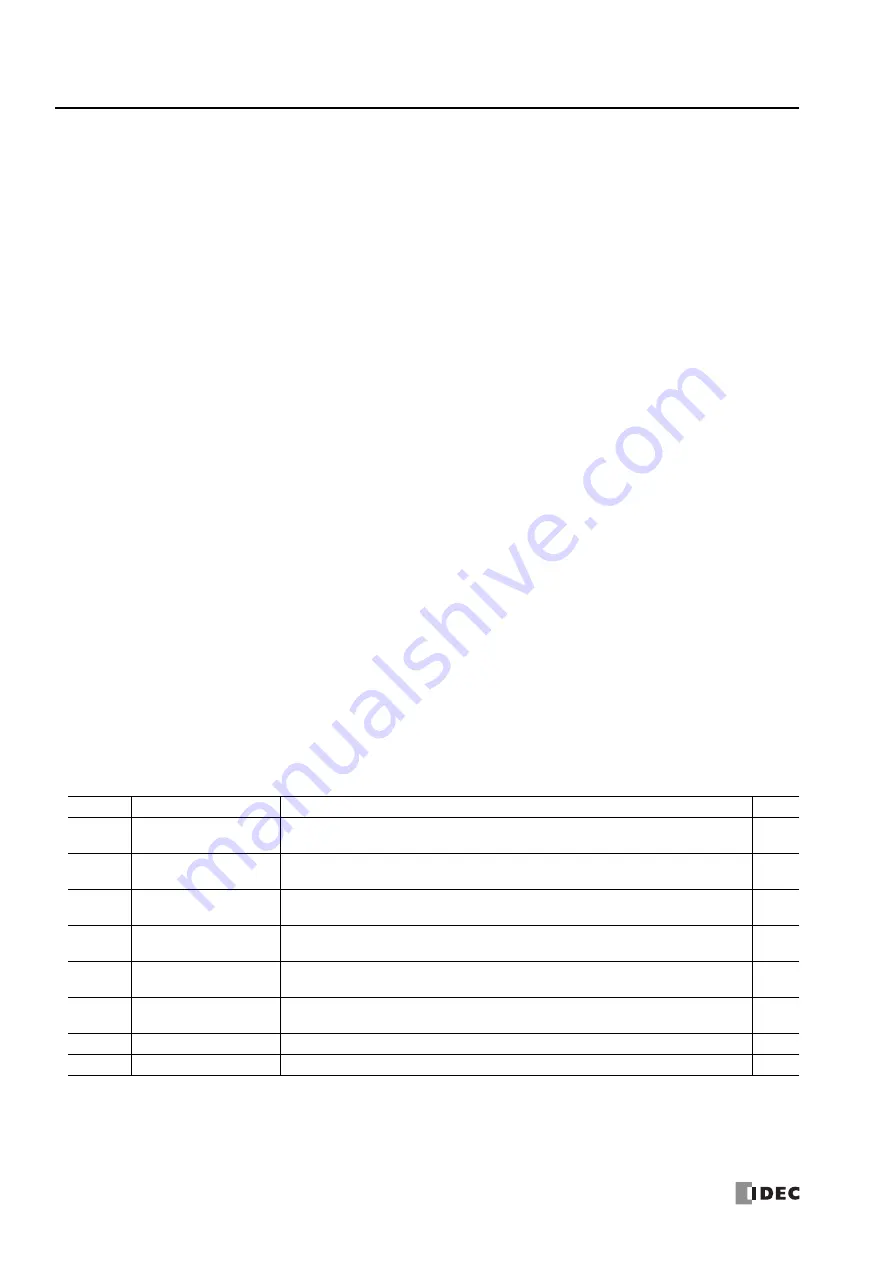
14:
PID
I
NSTRUCTION
14
‐
14
FC5A
M
ICRO
S
MART
U
SER
’
S
M
ANUAL
FC9Y
‐
B1273
S1+23 Output
Manipulated
Variable %
While
the
PID
action
is
in
progress,
the
data
register
designated
by
S1+23
holds
the
manipulated
variable,
–32768
through
32767
(–327.68%
through
327.67%),
indicating
the
value
to
the
second
decimal
place.
While
manual
mode
is
enabled
with
the
auto/manual
mode
control
relay
(S2+1)
set
to
on,
S1+23
holds
an
indefinite
value.
While
auto
tuning
or
advanced
auto
tuning
is
in
progress,
S1+23
holds
an
indefinite
value.
S1+24 Output
Manipulated
Variable
for
Analog
Output
Module
While
the
PID
action
is
in
progress,
the
data
register
designated
by
S1+24
holds
a
value
of
0
through
4095
or
50000,
depending
on
the
analog
I/O
module
type.
The
value
is
converted
from
the
value
of
0
through
100
stored
in
S1+1
to
rep
‐
resent
the
output
manipulated
variable
of
0%
through
100%.
While
manual
mode
is
enabled
with
the
auto/manual
mode
control
relay
(S2+1)
set
to
on,
S1+24
holds
a
value
of
0
through
4095
or
50000
converted
from
the
manual
mode
output
manipulated
variable
(S1+18).
While
auto
tuning
or
advanced
auto
tuning
is
in
progress,
S1+24
holds
a
value
of
0
through
4095
or
50000
read
from
the
AT
output
manipulated
variable
(S1+22).
