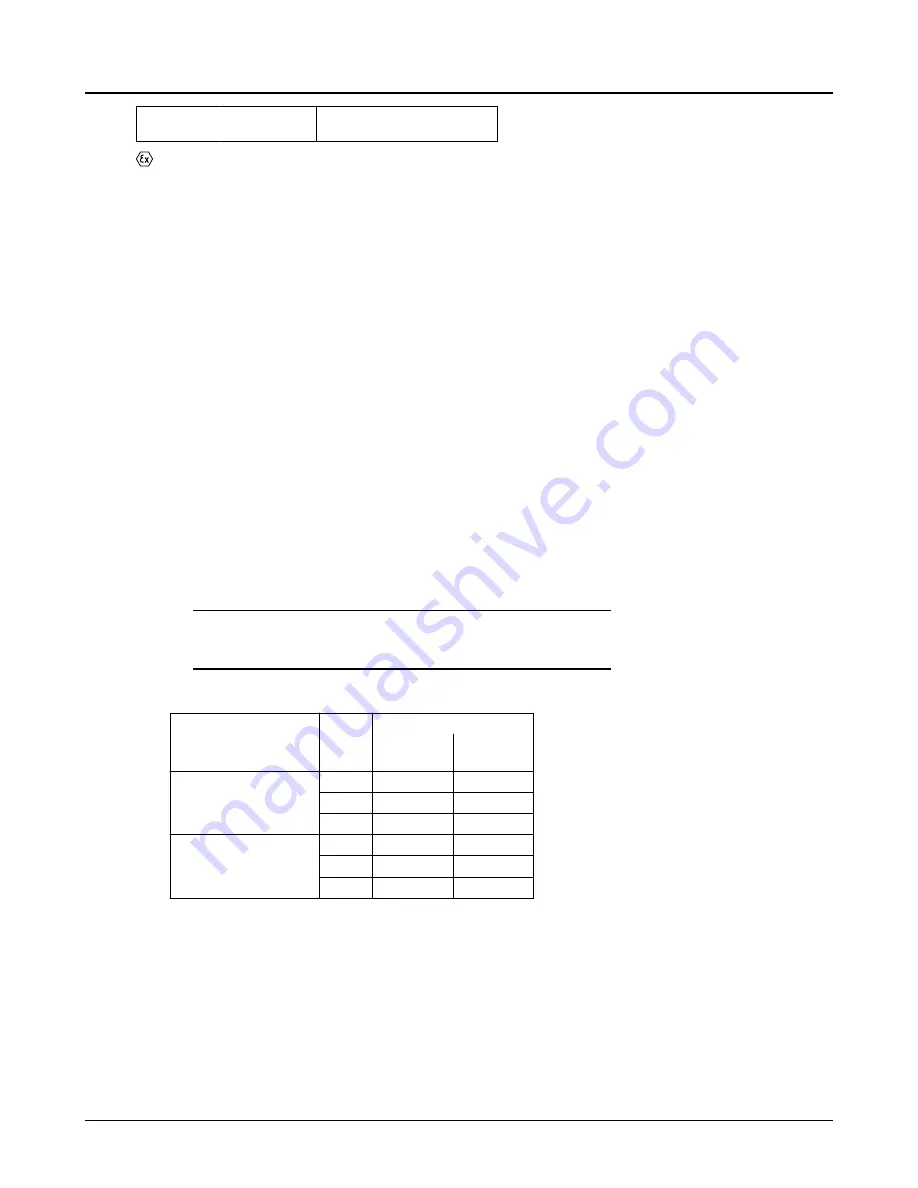
clearance a
(mm)
worn
max. 1,7
When the wear limits has been reached or exceeded, the worn parts must be replaced.
For volute casings (102V) with a wear ring (502.11) and cover casings (161) with a wear ring (502.31)
there are the following possibilities to restore the correct clearance:
1.
Renew impeller (230) and wear ring. Then the original measures are restored.
2.
A customized wear ring (bored to fit) can be supplied to avoid replacement of the impeller. Please
contact factory for details.
When volute casing (102V) or casing cover (161) without wear ring must be repaired, a wear ring can be
installed to renew pump performance. Re-machining of the volute casing and / or casing cover is re-
quired. Please contact the factory for details and assistance.
6.15 Reassembly
6.15.1 Mounting
1.
Re-assemble the pumps using the reverse order of steps as completed for pump disassembly.
However the following observations should be considered:
•
Pay attention to the utmost cleanliness when re-assembling the pump.
•
For tight tolerances, e.g. between shaft sleeve (433) and shaft (210) or impeller (230) and
shaft (210), as well as thread, use a suitable anti-galling compound (e.g. Molykote/Never-
Seeze), so that the assembly and the next disassembly will be easier.
NOTICE:
Anti-galling compound must be compatible with the pumpage.
Screws should be tightened, with the following torque:
Location
Screw
Size
Screw torque in Nm
Lubricated
threads
Dry threads
Casing screws
M12
35
50
M16
105
150
M20
210
305
All other screws
M10
35
50
M12
60
90
M16
150
220
Do not use excessive force.
2.
Before mounting the second bearing on the shaft push in the circlip (932.51) between the two bear-
ings.
3.
Before mounting new bearings, warm them up to 80°C | 176°F in an oil bath or using a bearing
heater. If necessary use a tube to force the inner ring onto the shaft by gentle taps with a hammer.
Hold the outer ring to avoid vibrations of the balls.
4.
When bolting together the bearing bracket (330) with the bearing bracket lantern (344) and the
bearing bracket lantern with the volute casing (102V), screws should be positioned in the centre of
the drilled holes. Failure to do so could result in improper oil setting.
6.15 Reassembly
40
Model ICP, ICPI, ICPH, ICPIH Installation, Operation and Maintenance Instruction
Содержание Goulds Pumps ICP
Страница 1: ...Installation Operation and Maintenance Instruction Model ICP ICPI ICPH ICPIH ...
Страница 2: ......