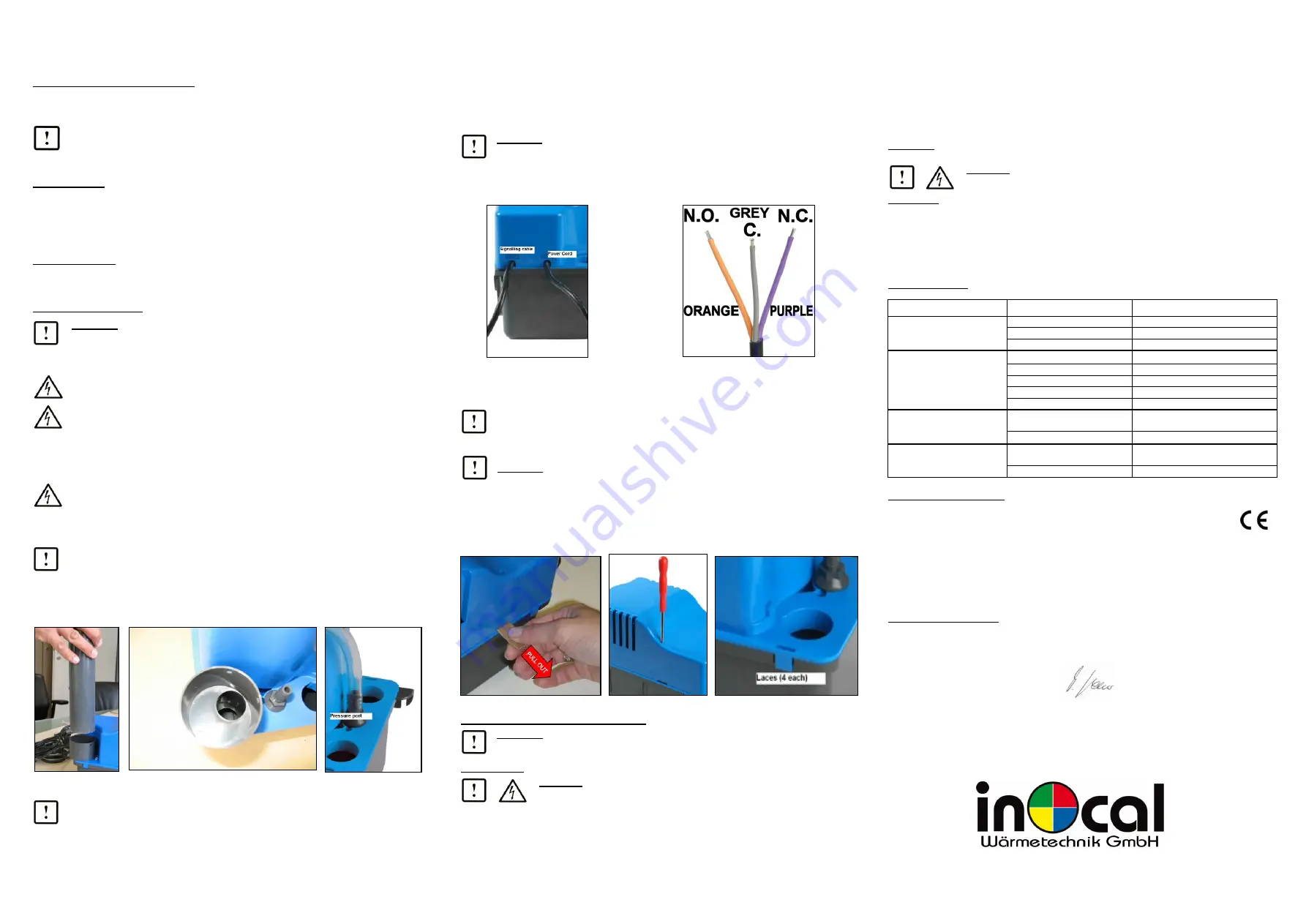
Condensate Pump Neotech 360
Instruction Manual
1.
