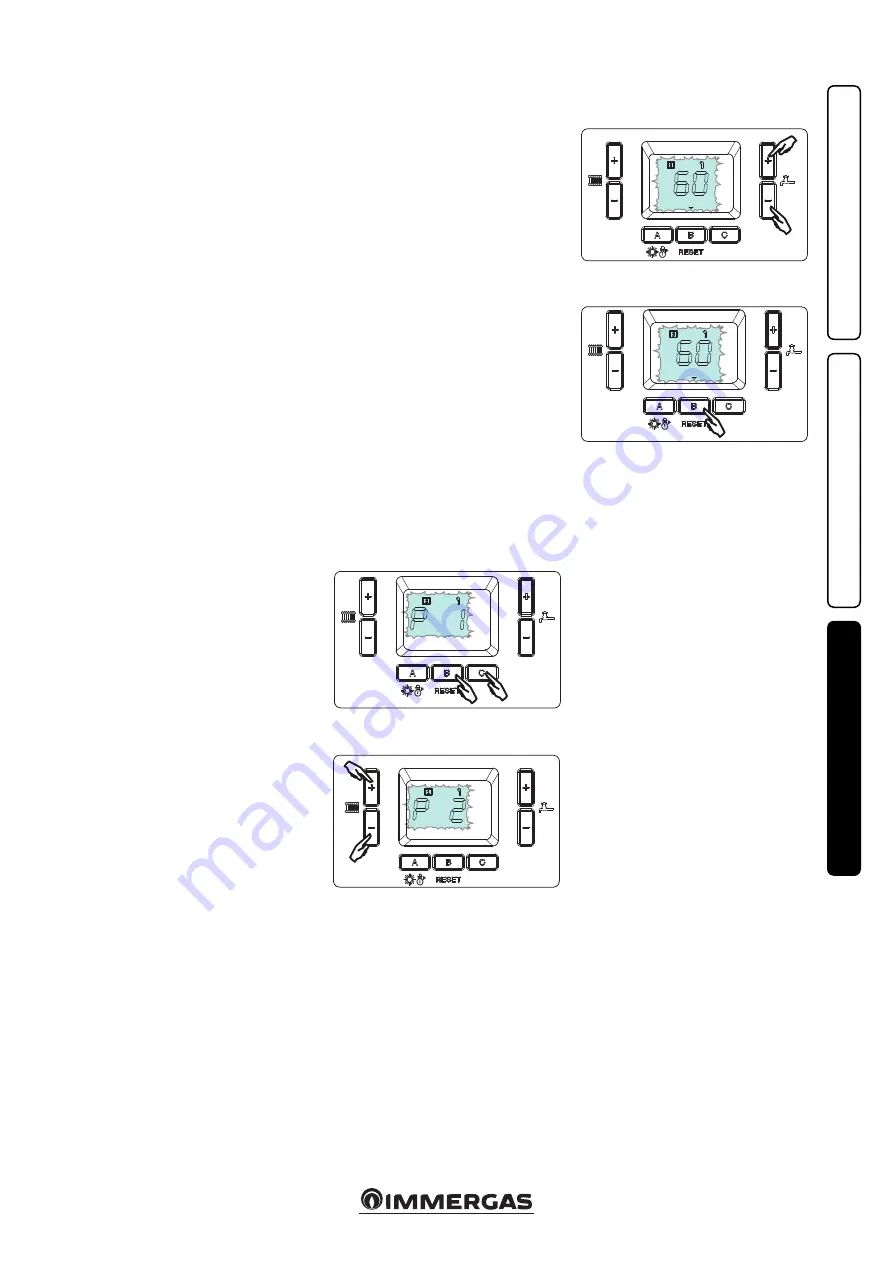
31
INS
TALLER
US
ER
MAINTEN
AN
CE TECHNI
CI
AN
- Noise due to air in the system. Check opening
of the special air vent valve cap (Fig. 1-25 Ref.
19). Check that system filling and air bleeding
has been performed according to the require-
ments.
- Noise due to air inside the condensation
module. Use the manual air vent valve (Fig.
1-25 Ref. 15) to eliminate any air present in the
condensation module. When the operation has
been performed, close the manual vent valve.
- No DHW is produced. The boiler is equipped
with a function that automatically recognises
when there is an optional DHW probe, and an
anomaly is reported if there is a failure affecting
the DHW NTC probe. If there is a power out-
age, or if the boiler is switched off and back on
again during the failure, it will not be possible
to detect said failure, but it will, however, be
recorded in the errors anomaly records.
- In case of ΔT > 35 °C, the boiler lowers the
power to avoid surpassing that value. When
this status is on, the flow temperature symbol
flashes.
3.8 PROGRAMMING THE BOILER P.C.B.
The boiler is prepared for possible programming
of several operation parameters. By modifying
these parameters as described below, the boiler
can be adapted according to specific needs.
- Access programming by pressing and holding
down buttons “B” and “C”.
- Scroll through the parameters by pressing the
+ and - heating adjustment buttons,
3-7
3-8
3.7 TROUBLESHOOTING.
N.B.:
maintenance interventions must be carried
out by a qualified licensed operative.
- Smell of gas. Caused by leakage from gas circuit
pipelines. Check sealing efficiency of gas intake
circuit.
- Repeated ignition blocks. No gas, check the
presence of pressure in the network and that
the gas adduction valve is open. Incorrect
adjustment of the gas valve, check the correct
calibration of the gas valve.
- Irregular combustion or noisiness. It may be
caused by: a dirty burner, incorrect combustion
parameters, intake-exhaust terminal not cor-
rectly installed. Clean the above components
and ensure correct installation of the terminal,
check correct setting of the gas valve (Off-Set
setting) and correct percentage of CO
2
in flue
gases.
- The over temperature safety thermostat, the
flow probe or the return probe are triggered
frequently. It can depend on the lack of water in
the boiler, little water circulation in the system
or blocked pump. Check on the manometer
that the system pressure is within established
limits. Check that the radiator valves are not
closed and also the functionality of the pump.
In addition:
- Also check the integrity of the thermofuse, and
if it has been triggered it will be necessary to
check the integrity of the module and the flue
circuit.
- Check that the exchanger safety thermostat has
not intervened. If it has, check the integrity of
the module and ceramic fibre panel, replace
the cover gasket of the manifold and reset the
thermostat by pressing the specific button.
- Heat exchanger clogged. This may be caused by
the trap being blocked. Check, by means of the
condensate drain cap, that there are no residues
of material blocking the flow of condensate.
- Change the parameter by pressing the + and -
DHW adjustment buttons.
Save the parameters by switching from one
parameter to the next or by pressing “B”.
- Exit the programming mode by pressing and
Exit the programming mode by pressing and
holding down buttons “B” and “C” or wait
approximately 2 minutes without touching the
buttons.., the boiler will then run a self-diag-
nosis of the parameters by displaying “PARA”
followed by “Auto”.
- While the value of a parameter is being dis-
played, press “B” quickly to see the code again.
3-9
3-10