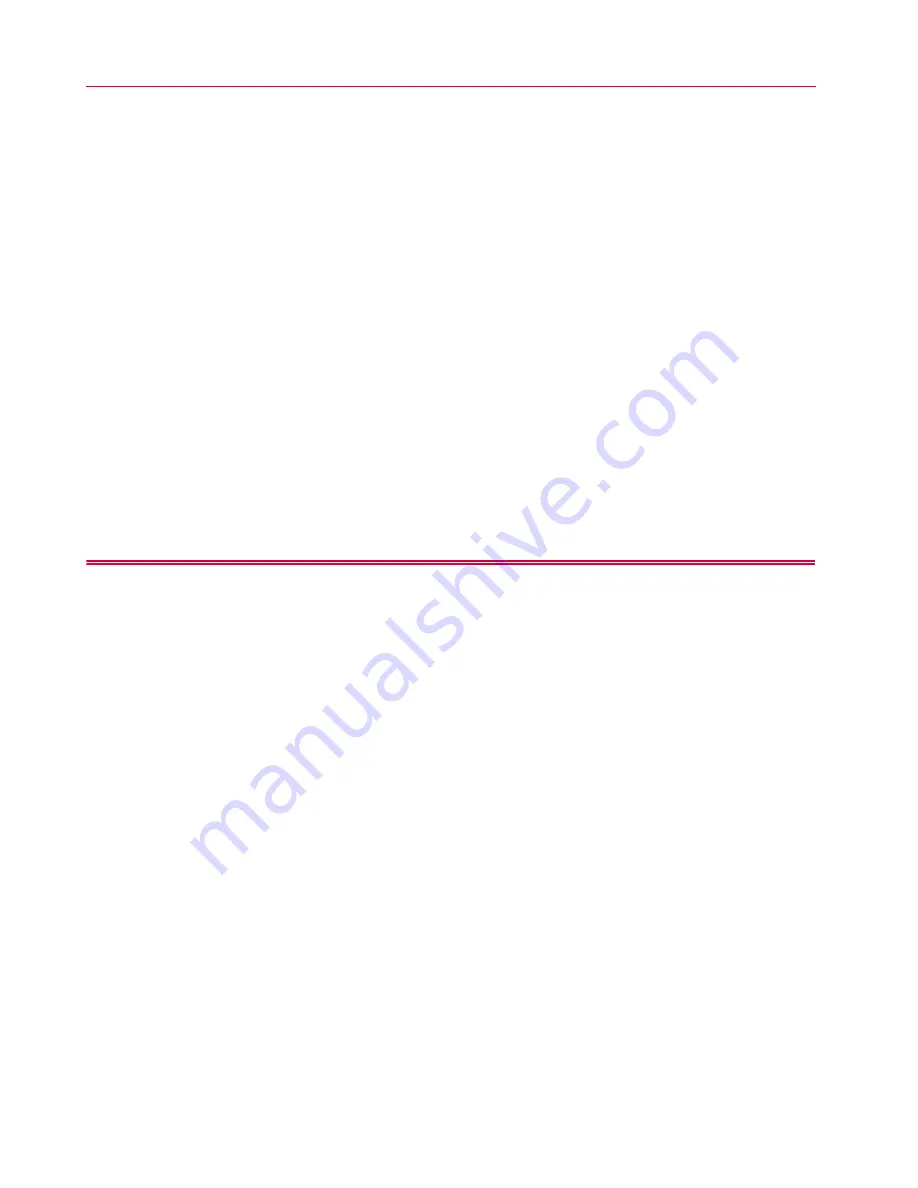
Chapter 3: Additional System Details
36
M47-17036-EN
Crosshead support collars
All KPX frames with either a J1-style or J3-style crosshead have crosshead support collars that mount to
each column, as shown in
. The crosshead support collars have several purposes:
•
During normal operation, the crosshead support collars are to be positioned so that they are in
contact with the bottom of the crosshead and the cap screws of the crosshead support collars are to
be tightened to the torque specified in the System Operating Instructions (supplied separately).
When properly placed and torqued, the crosshead support collars will support the weight of the
crosshead, guide plate and accessories, if a mechanical or hydraulic failure should occur.
•
For frames with a J1-style crosshead, the crosshead support collars are used during adjustment of
the crosshead.
•
For frames with a J3-style crosshead, the crosshead support collars are used during adjustment of
the crosshead travel range.
Load measurement
A strain gauged load cell is used to measure the force applied to the test specimen. The load cell (14,
) is mounted to the end of the hydraulic cylinder rod (10). This mounting
arrangement provides a load measuring system that is independent of the hydraulic system. This means
that the force measured by the load cell is free of interference due to piston friction and hysteresis; it is a
direct force measurement.
Caution
The controlling software is equipped with overload protection for the load transducer. The
overload protection should prevent damage to the load transducer during a test by shutting
off the HPS when an overload condition occurs.
Position measurement
A position encoder is used to determine the position of the piston inside the hydraulic cylinder. Two
position encoder resolution options are available. For specifications, refer to information provided in the
System Operating Instructions (supplied separately). All encoders are digital quadrature style encoders.
KPX frames with the C3 position option use a magnetostrictive-type encoder (see
). The
encoder is mounted to the stationary end of the hydraulic cylinder (4). The encoder rod (2) extends
through the cylinder body (4b) and into the piston (4a). The encoder magnet (3) is attached to the end of
the piston so that the encoder rod extends through the magnet. As the piston moves up and down, the
encoder magnet moves along the encoder rod. The position of the encoder magnet on the encoder rod
produces an electrical signal that is proportional to its position. As the position of the encoder magnet on
the encoder rod changes, the electrical signal changes. The electrical signal is transmitted to the
59 Series control unit.
KPX frames with the C4 position option use a linear position encoder that is mounted external to the
actuator rod.
For either type of encoder, the 59 Series control unit converts the signal into the relative position of the
hydraulic cylinder rod in relation to a stationary frame member.
Содержание 1000KPX-J3
Страница 16: ...Chapter 1 Introduction 16 M47 17036 EN This page is intentionally blank...
Страница 52: ...Chapter 3 Additional System Details 52 M47 17036 EN This page is intentionally blank...
Страница 56: ...Chapter 4 Parts Replacement 56 M47 17036 EN This page is intentionally blank...
Страница 57: ......
Страница 58: ...Product Support www instron com...