S1+25 Proportional
Band
Offset
Value
When
the
proportional
band
is
selected
(S1+4
set
to
2
or
3),
the
output
manipulated
variable
(S1+1)
of
0%
through
100%
can
be
shifted
by
an
offset
of
–100%
through
100%.
Set
a
required
offset
value
of
–100
through
100
to
the
data
register
designated
by
S1+25
before
executing
auto
tuning.
When
the
proportional
gain
is
selected
(S1+4
set
to
0
or
1),
the
proportional
band
offset
value
(S1+25)
has
no
effect.
S1+26 Derivative
Gain
The
derivative
gain
can
be
selected
from
0%
through
100%.
When
the
derivative
gain
is
set
to
a
small
value,
the
output
manipulated
variable
(S1+1)
is
susceptible
to
an
external
noise
or
a
change
in
the
set
point.
When
the
derivative
gain
is
set
to
a
large
value,
the
output
manipulated
variable
(S1+1)
becomes
less
susceptible
to
an
external
noise
or
a
change
in
the
set
point,
but
stability
is
adversely
affected
during
normal
operation.
Set
a
required
derivative
gain
of
0
through
100
to
the
data
register
designated
by
S1+26
before
executing
auto
tuning.
Recommended
values
are
20%
through
30%
when
the
process
variable
fluctuates
or
is
subject
to
noise.
Source
Device
S2
(Control
Relay)
Turn
on
or
off
appropriate
outputs
or
internal
relays
starting
with
the
device
designated
by
S2
before
executing
the
PID
instruction
as
required.
Devices
S2+4
through
S2+7
are
for
read
only
to
reflect
the
PID
and
auto
tuning
statuses.
Device
Function
Description
R/W
S2+0
Control
action
ON: Direct
control
action
OFF: Reverse
control
action
R/W
S2+1
Auto/manual
mode
ON: Manual
mode
OFF: Auto
mode
R/W
S2+2
Output
manipulated
variable
limit
enable
ON: Enable
output
manipulated
variable
upper
and
lower
limits
(S1+16
and
S1+17)
OFF: Disable
output
manipulated
variable
upper
and
lower
limits
(S1+16
and
S1+17)
R/W
S2+3
Integral
start
coefficient
disable
ON: Disable
integral
start
coefficient
(S1+10)
OFF: Enable
integral
start
coefficient
(S1+10)
R/W
S2+4
High
alarm
output
ON: When
process
variable
(S1+0)
high
alarm
value
(S1+14)
OFF: When
process
variable
(S1+0)
<
high
alarm
value
(S1+14)
R
S2+5
Low
alarm
output
ON: When
process
variable
(S1+0)
low
alarm
value
(S1+15)
OFF: When
process
variable
(S1+0)
>
low
alarm
value
(S1+15)
R
S2+6
Control
output
Goes
on
and
off
according
to
the
AT
parameters
or
PID
calculation
results
R
S2+7
AT
complete
output
Goes
on
when
AT
is
complete
or
failed,
and
remains
on
until
reset
R
Содержание MICROSmart FC5A Series
Страница 1: ...FC5A SERIES FC9Y B1273 1 User s Manual Advanced Volume ...
Страница 2: ......
Страница 8: ...Preface 6 FC5A MicroSmart User s Manual FC9Y B1273 ...
Страница 14: ...TABLE OF CONTENTS vi FC5A MICROSMART USER S MANUAL FC9Y B1273 ...
Страница 52: ...4 DATA COMPARISON INSTRUCTIONS 4 10 FC5A MICROSMART USER S MANUAL FC9Y B1273 ...
Страница 72: ...5 Binary Arithmetic Instructions 5 20 FC5A MicroSmart User s Manual FC9Y B1273 ...
Страница 88: ...7 SHIFT ROTATE INSTRUCTIONS 7 12 FC5A MicroSmart User s Manual FC9Y B1273 ...
Страница 112: ...8 DATA CONVERSION INSTRUCTIONS 8 24 FC5A MicroSmart User s Manual FC9Y B1273 ...
Страница 138: ...11 PROGRAM BRANCHING INSTRUCTIONS 11 14 FC5A MICROSMART USER S MANUAL FC9Y B1273 ...
Страница 178: ...13 PULSE INSTRUCTIONS 13 32 FC5A MICROSMART USER S MANUAL FC9Y B1273 ...
Страница 202: ...14 PID INSTRUCTION 14 24 FC5A MICROSMART USER S MANUAL FC9Y B1273 ...
Страница 206: ...15 DUAL TEACHING TIMER INSTRUCTIONS 15 4 FC5A MICROSMART USER S MANUAL FC9Y B1273 ...
Страница 214: ...16 INTELLIGENT MODULE ACCESS INSTRUCTIONS 16 8 FC5A MICROSMART USER S MANUAL FC9Y B1273 ...
Страница 248: ...21 COMPUTER LINK COMMUNICATION 21 4 FC5A MICROSMART USER S MANUAL FC9Y B1273 ...
Страница 272: ...23 MODBUS TCP COMMUNICATION 23 10 FC5A MICROSMART USER S MANUAL FC9Y B1273 ...
Страница 332: ...25 EXPANSION RS232C RS485 COMMUNICATION 25 16 FC5A MICROSMART USER S MANUAL FC9Y B1273 ...
Страница 341: ...NOTE FC5A MICROSMART USER S MANUAL FC9Y B1273 1 ...
Страница 342: ...NOTE 2 FC5A MICROSMART USER S MANUAL FC9Y B1273 ...