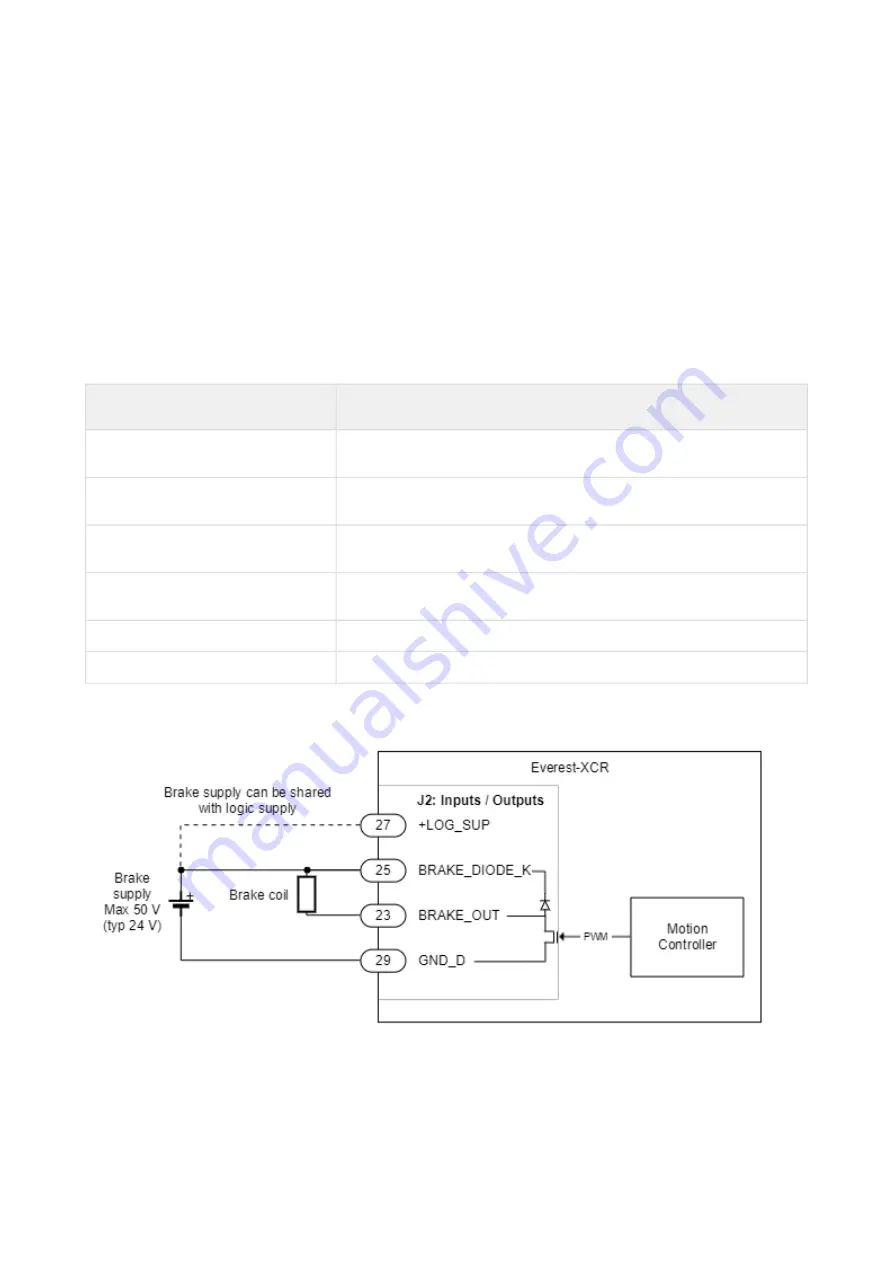
Everest XCR - Product manual |
Wiring and Connections
INGENIA | 2020-10-01 00:04:38
56
9.5. Brake and Motor Temperature
9.5.1. Motor electromagnetic / electromechanical brake
Electromechanical brakes are needed in critical applications where the disconnection of the motor or a lack of
electric braking could be dangerous or harmful (i.e. falling suspended loads). Everest XCR Servo Drive includes
a brake output on the I/O connector J2. The brake output is an N-Channel MOSFET that can be PWM modulated to
reduce effective brake voltage and thus power consumption when energized
.
Its operation is usually configured for normally locked electromechanical brakes; that is, brakes that by default
block the movement of the motor shaft when not powered. This kind of brakes increases the safety of the
application because, in a drive power failure, the switch would be opened therefore the brake activated. Main
ratings of the brake switch are detailed in the next table:
Specification
Value
Type of output
N-Channel MOSFET, open-drain with a recirculation diode
Maximum voltage
50 V (connector limited)
Maximum current
1A (full temperature range)
Delay after enabling the brake
0 ~ 10000 ms (
)
Delay before release brake
0 ~ 10000 ms (
)
Brake PWM frequency
4 kHz ~ 40 kHz
The next figure shows how the typical connection of the brake using a dedicated power supply.
The next figure shows the connection with a single power supply (< 50V systems). Note that it is possible to operate
a 24 V brake with a 48 V power supply by configuring the maximum PWM duty cycle of the brake to 50%. In this case,
configure it carefully before physically connecting the brake.
Содержание 2147502492
Страница 31: ...Everest XCR Product manual Connectors Guide INGENIA 2020 10 01 00 04 38 31 Image TE B 155 9001...
Страница 72: ...Everest XCR Product manual Wiring and Connections INGENIA 2020 10 01 00 04 38 72...
Страница 85: ...Everest XCR Product manual Installation INGENIA 2020 10 01 00 04 38 85...