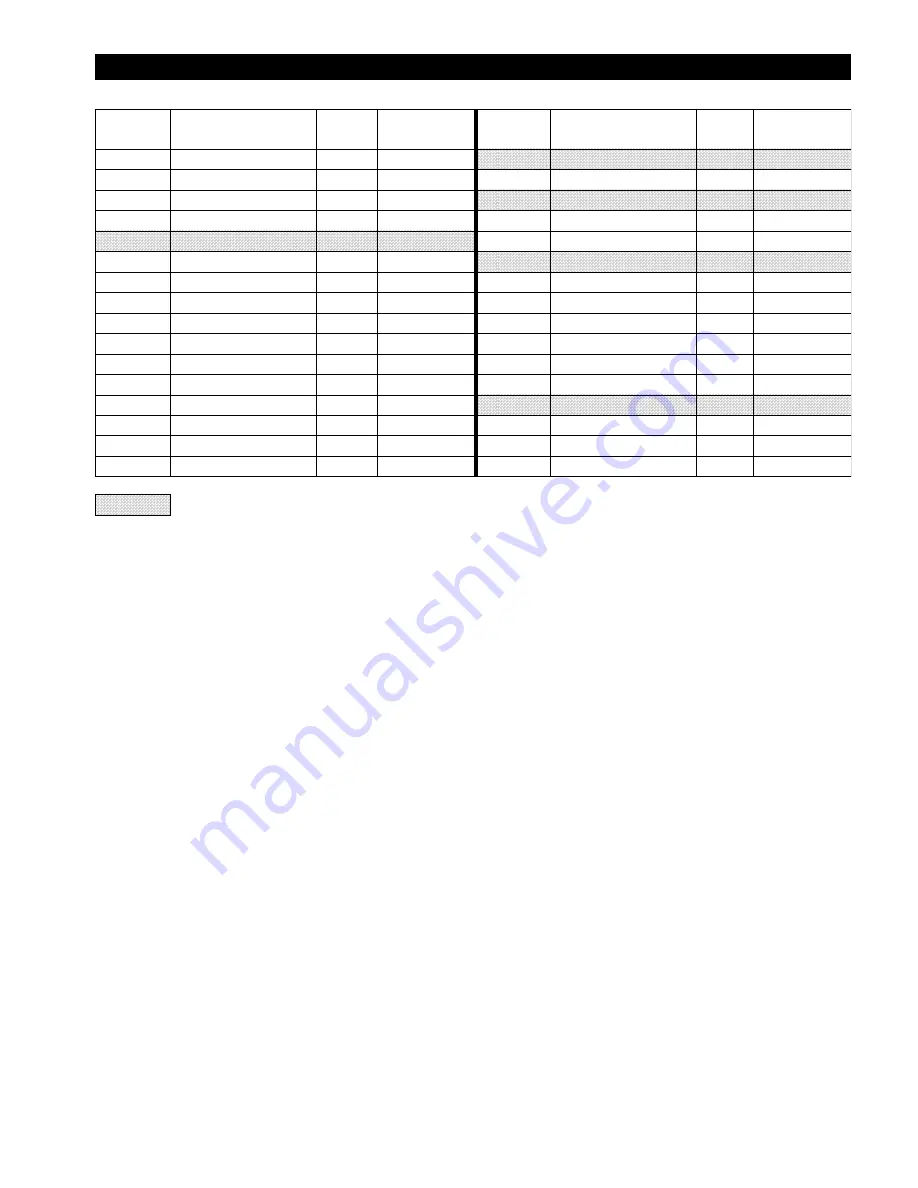
41
CONTROL VALVE ASSEMBLY PARTS LIST
ITEM
NO.
DESCRIPTION
OF PART
QTY
TOTAL
PART
NUMBER
ITEM
NO.
DESCRIPTION
OF PART
QTY
TOTAL
PART
NUMBER
260
Valve Assembly *
1
26126
•
315
Seal Ring
2
K5B-606
300
Handle
1
K5B-556P
316
Valve Body
1
26125
301
Roll Pin
1
K5B-1115
•
317
Gasket
1
K5B-275
302
Capscrew
4
71292064
318
Flange
1
KK5B-276SP
•
303
Spring
1
K5B-412
319
Fitting, Elbow Swivel
1
71328561
304
Lockwasher
4
51581
•
321
Gasket
1
K5B-547
305
Valve Body Retainer
1
K5B-1110AP
331
Capscrew
4
71325039
306
Spring Retaining Stud
1
K5B-553
523
Fitting, Elbow
1
71273676
307
Latch
1
K5B-869AP
524
Fitting, Nipple
1
71057483
308
Roll Pin
1
HLK-20
525
Muffler
1
52472
309
Pipe Plug
2
71263297
606
Manifold ***
1
26128
310
Fitting, Bushing
1
51814
607
Cover, Manifold ***
1
26130
311
Valve Housing **
1
26062
•
611
Gasket
1
26129
312
Roll Pin
1
71326102
612
Pipe Plug
2
54246
313
Grease Fitting
1
53095
613
Dowel Pin
1
71326508
314
Valve Bushing **
1
26040
614
Capscrew
4
71326441
•
Recommended spare.
*
Valve Assembly (260) includes items 300 through 309 and 311 through 318.
**
Valve Housing (311) and Valve Bushing (314) are a matched set. Replace both at the same time.
***
Manifold (606) and Cover (607) are bonded together and should not be separated.
Содержание force5 GULF MAN-RIDER FA2A-GMR
Страница 8: ...8 ...
Страница 34: ...34 WINCH ASSEMBLY PARTS DRAWING ...
Страница 36: ...36 MOTOR ASSEMBLY PARTS DRAWING ...
Страница 40: ...40 CONTROL VALVE ASSEMBLY PARTS DRAWING ...
Страница 42: ...42 REMOTE PENDANT AND CONTROL VALVE ASSEMBLY PARTS DRAWING ...