Description and range of application
Fully automatic condensate removal pump designed to remove condensate from furnace burners,
gas or oil condensing boilers, air conditioners, refrigeration display cabinets and de-humidifiers
where drainage by gravity is not possible.
WARNING: Regulations of water authorities or other relevant authorities must be
obeyed when condensate is being disposed of. Condensate from condensing
boilers being operated with standard heating-oil (not low on sulphur) may not be
disposed of into the canalization without being neutralized. This is also true for condensing
boiler systems exceeding 200 KW.
2. Technical Data
Motor power output: P2 = 80 Watt
Max. flow: 360 l/h
Voltage: 230 V – 50 Hz
Max. head: 5,2 m WS
Nominal current: 0,6 A
Max. liquid temperature: 50° C
Operational voltage: 230 V – 50 Hz
3/8“ connection with 9 mm hose connector
Protection: IP 44
Weight: app. 2,5 kg
RPM: 2780
Cable with plug: Length 2,0 m
3. Scope of delivery
Ready to plug in pump with 2 metre power cable and signalling cable, inlet adapter, check valve and
instruction manual. The Neotech 360 – 6MT version also comes with discharge tubing (6m) which is
to be connected to the outlet side (check valve) which is supplied.
4. Installation and start up
WARNING: Read instructions completely prior to installing, operating or servicing
the pump! The installation may only be performed by a qualified person.
Check content for completeness and eventual damage prior to operation. Inform your dealer
immediately in case of any deficiency.
Never transport or remove the pump from the packaging by holding on to the
cable!
An orderly grounded mains supply and residual current circuit-breaker of max.
30mA disconnecting all phases is required for the operation of the pump.
Already existing outlets are to be checked for the existence of a residual current
circuit-breaker. Ensure that power cord is NOT plugged in when performing any
type of work on the pump.
4.1 Installation and inlet connection
The pump must be level (either on the floor or mounted on the wall) to ensure a proper operation.
The pump must be installed ensuring that it can not tilt and that it is properly
mounted!
The pump should be mounted close to the condensate drainage of the unit to be drained. The
connections from the unit to the pump are not included. Please ensure to use corrosion-resistant
and acid-resistant material when choosing the drainage pipes (e.g. PVC, PE, stainless-steel).
Condensate from condensing boilers is very aggressive and corrosive!
A standard high-temperature plastic wastewater tube (40mm) may directly be connected to one of
the three inlets by means of the supplied inlet adapter (see figure 2). Other pipes or tubing with a
smaller diameter may be safely fixed by running cable straps through the two holes in the adapter
and firmly tightening them.
Figure 1 - Inlet
adapter
Figure 2: Inserted inlet adapter
Figure 3
Under no circumstances may pipes or tubes be inserted into the tank because this
may lead to pump failure since the integrated float switch may be blocked!
Standard condensing boilers are equipped with a siphon trap. This must in all cases
be filled with water
prior to operation of the boiler and condensate pump. Failure to do so
may result in acidic gases reaching the pump and therefore destroying it!
4.2 Pressure connection
The pressure port is equipped with a check valve. PVC tubing with an inner diameter of 9mm is to
be tightly connected to the pressure port (accessory, model Neotech 360-6MT is equipped with 6 m
of PVC tubing), see figure 3.
The PVC-tubing is to be secured with a hose clamp (not supplied) avoiding any kinks, ties and
connected to the drain pipe of the canalization.
In case of an installation in the basement below the level of backed-up water (locally defined;
generally the upper edge of the street) it must be ensured that the pressure piping is lead above this
level and then connected downward to the drain pipe.
WARNING: In case of non-observance the basement may be flooded in the event of
a flow back from the canalization!
4.3 Signalling cable
In addition to the power cord (POWER), the pump is also equipped with a signalling cable (ALARM).
