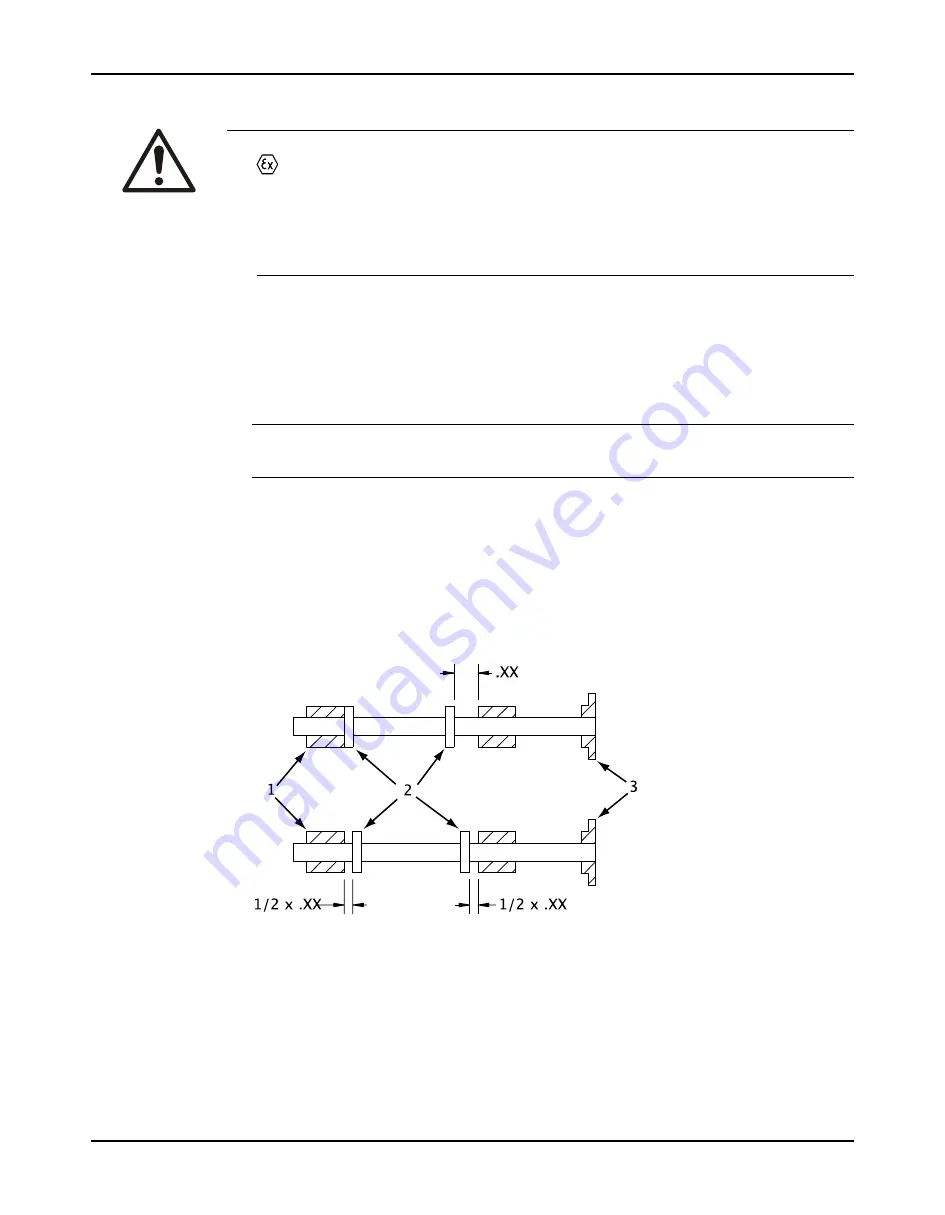
Commissioning, Startup, Operation, and Shutdown
Couple the pump and driver
WARNING:
•
Always disconnect and lock out power to the driver before you perform any installation or
maintenance tasks. Failure to disconnect and lock out driver power will result in serious physical
injury.
• Electrical connections must be made by certified electricians in compliance with all international,
national, state, and local rules.
• Refer to driver/coupling/gear manufacturers installation and operation manuals (IOM) for specific
instructions and recommendations.
•
1. Check the gap between the coupling hubs against the dimensions shown on the elevation
drawing or as stamped on the coupling hub. For any necessary adjustment, move the
driver not the pump.
Motors with sleeve bearings may be manufactured with 1/4 or 1/2 in. (6.35 or 12.7 mm) end
movement (float) in the motor rotor. For limited end-float arrangement, the gap between the
coupling halves must be set in a different manner. If specific directions are not indicated in
the motor instructions, then follow this procedure:
NOTICE:
If the driver was mounted at the factory, the setting for the coupling is already determined.
a) Slide the rotor towards the outboard end of the motor as far as it will go and mark the
shaft at the motor frame.
b) Slide the rotor towards the inboard end of the motor as far as it will go and mark the
shaft again.
The distance between the marks should be either 1/2 or 1/4 in. (6.35 or 12.7 mm) if the
motor is arranged for limited end-float travel.
c) Scribe a third mark on the shaft halfway between the scribe marks made in the previous
steps.
d) Clamp the rotor in place.
1. Sleeve bearing
2. Thrust collar
3. Coupling
2. Use the instructions from the coupling manufacturer to lubricate and install the coupling.
3. Check the angular and parallel alignment of the coupling halves. See Pump-to-driver
alignment in the Installation chapter.
Model 3610, API Type BB1 API 610 11th Edition Installation, Operation, and Maintenance Manual
37