indications of damage.
Inspect instrument plumbing & wiring for damage, kinks and security.
Inspect the instrument panel, shock mounts, decals & labels