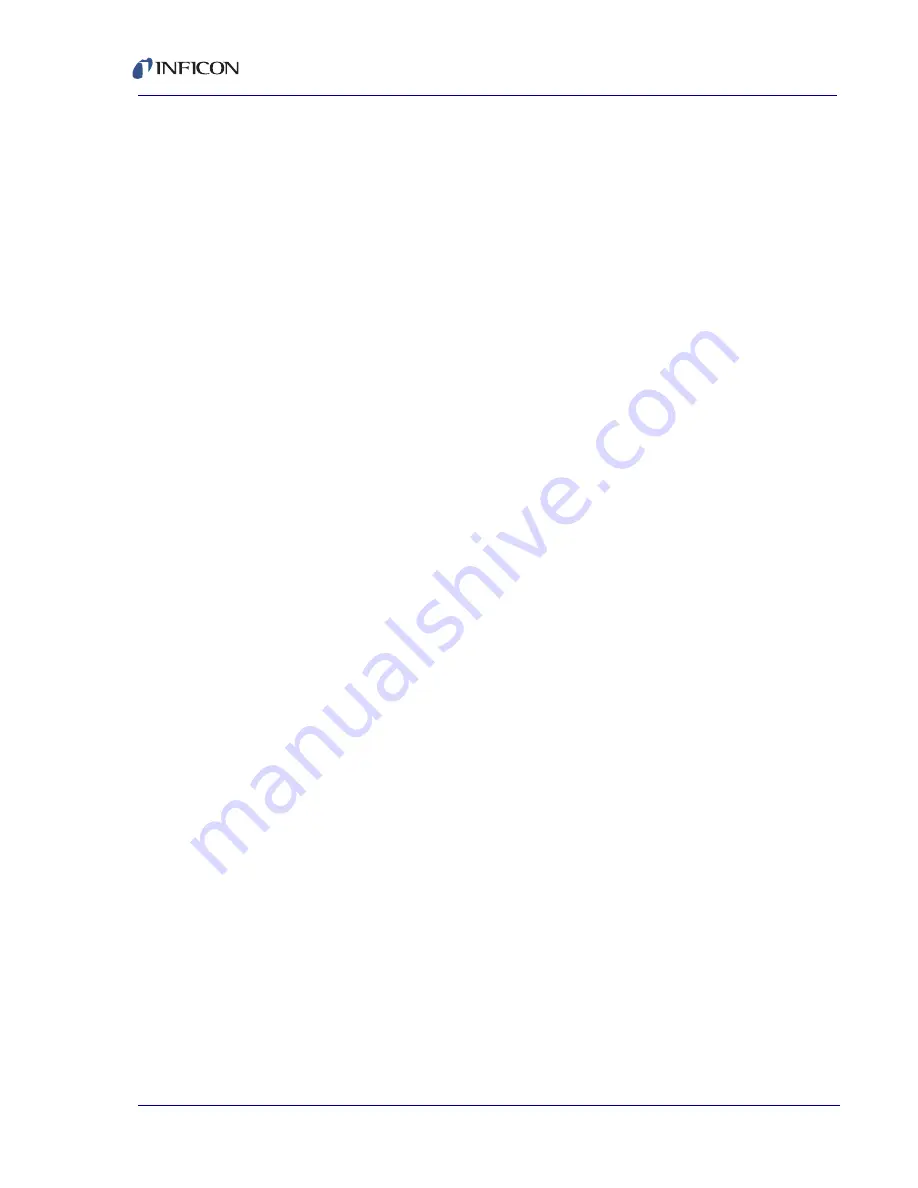
8 - 9
XTC/3 Operating Manual
8.1.6 Control Loop Theory
The instrumental advances in measurement speed, precision and reliability would
not be complete without a means of translating this improved information into
improved process control. For a deposition process, this means keeping the
deposition rate as close as possible to the desired rate. The purpose of a control
loop is to take the information flow from the measurement system and to make
power corrections that are appropriate to the characteristics of the particular
evaporation source. When properly operating, the control system translates small
errors in the controlled parameter, or rate, into the appropriate corrections in the
manipulated parameter, power. The controller’s ability to quickly and accurately
measure and then react appropriately to the small changes keeps the process from
deviating very far from the set point.
The controller model most commonly chosen, for converting error into action is
called PID. In the PID, P stands for proportional, I stands for integral and D stands
for derivative action. Certain aspects of this model will be examined in detail a little
further on. The responsiveness of an evaporation source can be found by
repetitively observing the system response to a disturbance under a particular set
of controller settings. After observing the response, improved controller parameters
are estimated and then tried again until satisfactory control is obtained. Control,
when it is finally optimized, essentially matches the parameters of the controller
model to the characteristics of the evaporation source.
Techniques for calculating optimum source control parameters can be classified by
the type of data used for tuning. They fall into basically three categories:
Closed Loop Methods
Open Loop Methods
Frequency Response Methods
Of these categories, the open loop methods are considered superior. They are
considered superior because of the ease with which the necessary experimental
data can be obtained and because of the elimination (to a large extent) of trial and
error when the technique is applied. The important response characteristics are
determined as shown in
In general, it is not possible to characterize all processes exactly; some
approximation must be applied. The most common is to assume that the dynamic
characteristics of the process can be represented by a first-order lag plus a dead
time. The Laplace transform for this model (conversion to the s domain) is
approximated as:
[5]
Output
Input
------------------
K
p
L
– s
exp
T
1
s 1
+
-------------------------------
=