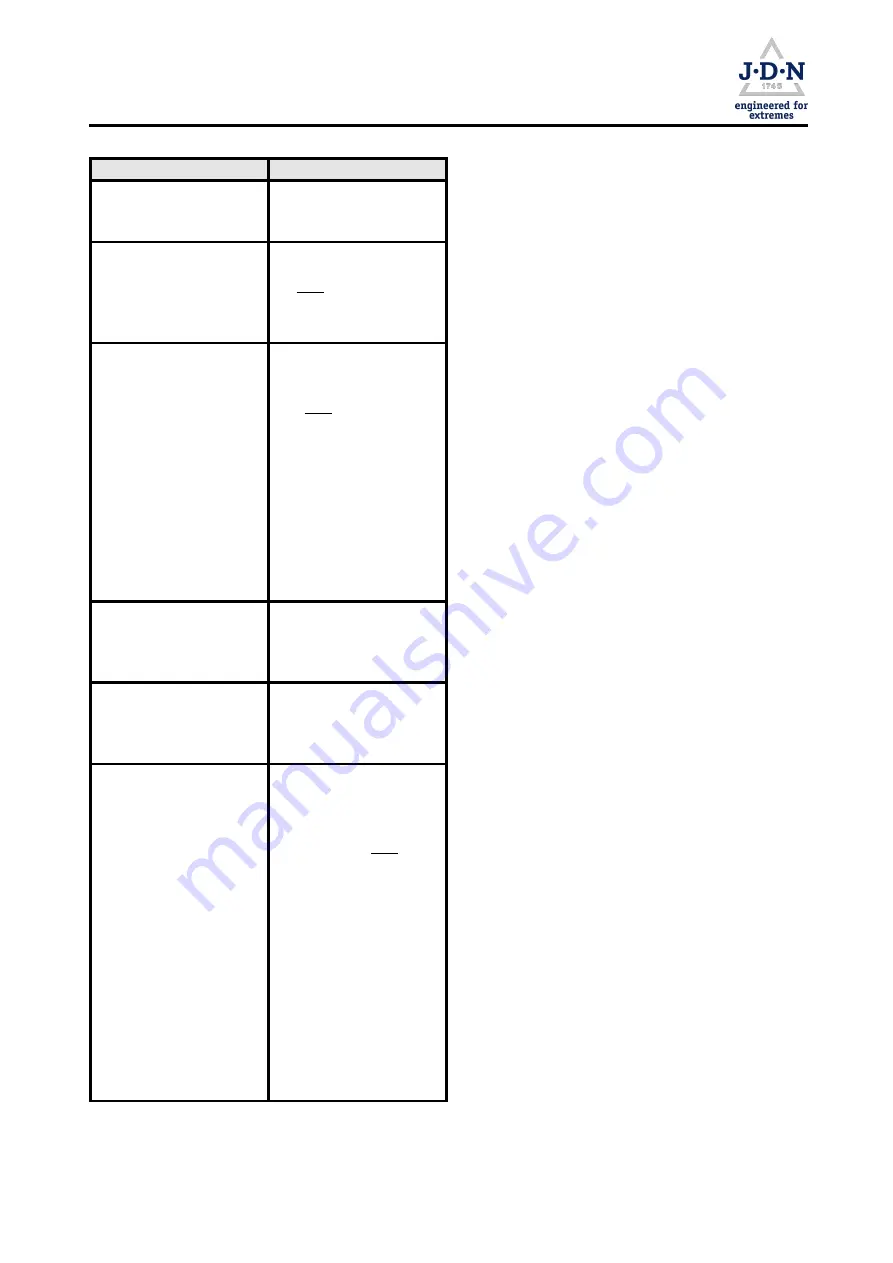
P
RODUCT INFORMATION
Application area
Operating material
Motor lubrication
JDN high performance
grease, item no. 11904
(250ml)
Engine lubrication for
operation with oiler
Air lubricator “D”, kine-
matic viscosity about
30
mm
2
s
(cSt) at 40
◦
C,
possibly with anti-icing
agent
Chain lubrication
Chain oil or vehi-
cle motor oil, kine-
matic viscosity about
150
mm
2
s
(cSt) at 40
◦
C,
or special lubricant
from J.D. Neuhaus.
In areas with extreme
corrosion potential,
such as offshore, a
lubricant with a particu-
larly powerful corrosion
protection is to be
used.
Motor corrosion pro-
tection (not applicable
if using the JDN high
performance grease)
Non-gumming preser-
vative oil with corre-
sponding effective
duration
Engine cleaning (not
applicable if using the
JDN high performance
grease)
Pure petroleum
Lubrication for bearings
and gearbox (also for
open gears)
Lithium-saponified
grease, worked pen-
etration 265-295
(0,1mm), base oil
viscosity: 190
mm
2
s
(cSt)
at 40
◦
C, dropping point:
180
◦
C,
Application temper-
atures: -20
◦
C to +
120
◦
C,
Designation according
to DIN 51825: KP2K-
20, active ingredients:
EP additives (to reduce
wear) and ageing pro-
tection; water-resistant
and anti-corrosive
3.10. Explosion protection
The basis for the following information is an expert
statement by DMT Gas & Fire Division regarding
the use of JDN hoists, trolleys and cranes in po-
tentially explosive areas based on the European
directive 94/9/EC (“ATEX 100a”). DMT is accred-
ited for the testing devices and protective systems
for proper use in potentially explosive areas.
Load chain
To ensure the required earthing,
badly rusted chains may no longer be used in
zones 1 and 21 as well as in devices of category
M2. For, depending on the degree of corrosion,
the conductivity of the chain may deteriorate so
that it is no longer sufficient.
Hoses
Hoses in zone 1 must have a sufficiently
low surface resistance of less than
10
9
Ω
in order to
avoid electrostatic ignition hazards. Otherwise (at
>
10
9
Ω
) the hoses for explosion groups I, IIA and
IIB must be
≤
∅
30
mm
and for explosion group IIC
≤
∅
20
mm
or they must have the evidence that
they cannot be dangerously loaded.
Materials for friction and impact hazards
Fric-
tion and impacts may cause individual sparks that
may cause a risk of ignition for gases of the ex-
plosion group IIC, hydrogen sulphide or ethylene
oxide as well as for light metal or other impact-
sensitive dusts. Therefore, spark formation caused
by mechanical influences must be prevented here.
The chain and load are always to be moved in
such a way that sliding and/or frictional contact
with other systems and components is excluded.
If circumstances do not permit this, it is necessary
to ensure an absence of explosive atmospheres
during operation.
Impacts between special material pairings result
in an increased ignition hazard. This does not ap-
ply to corrosion-resistant steel or cast iron against
aluminium, magnesium or corresponding alloys.
This especially applies in the presence of rust or
rust film. Rust (also rust film) may form at the fric-
tion points, especially on the chain and on the load
hook. The following applies for all zones: For the
intended use of your product, it is to be ensured
that no rust is present at the aforementioned fric-
tion points and that material combinations from the
aforementioned light metals and steel (exceptions
Page
22
of 64
Doc.-No.: VA049318-10-OM-EN-0319-64-2