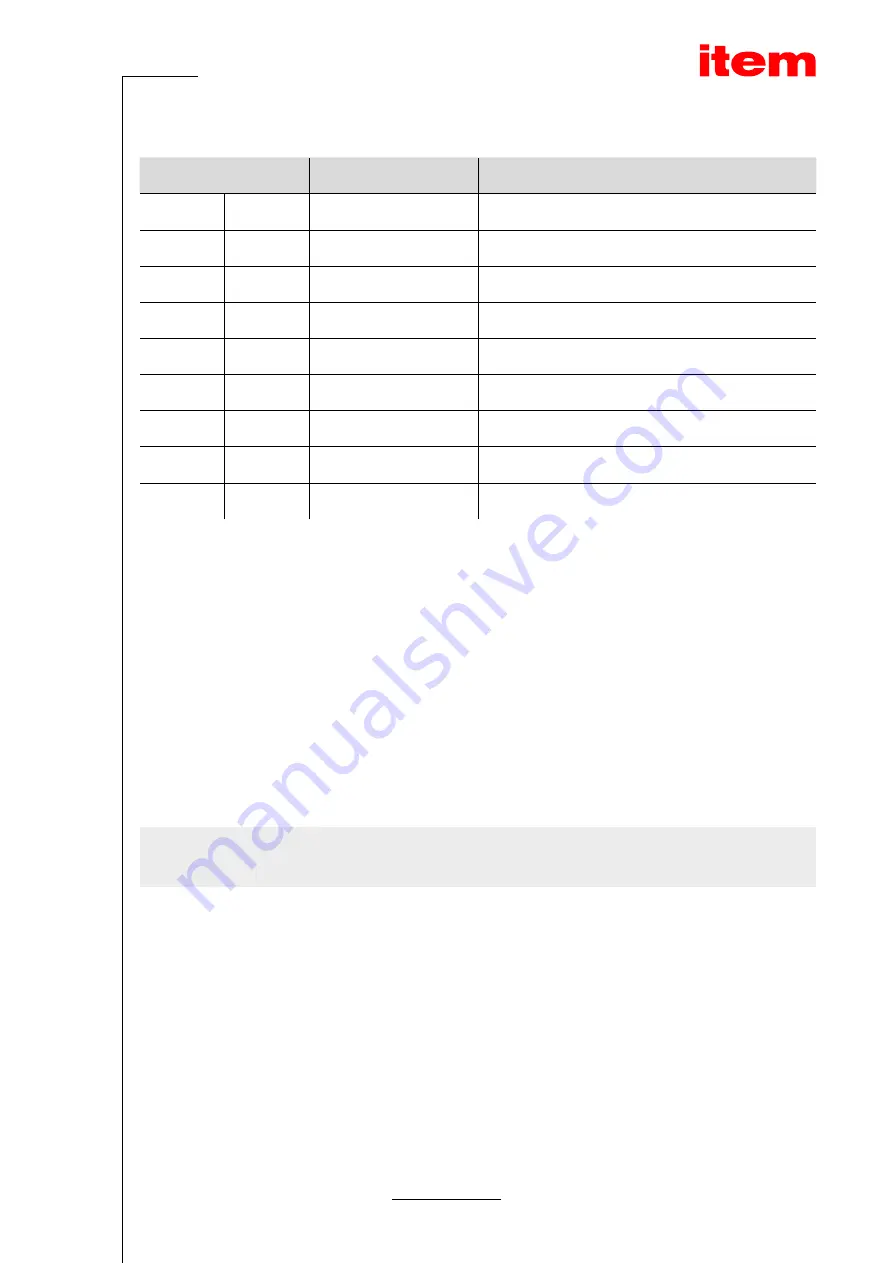
67
item Controller BL 1-04 /C
― Product manual
Steckerbelegung [X4]
Pin
Name
Specification
1
Not used
6
GND
CAN-GND, directly coupled to GND in the servo drive
2
CANL
CAN low signal line
7
CANH
CAN high signal line
3
GND
See pin no. 6
8
Not used
4
Not used
9
Not used
5
Shield
Connector for the cable shield
*) To terminate the CAN bus at both ends, an external terminating resistor is required.
Cable type and configuration [X4]
The cable names that are stated refer to cables made by Lapp. However, it is also possible to use comparable cables from
other manufacturers, for example Lütze or Helukabel.
Technical data of the CAN bus cable: 2 pairs of 2 twisted cores, d ≥ 0.22 mm2, shielded, loop resistance < 0.2 Ω/m, charac
-
teristic impedance 100-120 Ω
LAPP KABEL UNITRONIC BUS CAN; 2 x 2 x 0.22; 7.6 mm, with CU shielding
For highly flexible applications:
LAPP KABEL UNITRONIC BUS CAN FD P; 2 x 2 x 0.25; 8.4 mm, with CU shielding
9.11 Connector: I/O interface [X1]
The BL 1-04 /C servo drive has two differential inputs (AIN) for analogue input voltages in the range of ±10 V.The inputs AIN
and #AIN are connected to the control system via twisted cables (twisted-pair type). Alternatively, it is also possible to use a
shielded cable.
If the control system is equipped with single-ended outputs, the output is connected to AIN and #AIN is connected to the
reference potential of the control system. If the control system is equipped with a differential output, it must be connected 1:1
to the differential inputs of the servo drive.
The reference potential GND24 must be connected to the reference potential of the control system. This is necessary in order
to prevent the differential input of the servo drive from being overridden by high "common-mode interference".
Despite the differential design of the analogue input, using unshielded cables for the analogue signals is not recommended,
since interferences, e.g. caused by switching contactors, or output stage interferences of the converters can reach high
amplitudes.
The 24 V connections inside the control cabinet can be made without a shield. In the case of long cables (l > 2 m) towards the
PLC or outside the control cabinet, shielded cables must be used. The shields of these cables must be connected to PE on
both ends. The cable shield can then be connected to the back panel of the control cabinet, for example.