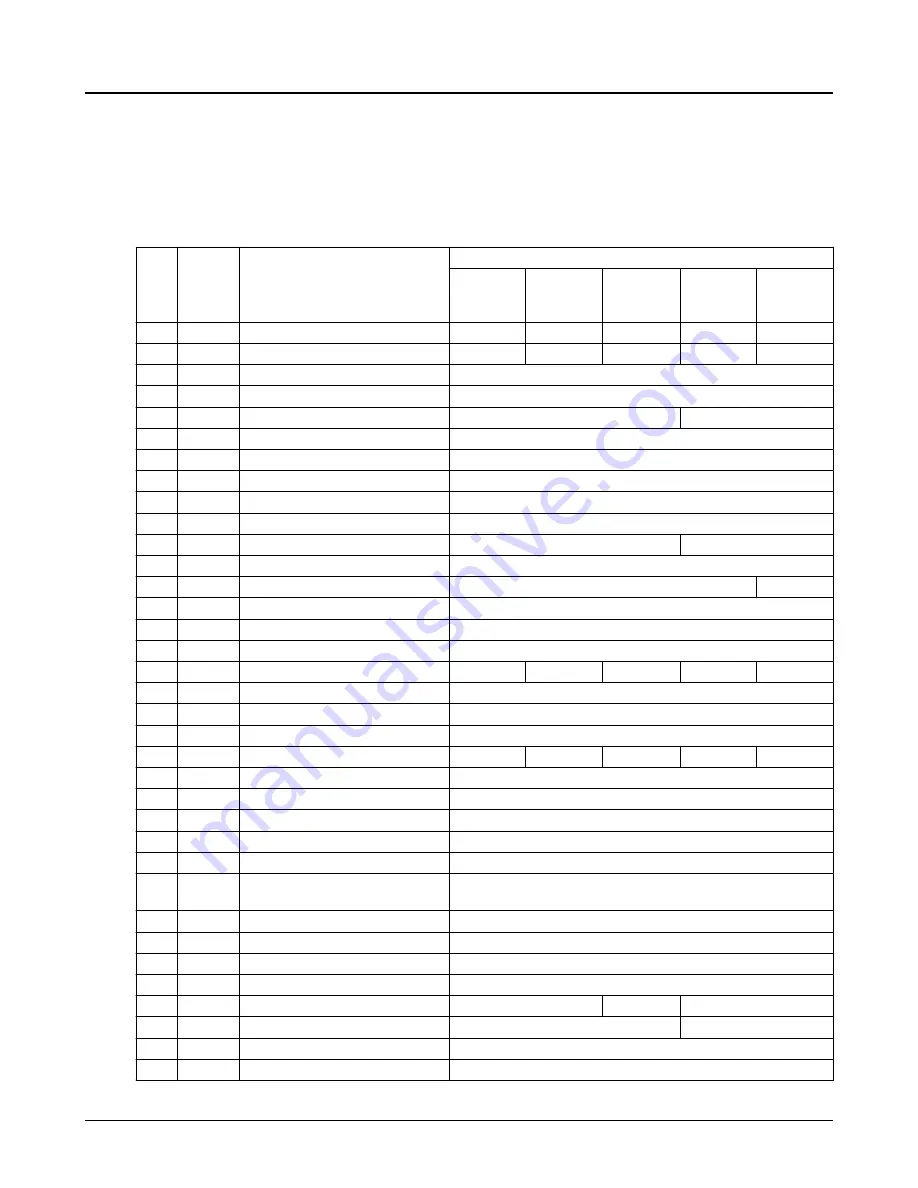
8 Parts Listings and Cross-Sectionals
8.1 Parts list
Table 29: Construction material and quantity
Item Quantity Part name
Pump Material
All D.I.
D.I. With
316 SS im-
peller
All 316SS
All
CD4MCu
All Alloy
20
100
1
Casing
1012
1012
1203
1216
1204
101
1
Impeller
1013
1203
1203
1216
1204
105
1
Lantern Ring
PTFE
106
1 set
Stuffing Box Packing
Non-asbestos braid
107
1
Gland—Packed Box
1203
1204
108
1
Frame Adapter
1013
109C 1***
Outboard Bearing End Cover
1001
112A 1
Outboard Bearing
Double row angular contact (duplex pair for LTi)
113
2
Plug—Grease Relief
2210
113B 1
Plug—Oil Fill
2210
122
1
Shaft—Without Sleeve
2229
2230
122
1
Shaft—With Sleeve
2238
126
1
Shaft Sleeve
2229
2230
134
1
Bearing Housing
1001
136
1
Bearing Locknut
Steel
168A 1
Radial Bearing
Single row ball
184
1
Seal Chamber/Stuffing Box Cover 1012
1012
1203
1216
1204
193
2
Grease Fitting
Steel
228
1
Bearing Frame
STi 1013, All others - 1001
236A 10
Cap Screw—Bearing Clamp Ring
2210
239
1
Support, Casing
–
–
2201*
2201*
2201*
241
1
Frame Foot
1001
248
1
Oil Thrower
2210
250
1
Gland—Mechanical Seal
Material varies
253B 1
Bearing Clamp Ring
2210
319
1
Sight Glass
Glass/steel
332A 1
Outboard Labyrinth Seal w/O-
rings
Brass ASTM B505-96
333A 1
Inboard Labyrinth Seal w/O-rings
Brass ASTM B505-96
351
1
Casing Gasket
Aramid fiber w/EPDM
353
4
Gland Stud
2228
355
4
Gland Stud Nut
2228
358
1
Plug—Casing Drain
2210
2229
2230
358Y 1 ***
Plug, Impeller
2229
2230
360C 1 ***
Gasket—Thrust End Cover
Buna
360D 1
Gasket—Frame-to-Adapter
Buna
8 Parts Listings and Cross-Sectionals
156
Model CV 3196 i-FRAME Installation, Operation, and Maintenance Manual
Содержание Goulds Pumps CV 3196 i-FRAME
Страница 1: ...Installation Operation and Maintenance Manual Model CV 3196 i FRAME ...
Страница 2: ......
Страница 171: ...9 1 Certificates of conformance Model CV 3196 i FRAME Installation Operation and Maintenance Manual 169 ...
Страница 174: ...9 1 Certificates of conformance 172 Model CV 3196 i FRAME Installation Operation and Maintenance Manual ...