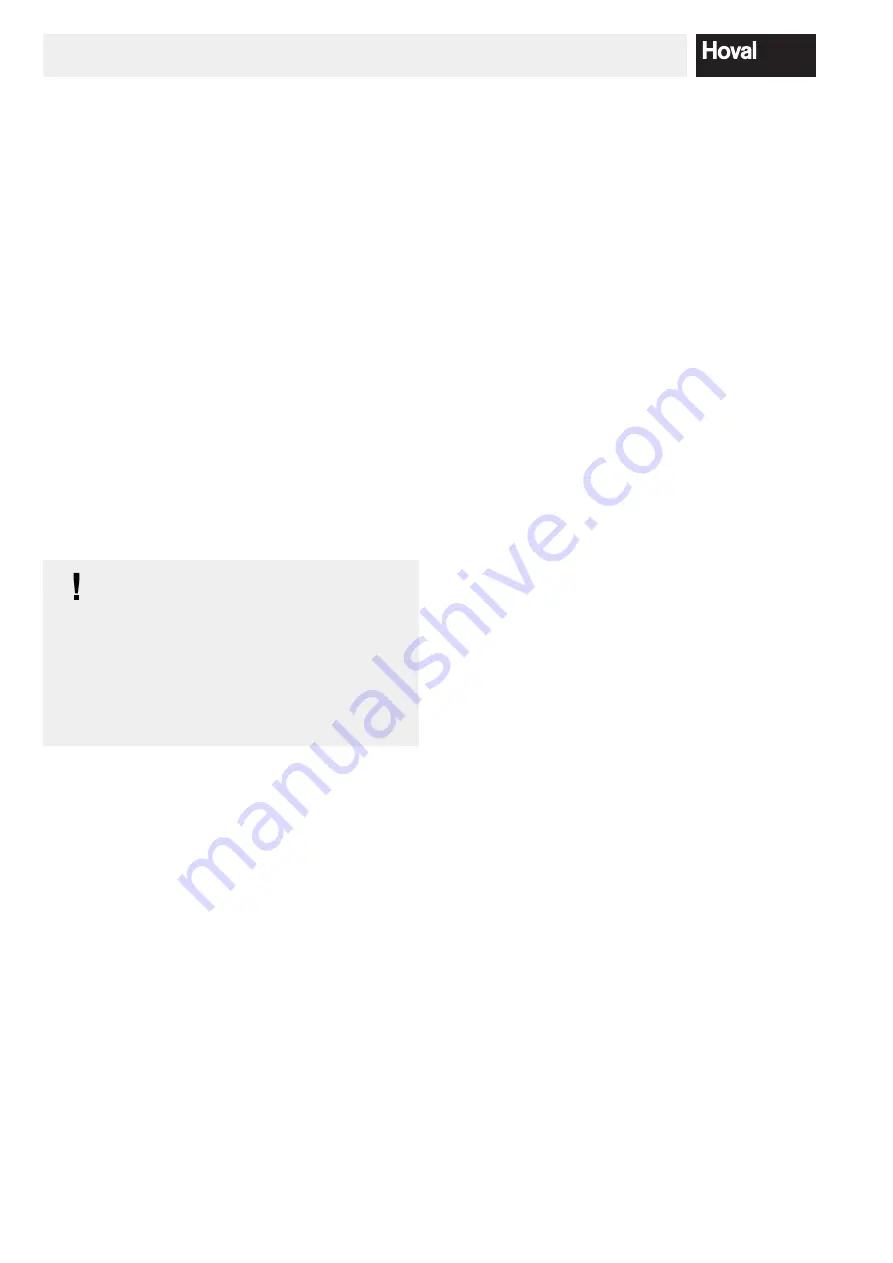
4 215 983 / 01
18
InSTaLLaTIOn
4.5
Minimum value limiting of boiler
return temperature
Hydraulic and control measures must be provided to en
sure that the temperatures do not fall below the per mis
si ble minimum boiler flow and return temperature under
any operating conditions.
4.6
Discharge of start-up condensate
from the boiler
• When commissioning a cold boiler, condensate always
oc curs within the boiler. This collects in the lower area
of the boiler (flue gas collector) and is then evaporated
through the boiler's continued heating up.
• The boiler should therefore – also for this reason – only
be started up without “network acceptance”, so that the
con den sation temperature threshold (approx. 55 °C) is
ex cee ded as quickly as possible
• If necessary, the condensate which occurs can be
drained via the flue gas collector's cleaning fitting (re-
move cap on the drain connection before starting the
burner, connect ball valve and temperatureresistant
drain hose).
NOTICE
• When draining the condensate, it must be
en sured that no uncontrolled escape of flue
gas occurs in the installation room (do not
keep the ball valve open “constantly”, but
only drain off the condensate “inter mit tently”).
• The locally valid waste water regulations
must be observed when disposing of the
con den sate!
As soon as the boiler has reached its minimum tem per
a ture and this can be kept stable via the return boost,
the burner should be shut off briefly and the closure cap
mounted on the cleaning drain connection again.
•
The drain connection on the boiler's flue gas collector is
not intended for the permanent connection of a drainage
line – frequent condensation in the area of the boiler is
impermissible!
4.7
Setting the temperature controllers
Basic setting of the controller is carried out by the heating
contractor.
4.8
Safety valves
The heating system and hot water supply must each be
pro tected with one safety valve against impermissible
over pressure. The discharge capacity of the heating sys
tem safety valve must correspond to the boiler’s max i
mum nominal heat output. The valve is installed in the
safety flow. In Germany, only safety valves with the code
let ter “H” in the approval mark may be connected, and
they must always be connected at the boiler safety flow.
4.9
Supply pump
(boiler with free-standing calorifier)
Speed of rotation and output regulation must correspond
to the requirements of the free-standing calorifier. Setting
car ried out by the heating installation engineer.
4.10 Heating pump
Speed of rotation and output regulation must correspond
to the requirements of the system. They are to be set by
the heat ing installation engineer.
4.11 Heating connections
For boiler rooms adjacent to the domestic sphere, the
heat ing connections on the boiler are to be flexibly con-
nected with compensators.
Содержание 2-Max-3 condens
Страница 24: ...4 215 983 01 24...
Страница 25: ...4 215 983 01 25...