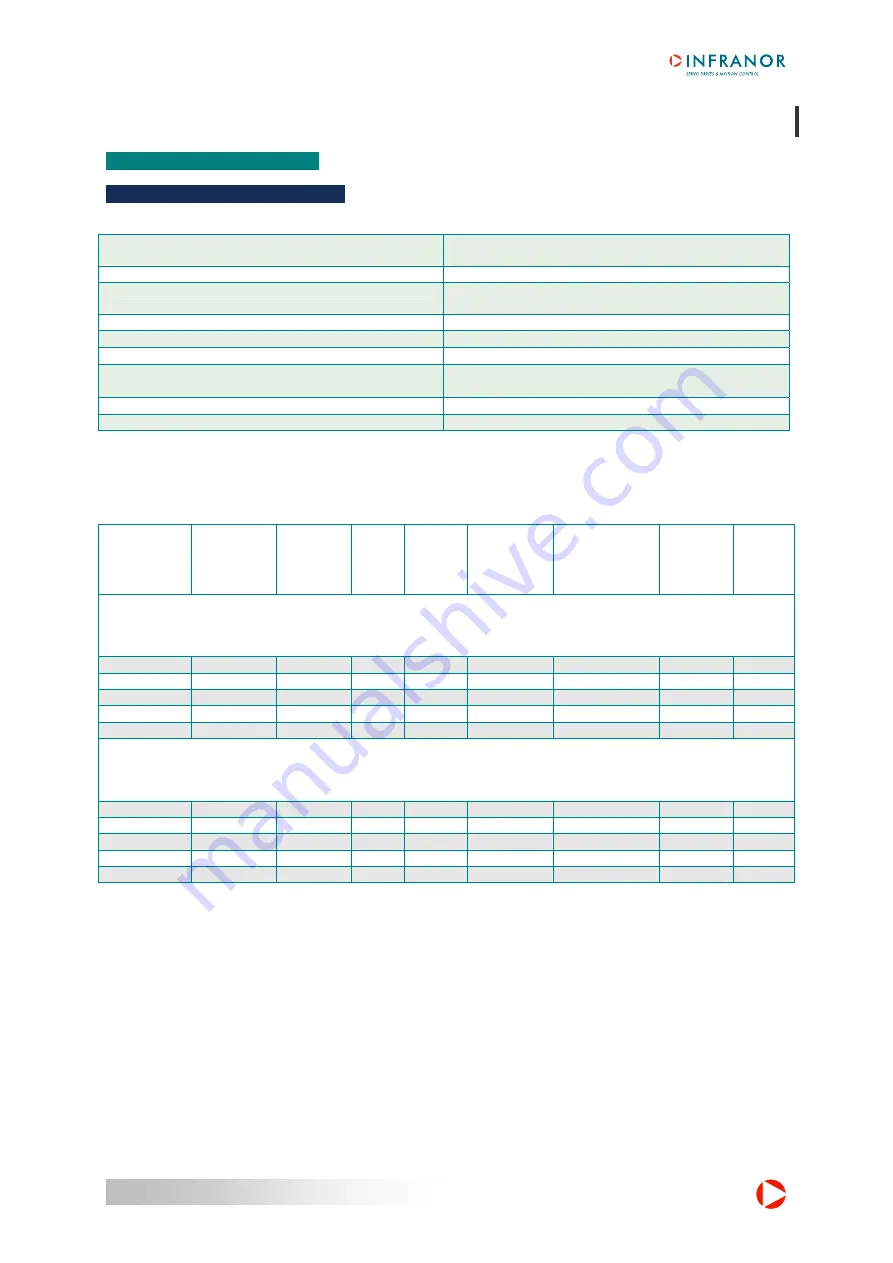
GD1 – Installation Guide
13
Part 1 –
Chapter 2 – Specifications
Chapter 2 – Specifications
2.1 – MAIN TECHNICAL DATA
2.1.1
–
GD1-230/I
SINGLE
-
AXIS DRIVE
Mains operated power supply voltage
230 V
AC
+10% / -15% single-phase
50-60 Hz
Isolated auxiliary logic supply
Input voltage: 24 V
DC
+/-15%
Input current: I
XN
= 320 mA without brake
Motor phase-phase output voltage
≥
200 Vrms
Integrated braking system
200
Ω
/ 65 W
or external resistor: min. 50
Ω
(dp 50/200)
Triggering threshold of the braking system
400 V +/-10 V
OUTPUT CURRENT RATINGS (at a maximum room temperature of 40° C)
Drive type
Max. output
current
(Arms) for
1 sec. +/-5%
(230 V
AC
)
Rated
output
current
(Arms)
(230 V
AC
)
Rated
power
(kW)
Power
losses
(W)
Rated input
current
(Arms)
(230 V
AC
60 Hz)
Max. protection
fuses for line
circuit A60Q
listed (Ferraz)
Short-
circuit
power of
the mains
UL
listed
Use with integrated single-phase 230 V
AC
power supply unit:
Drive type: GD1-230/cc-PS
GD1-230/05
5
2.5
1
2.5
2 A
5 kA
Yes
GD1-230/08
8
4
1.6
4
4 A
5 kA
Yes
GD1-230/11
11
5.5
2.2
5.5
6 A
5 kA
Yes
GD1-230/17
17
8.5
3.4
8.5
10 A
5 kA
Yes
GD1-230/30
30
10
4
10
15 A
5 kA
Yes
Use with external power supply unit GDPS supplied in 230 V
AC
three-phase
Drive type: GD1-230/cc-00-0
GD1-230/05
5
2.5
1
2.5
2 A
5 kA
Yes
GD1-230/08
8
4
1.6
4
4 A
5 kA
Yes
GD1-230/11
11
5.5
2.2
5.5
6 A
5 kA
Yes
GD1-230/17
17
8.5
3.4
8.5
10 A
5 kA
Yes
GD1-230/30
30
15
6
15
15 A
5 kA
Yes
Содержание GD1-400/05
Страница 1: ...GD1 INFRANOR Gem Drive Installation Guide gb Actuator ...
Страница 5: ...4 Part 1 GD1 amplifier GD1 Installation Guide PART 1 ________ GD1 AMPLIFIER ...
Страница 40: ...GD1 Installation Guide 39 Part 2 GDPS power supply PART 2 ________ GDPS POWER SUPPLY ...
Страница 49: ...48 Part 2 Chapter 4 Order code GD1 Installation Guide PART 3 ________ APPENDIX ...