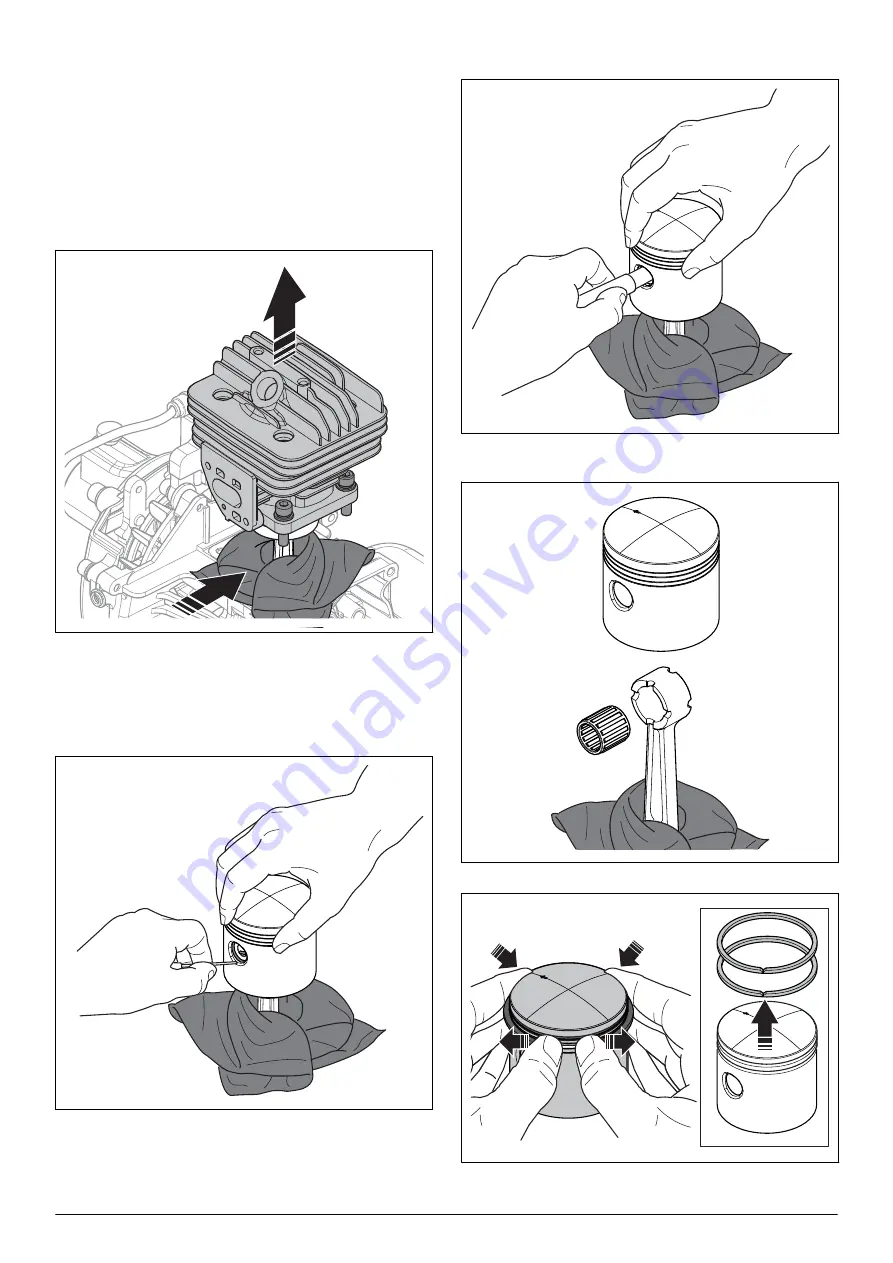
6. Remove the air filter cover, the air filter and the air
filter holder.
7. Remove the carburetor, the distance piece and the
heat shield.
7.9.2 To disassemble the cylinder and piston
cylinder and piston on page 29 to get access to the
cylinder and piston.
2. Loosen the 4 bolts and pull the cylinder up.
3. Remove the cylinder base gasket.
4. Put a cloth on top of the crankcase opening to make
sure that no dirt goes into the crankcase.
5. Use a pointed tool to remove the G snap rings for
the wrist pin.
6. Push the wrist pin from the piston with a punch of
the correct dimension.
7. Remove the piston and the needle bearing from the
rod.
8. Remove the piston rings.
30 - Repair instructions
1281 - 001 -
Содержание 331RB
Страница 1: ...Workshop manual 331RB English 1281 001 ...
Страница 47: ...1281 001 Technical data 47 ...
Страница 48: ...1141483 26 2019 09 27 ...