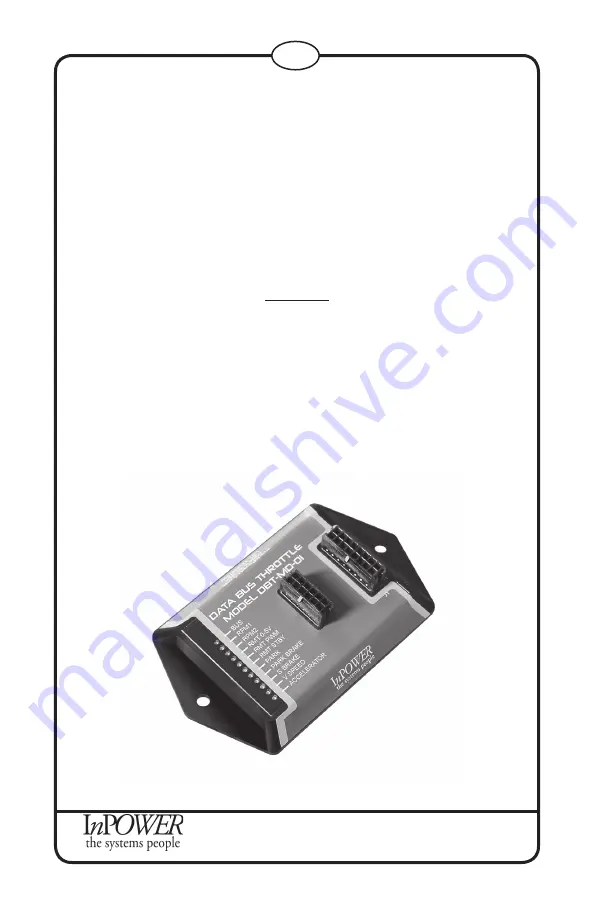
© Copyright 2016 InPower LLC
DBT-MD-01 Owner’s Manual
1
Document: OM-194
Version Code: A
Date: August 2016
Date: Sept. 14, 2016
OWNERS MANUAL
InPower Model DBT-MD-01
Contents
1. Introduction........................................ .................... 2
2. Installation Procedures........................... ............... 3
2.6 Harness Wire Table ........................................ 6
3. Operation ............................................................... 7
4. Mechanical Drawing .............................................. 9
5. Status LED and Troubleshooting ........................... 10
5.6 Troubleshooting Flowchart ............................. 11
6. Contact Us ............................................................. 12
Electronic Throttle Module and Databus Decoder
for Ford 2016+ Vehicles