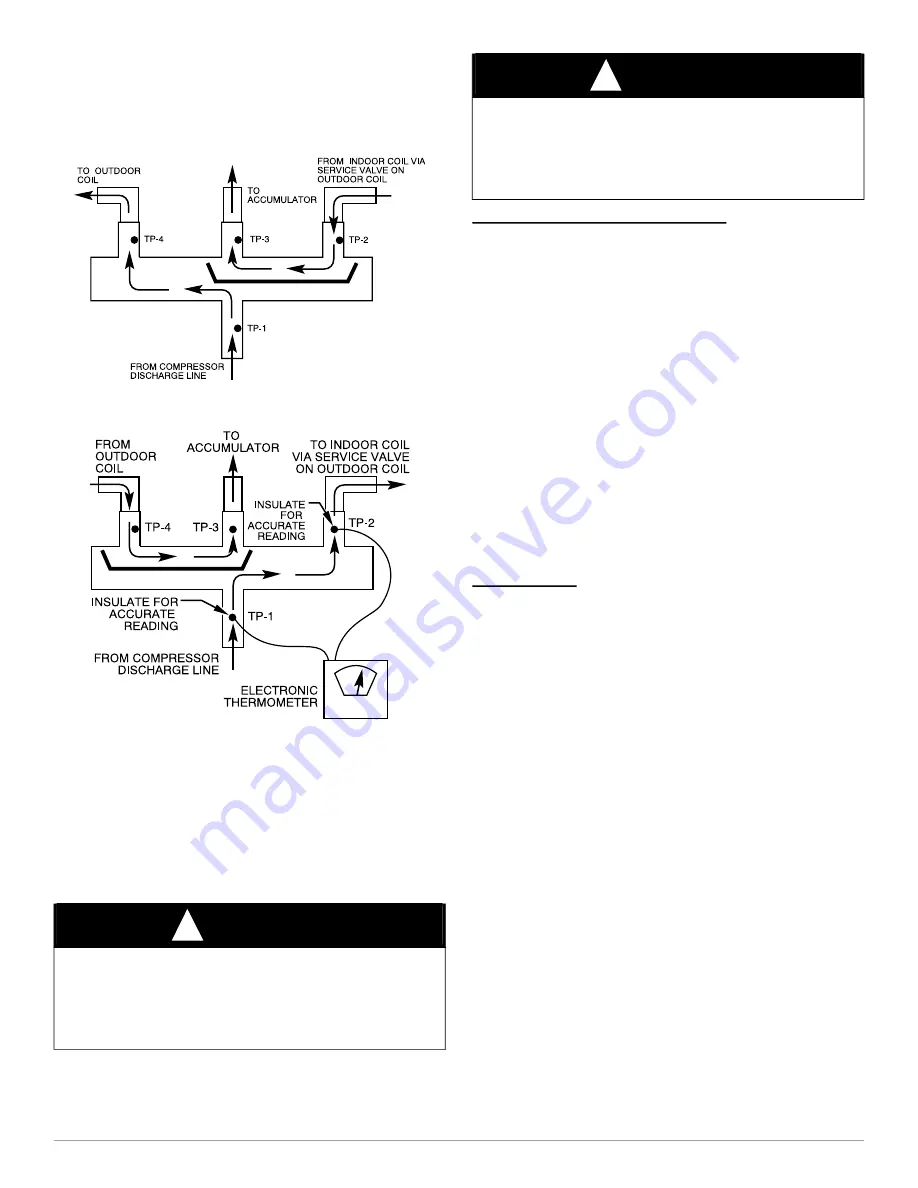
CVH8, HVH8, TVH8, VA9, HVA9, TVA9: APPLICATION GUIDELINE & SERVICE MANUAL
Manufacturer reserves the right to change, at any time, specifications and designs without notice and without obligations.
38
4. Use slip couplings to install new valve with stubs back into system.
Even if stubs are long, wrap valve with a wet rag to prevent
overheating.
5. After valve is brazed in, check for leaks. Evacuate and charge
system. Operate system in both modes several times to be sure
valve functions properly.
A88342
Fig. 40 – eversing Valve
(Cooling Mode or Defrost Mode, Solenoid Energized)
A88341
Fig. 41 – Reversing Valve
(Heating Mode, Solenoid De-Energized)
Liquid Line Filter Drier
Filter driers are specifically designed for R-22 or R-410A refrigerant.
Only operate with the appropriate drier using factory authorized
components.
It is recommended that the liquid line drier be installed at the indoor unit.
Placing the drier near the TXV allows additional protection to the TXV
as the liquid line drier also acts as a strainer.
Install Liquid-line Filter Drier Indoor
Install filter drier as follows:
1. Braze 5 in. liquid tube to the indoor coil.
2. Wrap filter drier with damp cloth.
3. Braze filter drier to 5 in. long liquid tube from step 1.
4. Connect and braze liquid refrigerant tube to the filter drier.
Suction Line Filter Drier
The suction line drier is specifically designed to operate with R-410A,
use only factory authorized components. Suction line filter drier is used
in cases where acid might occur, such as burnout. Heat pump units must
have the drier installed between the compressor and accumulator only.
Remove after 10 hours of operation. Never leave suction line filter drier
in a system longer than 72 hours (actual time).
Thermostatic Expansion Valve (TXV)
All fan coils and furnace coils will have a factory installed thermostatic
expansion valve (TXV). The TXV will be a bi-flow, hard-shutoff with
an external equalizer and a balance port pin. A hard shut-off TXV does
not have a bleed port. Therefore, minimal equalization takes place after
shutdown. TXVs are specifically designed to operate with R-410A or
R-22 refrigerant, use only factory authorized TXV’s.
Do not
interchange R-410A and R-22 TXVs.
TXV Operation
The TXV is a metering device that is used in air conditioning and heat
pump systems to adjust to changing load conditions by maintaining a
preset superheat temperature at the outlet of the evaporator coil. The
volume of refrigerant metered through the valve seat is dependent upon
the following:
1. Superheat temperature is sensed by cap tube sensing bulb on
suction tube at outlet of evaporator coil. This temperature is
converted into pressure by refrigerant in the bulb pushing
downward on the diaphragm which opens the valve via the push
rods.
2. The suction pressure at the outlet of the evaporator coil is
transferred via the external equalizer tube to the underside of the
diaphragm. This is needed to account for the indoor coil pressure
drop. Residential coils typically have a high pressure drop, which
requires this valve feature.
3. The pin is spring loaded, which exerts pressure on the underside of
the diaphragm. Therefore, the bulb pressure works against the
spring pressure and evaporator suction pressure to open the valve.
If the load increases, the temperature increases at the bulb, which
increases the pressure on the top side of the diaphragm. This opens
the valve and increases the flow of refrigerant. The increased
refrigerant flow causes the leaving evaporator temperature to
decrease. This lowers the pressure on the diaphragm and closes the
pin. The refrigerant flow is effectively stabilized to the load demand
with negligible change in superheat.
CAUTION
!
UNIT DAMAGE HAZARD
Failure to follow this caution may result in equipment damage or
improper operation.
To avoid performance loss and compressor failure, installation of filter
drier in liquid line is required.
CAUTION
!
UNIT DAMAGE HAZARD
Failure to follow this caution may result in equipment damage or
improper operation.
To avoid filter drier damage while brazing, filter drier must be wrapped
in a heat-sinking material such as a wet cloth.