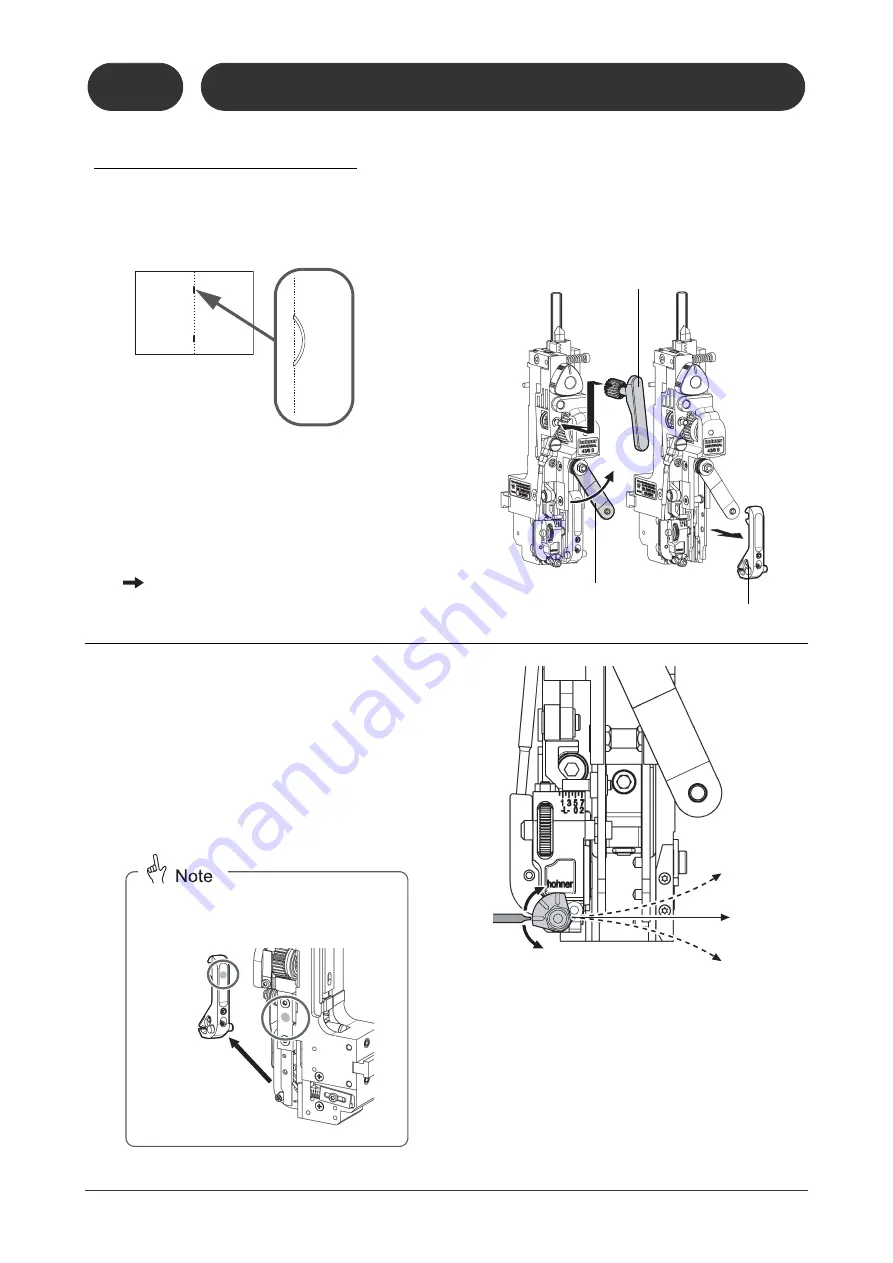
78
4-1
Stitch Adjustments
Wire Straightening Adjustment
The wire is supplied in a coil, so it is not
straight. Adjust the wire so that it comes out
straight.
1
Move the leaf spring to the right
and remove the former.
2
Insert the wire adjusting lever and
turn it clockwise.
This should feed some wire.
- If the wire does not feed, check that the wire
feed On/Off knob is turned to the On position.
3
Adjust the wire so that it comes out
straight.
- Adjust the angle of the eccentric shaft which
feeds the wire.
4
Cut the wire, attach the former and
return the leaf spring to its original
position.
11119
40101M1
11119
40101I1
11119
40101J1
1
1
2
Leaf
Spring
Former
Wire Adjusting Lever
11119
40101L1
11119
40101K1
Attach the former to the same stitcher head.
Each stitcher head and former have paint of
the same color.
Содержание Bookletmaker FC-200A
Страница 84: ...This page is intentionally left blank...
Страница 94: ...This page is intentionally left blank...
Страница 146: ...This page is intentionally left blank...
Страница 202: ...This page is intentionally left blank...
Страница 217: ...This page is intentionally left blank...
Страница 218: ...Manufacturer Phone 81 75 934 6700 Fax 81 75 934 6708 www horizon co jp...