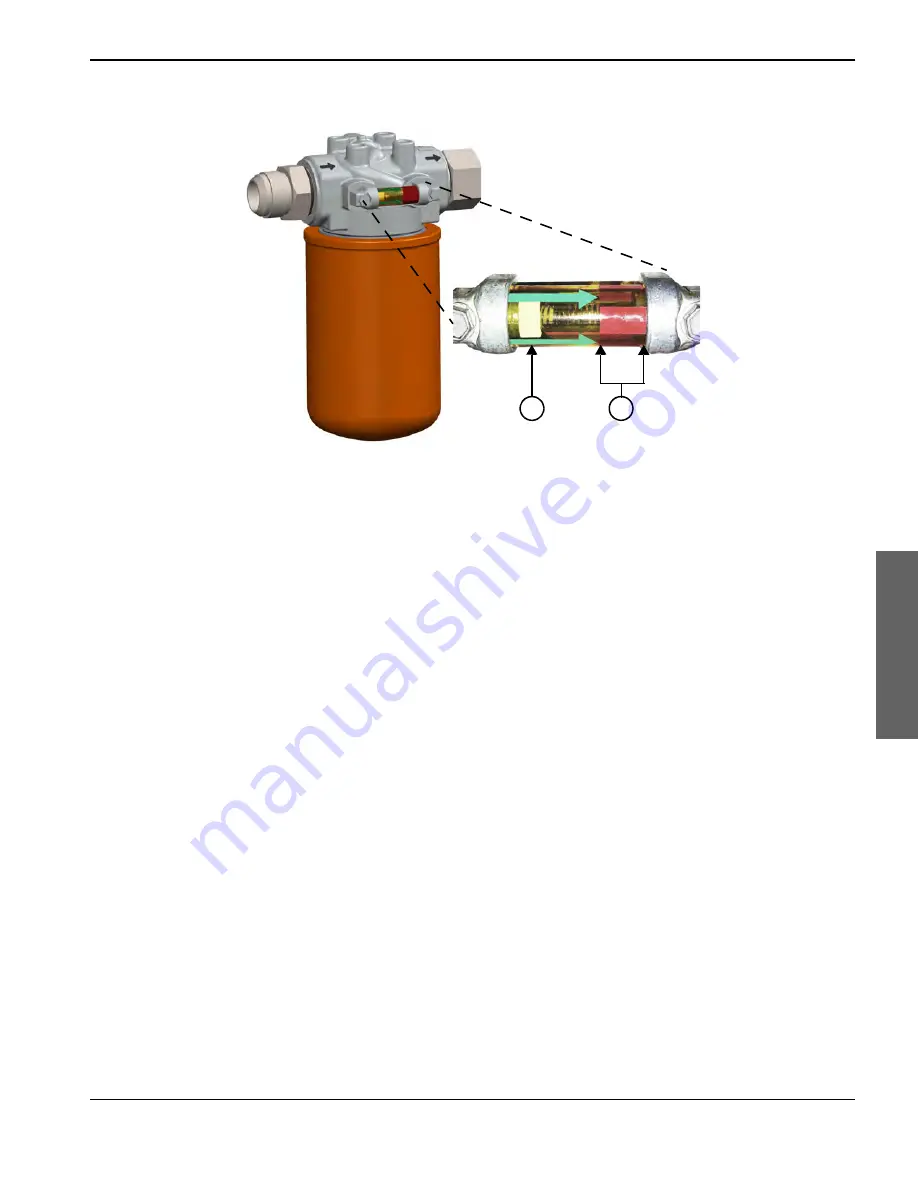
HyPrecision15/30/50
Operator
Manual 808240
71
5 – Preventive maintenance
Preventive maintenance
Check the hydraulic fluid indicator
Replace the filter after every 1,500 hours of operation.
Replace the filter when the white indicator stays in the red zone while the pump is running at operating temperature.
Refer to page 92 for instructions.
1
2
1
White indicator
2
Red zone
Содержание HyPrecision 15
Страница 1: ...HyPrecision15 30 50 Waterjet Pump Operator Manual 808240 Revision 1 English ...
Страница 10: ...10 HyPrecision15 30 50 Operator Manual 808240 Pump information Pump information ...
Страница 12: ...SC 12 Safety and compliance Warranty Warranty ...
Страница 16: ...SC 16 Safety and compliance Product stewardship Product stewardship ...
Страница 18: ...SC 18 Safety and compliance Environmental stewardship Environmental stewardship ...
Страница 24: ...SC 24 Safety and compliance Symbols and marks Symbols and marks ...
Страница 28: ...28 HyPrecision15 30 50 Operator Manual 808240 Terminology Terminology ...
Страница 44: ...44 HyPrecision15 30 50 Operator Manual 808240 3 Options Options ...
Страница 60: ...60 HyPrecision15 30 50 Operator Manual 808240 4 Operation Operation ...
Страница 146: ...146 HyPrecision15 30 50 Operator Manual 808240 5 Preventive maintenance Preventive maintenance ...
Страница 152: ...152 HyPrecision15 30 50 Operator Manual 808240 6 Parts lists Parts lists ...
Страница 176: ...176 HyPrecision15 30 50 Operator Manual 808240 8 Pump specifications Pump specifications ...
Страница 194: ...194 HyPrecision15 30 50 Operator Manual 808240 9 Installation Installation ...