See figure 4
Figure 4 - Inlet adapter
Figure 5 - Contact configuration, signalling cable
The signalling cable (dry contact) can be used to either conduct a safety shutdown of the
condensing boiler (COM and NO) or to activate an external low voltage alarm system (COM and
NC). See figure 5 for contact configuration.
Please refer to the instruction manual of the condensing boiler for the connection
as a safety shutdown or to the manual of the alarm system for the connection as an
alarm.
4.4 Testing
WARNING: Pull out the tab before testing or operating (see figure6)
The operation of the pump can be tested by activating the test-switch without filling the tank by
using a screwdriver. Insert the screwdriver in the respective opening to activate the switch and start
the pump. The switch is deactivated by removing the screwdriver and the pump stops (see figure 7).
This test is only to be conducted briefly for a couple of seconds to avoid the pump from being
damaged due to running dry.
It is imperative to remove the screwdriver again!
Figure 6
Figure 7
Figure 8
5. Limitation of use and improper operation:
WARNING:
This pump
may
not to be used
for waste water, in particular liquids
containing solids
liquids with abrasive content as well as
flammable and explosive
liquids.
6. Maintenance
WARNING
:
Ensure that the power is disconnected before performing any
service or maintenance!
The proper function of the pump, its wear parts and its product life are mainly dependant on regular
servicing and maintenance of this unit. Particulates settle on the bottom of the tank in the course of
time. This sediment can lead to pump clogging and block the float switch. It is therefore
recommended to service the pump, piping, inlets and pressure port biannually and, if necessary,
clean the respective areas and parts. This is especially necessary in connection with the general
maintenance of the heating system prior to the start of the heating period. In the course of time and
especially after longer standstill period particulates, at times highly acidic, can affect or destroy parts
of the tank.
The upper part of the pump can be removed without the use of tools by carefully moving the 4 laces
on the upper part of the pump outward (see figure 8). The upper part can then completely be
removed and the float switch and the bottom part of the pump body as well as the tank (bottom part)
are freely accessible. These parts can now be washed with warm water and mild soap. After
cleaning, place the upper part on the lower (tank) part. A latching can be heard. Connect the pump
to the mains and fill water into the tank through one of the inlets. After having filled the tank with
about 1.5 l the system will start automatically and discharge the water into the canalization.
WARNING:
All points pertaining to installation and start up (see point 4) must be observed
when pump is returned to service.
WARNING
:
Unit must be disconnected from the power source before
servicing or performing pump maintenance!
7 . Warranty
The warranty period for this product is 24 months from date of purchase. Proof of purchase must be
provided.
Any material or manufacturing defect within this timeframe will be rectified or repaired free of cost.
Any damage resulting from misuse, in particular non-observance of the instruction manual and
excessive wear and tear is excluded from warrantee. Any unauthorized modifications or opening of
the product will void the warranty.
8. Troubleshooting
Problem
Probable Cause
Remedy
Low flow rate
Outlet piping clogged or kinked
Clean / remove kink
Check valve contaminated
Clean
Head to large
Reduce head
Motor is idle or does not start
No voltage present
Check power supply
Plug not plugged in
Plug in plug
Pump blocked by mud or solids
Clean tank and pump body
Defective motor
Replacement by qualified personnel
Defective electronics
Replacement by qualified personnel
Motor running, pump does not
deliver
Outlet piping clogged or kinked
Clean / remove kink
Check valve contaminated
Clean
Pump does not operate
automatically
Float switch contaminated
Clean
Micro-switch defective
Replacement by qualified personnel
9. Decleration of conformity
This declaration is valid for the following product:
Device type:
Condensate-Pump Neotech 360
We hereby declare that the product is in conformity with the provisions of the
Machinery Directive
(73/23/EEC)
.
The following norms have been taken as a reference with respect to the electromagnetic
compatibility (89/336/CEE):
EN 50081 – 1 and EN 50081 – 2
This declaration is made by:
Neotech
Via N. Sauro 12
20043 Arcore (MI)
Thomas Spamer Technical manager