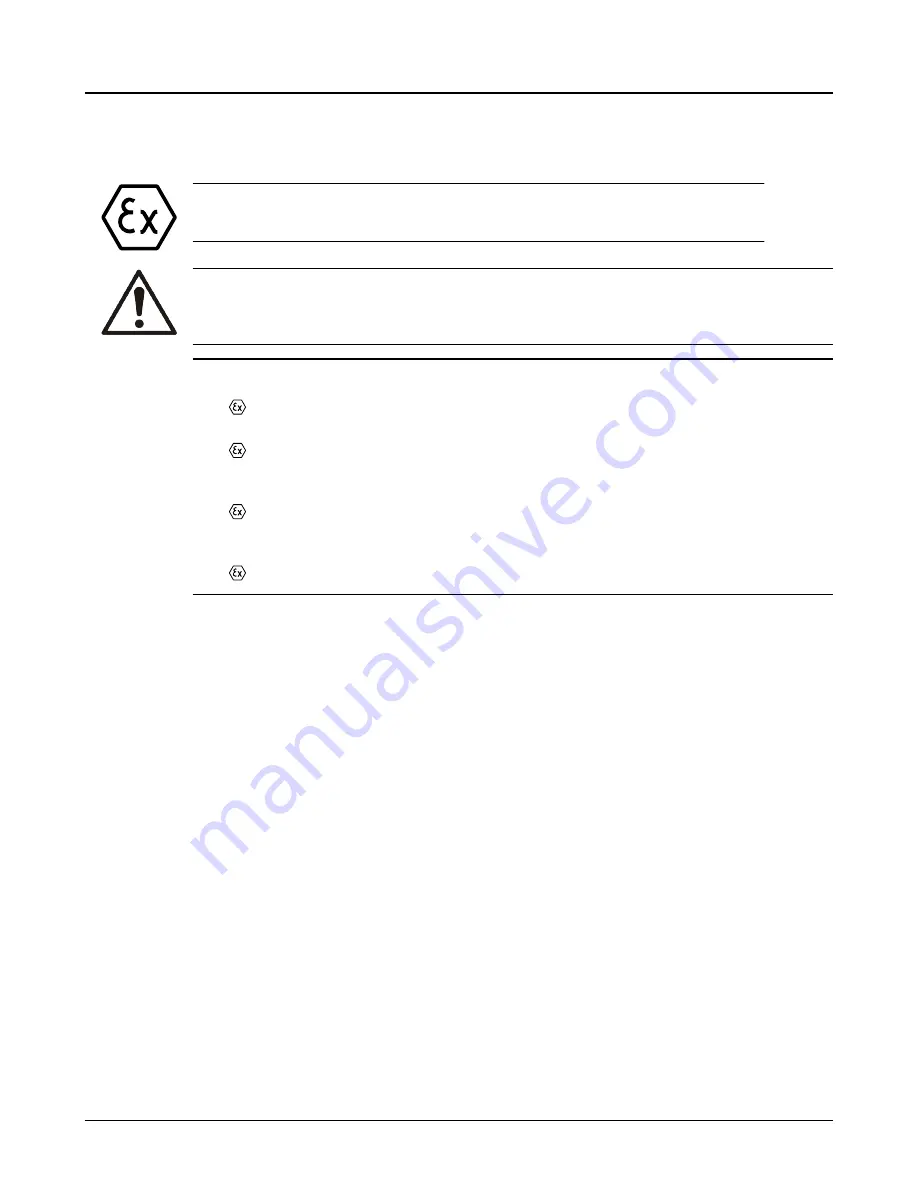
5.6 Shaft sealing with a mechanical seal
Precautions
WARNING:
The mechanical seal used in an Ex-classified environment must be properly certified.
CAUTION:
Running a mechanical seal dry, even for a few seconds, can cause seal failure and physical
injury. Never operate the pump without liquid supplied to the mechanical seal.
NOTICE:
•
The mechanical seal must have an appropriate seal-flush system. Failure to do so will
result in excess heat generation and seal failure.
•
Cooling systems such as those for bearing lubrication and mechanical-seal systems
must be operating properly to prevent excess heat generation, sparks, and premature fail-
ure.
•
Sealing systems that are not self-purging or self-venting, such as plan 23, require
manual venting prior to operation. Failure to do so will result in excess heat generation
and seal failure.
•
Follow seal manufacturer's guidelines for proper seal installation procedures.
Shipping
Pumps may be shipped with or without a mechanical seal installed.
Cartridge-type mechanical seals
Cartridge-type mechanical seals are commonly used. Cartridge seals are preset by the seal manufactur-
er and require no field settings. Cartridge seals installed by the user require disengagement of the hold-
ing clips prior to operation, allowing the seal to slide into place.
Other mechanical seal types
For other types of mechanical seals, refer to the instructions provided by the seal manufacturer for instal-
lation and setting.
5.7 Connection of sealing liquid for mechanical seals
Seal lubrication is required
Seal faces must have liquid film between them for proper lubrication. Locate the taps using the illustra-
tions shipped with the seal.
5.6 Shaft sealing with a mechanical seal
54
3640 i-FRAME API Type BB2 2-Stage / ISO 13709 2nd Ed. API 11th Ed. Installation, Operation, and Maintenance Man-
ual
Содержание Goulds Pumps i-FRAME 3640
Страница 2: ......