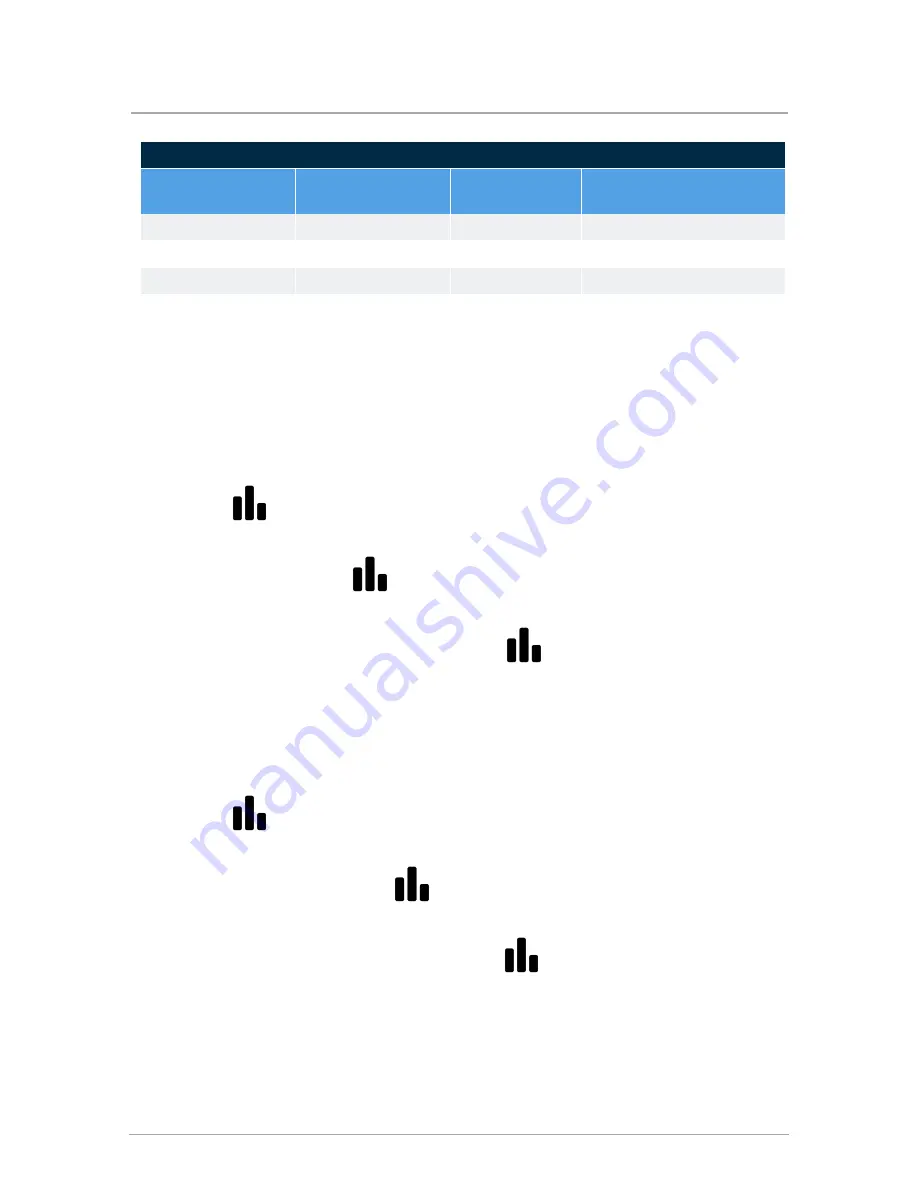
SIM Status Indicators
LED 1
LED 2
State
Description, LED status
indication
On
On
Heating
Rapid flash
On
Igniting
Off
Flashing
Lockout
Flash alternately with
LED 2
Flash alternately with
LED 1
Fail-safe
Boiler requires a power cycle
Table 13
SIM+ LED status Indicators
8.1.4.2 Resetting a boiler after a LWCO lockout
A boiler in a lockout condition due to a LWCO error will need to be reset.
1. Go to
>
Clear Errors
>
Yes
.
2. Check that there is enough water in the system and that the boiler is pressurized.
3. To reset the boiler, go to
>
SIM Menu
>
LWCO Test
>
Reset
>
Yes
.
4. Run the boiler to ensure that the error has been cleared.
5. If the error persists, perform a LWCO test. Go to
>
SIM Menu
>
Hi-Limit Test
>
Run the test to check if the low water cutoff sensor is opening.
8.1.4.3 Resetting a boiler after a hi-limit temperature lockout
A boiler in a lockout condition due to a hi-limit temperature error will need to be reset.
1. Go to
>
Clear Errors
>
Yes
.
2. Check that there is no air trapped in the system and that the boiler is pressurized.
3. To reset the SIM Module, go to
>
SIM Menu
>
Hi-Limit Test
>
Reset
>
Yes
.
4. Run the boiler to ensure that the error has been cleared.
5. If the error persists, perform a hi-limit test. Go to
>
SIM Menu
>
Hi-Limit Test
>
Run the test to see if the hi-limit switch is operational. You can also perform this test for
gasket blowouts.
88
Section: Troubleshooting
Содержание IBGFSW1-0110
Страница 8: ...Intentionally left empty ...
Страница 14: ...Intentionally left empty ...
Страница 52: ...Figure 36 Two pump two load parallel piping concept 48 Section Installation ...
Страница 74: ...Intentionally left empty ...
Страница 100: ...Intentionally left empty ...
Страница 101: ...97 Appendices Wiring diagrams Figure 48 Controller electrical diagram ...
Страница 102: ...Figure 49 Internal wiring diagram 98 Section Appendices ...
Страница 103: ...Figure 50 Sequence of Operation 99 Appendices ...
Страница 106: ...102 Section Appendices ...