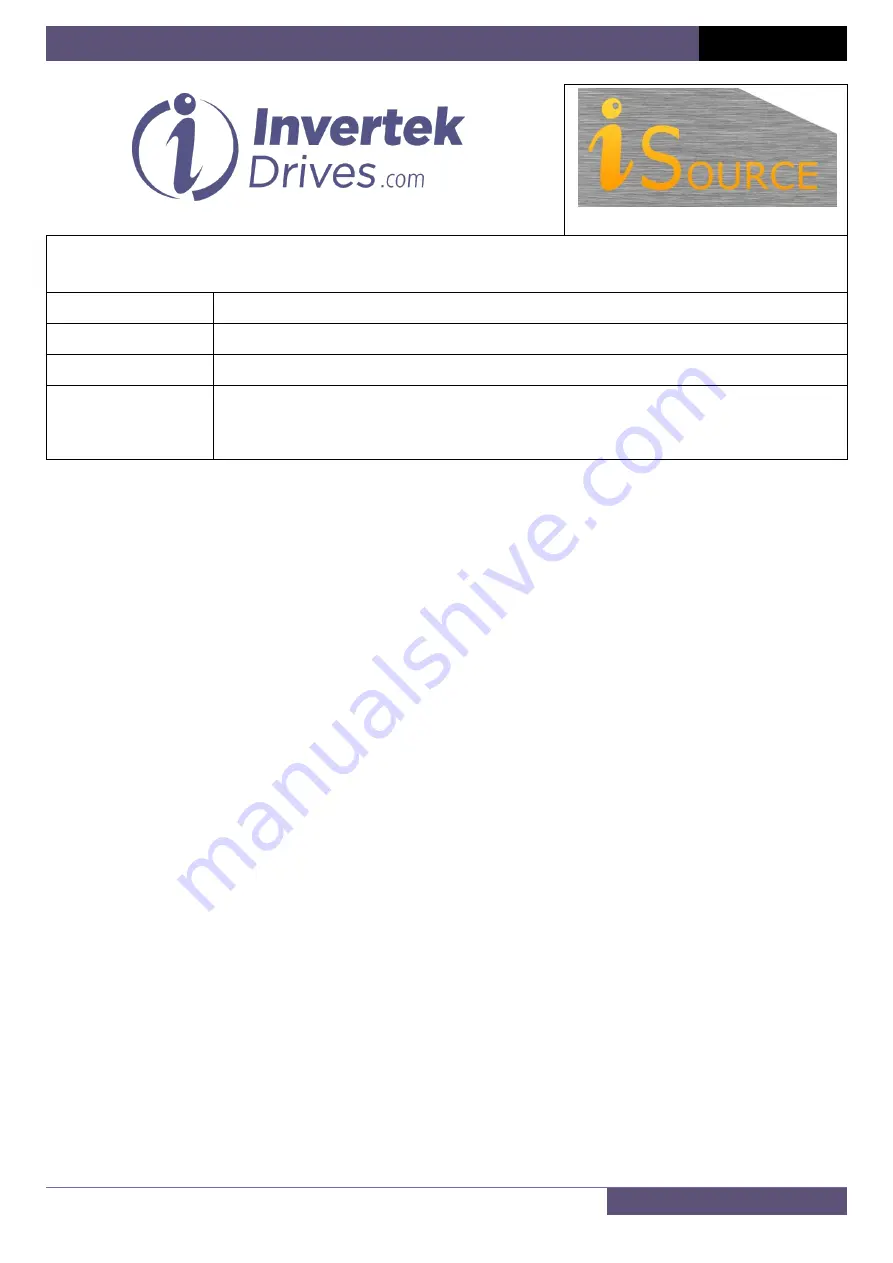
Application note AN-ODV-2-068
22 October 2014
AN-ODV-2-068 Using Optiflow Multi Pump Cascade Control
1
Optidrive Applications Support Library
Application Note AN-ODV-2-068
Title
Using Optiflow Multi Pump Cascade Control
Related Products Optidrive HVAC
Level
3
1 – Fundamental - No previous experience necessary
2 – Basic – Some Basic drives knowledge recommended
3 – Advanced – Some Basic drives knowledge required
4 – Expert – Good experience in topic of subject matter recommended
Overview
Optidrive HVAC features a unique Optiflow system, designed to simplify the operation of multiple pump sets, typically in Duty /
Standby or Duty / Assist / Standby configurations. The system allows up to five drives, each controlling an individual pump to be
connected together, and provides automation of the following functions.
Automated changeover between Duty and Standby Pumps in the event of a pump fault
Automated changeover based on time to allow balanced operating time between all pumps
Automated Staging / Cascade Control of Duty and Assist Pumps in closed loop pressure or flow control applications
Isolation of any individual pumps is possible whilst maintaining operation with the available pumps
Operating Principle
The Optiflow system operates on the principle that one drive is designated as the Control Master. All other drives operate as
Slaves. The Master drive determines which pumps should operate at any given time, to ensure that only the required number of
pumps are operating, and operating time is balanced between all pumps.
Control functions are carried out using the on-board RJ45 connector. The Control Master drive must be address 1. The
connected Slaves must then have incremental addresses, starting from address 2.
All external control connections, such as feedback transducers, external setpoint and controls are made to the Master drive
only. Slave drives simply require an enable input, to allow switching of individual slaves when required. Motor thermistors can
also be connected back to each slave drive, and fieldbus connections for remote monitoring can also be made if required.
Installation
Basic installation of the drive, such as incoming mains power and motor connections should be carried out according to
information provided in the User Guide.
Any required control connections should then be made to the Master drive, e.g. a pressure feedback transducer can be
connected for closed loop pressure control, or an analog signal for direct speed control can be connected.
Each Slave drive requires the inhibit circuit to closed to operate (refer to the User Guide for further information), and an enable
signal on digital input 1. A motor thermistor can also be connected and configured if required.
Basic Commissioning
Once installation has been completed, and all drives can be safely powered on, commissioning should be carried out according
to the following procedure.
1.
Set the drive addresses. Each drive must have a unique individual address, starting with the Control Master drive as
address 1, and increasing for each connected slave (e.g. first slave is address 2; second slave is address 3 etc.). The
address is set in Parameter P5-01.
2.
Configure the motor nameplate details into each drive. For each drive and pump combination, the correct motor
nameplate details for the connected motor must be entered into the relevant drive parameters. This ensures that the
motor is correctly protected and controlled by the drive. The settings should include