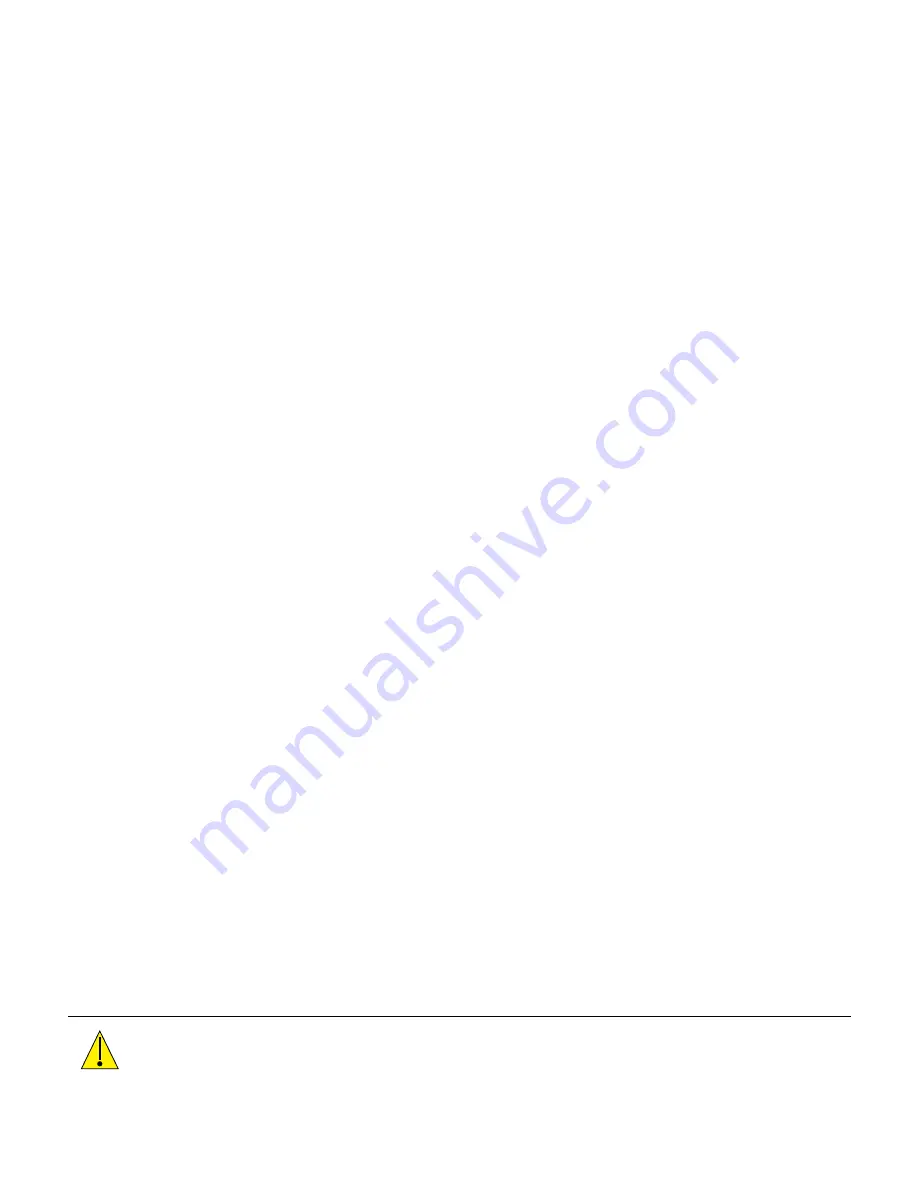
98
Frequency
The sensor should be cleaned periodically. The frequency required will vary by installation. In a new
installation, it is recommended that the sensor be cleaned only if a 1-Point Calibration cannot be success
fully performed.
Cleaning Procedure
The most important maintenance item for the sensor is to keep the optical paths clean of plate-out or
other coatings. In electroless applications, the sensor should be etched when the tank is etched, or when
ever plate-out is evident. If plate-out does occur in the sample line or sensor, etch the system as you
would the tank.
Avoid any mechanical cleaning of the optical surfaces to avoid scratching them. Chemical cleaning is
preferred over mechanical cleaning methods. Plate-out should be removed using nitric acid or a persul
fate or peroxide/sulfuric etch.
7.2 pH Electrode Maintenance
The pH electrode requires periodic cleaning and calibration. These electrodes are like batteries and their
voltage outputs will change with time even if they are not being used. After installation, the rate of change
increases, and factors such as temperature, extremes of pH, abrasion and chemical attack will increase the
required frequency of calibration. If the process solution contains oils, scale or other solids, the electrode
surfaces will tend to coat, its response time will slow down and cleaning will be required.
The frequency of cleaning and calibrating will vary greatly depending upon the application, the factors list
ed above, as well as the accuracy of control you require. The best way to determine the optimum number of
days between calibrations is to remove the electrode from the process periodically (weekly in clean water
applications, daily in dirty or hot applications) and check its accuracy in a buffer solution. If using manu
-
al temperature compensation, remember to change the temperature from that of the process to that of the
buffer. If the accuracy of the reading is within your required tolerances, and the speed of response is good,
replace the electrode in the process. If not, clean the electrode and perform a
two point calibration.
The method of cleaning the electrode will depend upon the coating, as well as the materials of construction
of the electrode. Do not use a solvent that will attack the electrode! Care must be taken to avoid scratching
the pH electrode’s glass, as this will shorten its life.
Oily coatings should be removed with a mild detergent or isopropyl alcohol. Hard scales such as calcium
carbonate can usually be removed with a dilute hydrochloric acid solution. Soft coatings can be removed
using a soft cloth or soft toothbrush.
A two point calibration should always be performed after cleaning the electrode.
Because the electrode signal is so sensitive, the condition of the cable and connectors between the electrode,
preamplifier and controller is critical. Make sure that all electrical connections stay clean and dry. Never
splice the cable prior to preamplification. Replace the cable if there is any sign of damage.
8.0 TROUBLESHOOTING
CAUTION
: Disconnect power to the controller before opening front panel!
Troubleshooting and repair of a malfunctioning controller should only be attempted by qualified personnel using cau
-