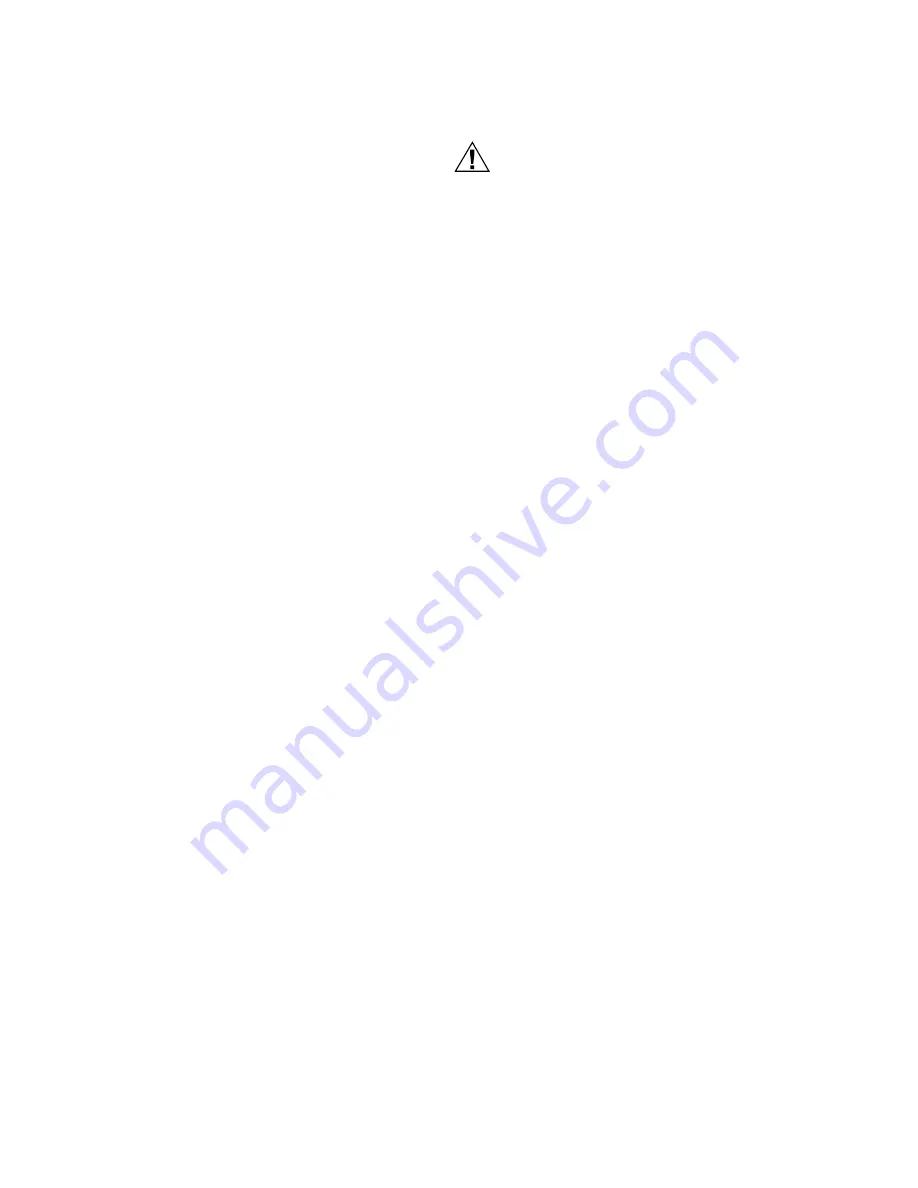
VRW2 DYNAMIC PRESSURE- REGULATING FLANGED CONTROL VALVES
62-3116—01
4
Application Notes
Accurate valve sizing and adjustment is crucial for efficient
system operation. Pressure regulated control valves optimize
hydronic HVAC systems at all load conditions as well as
balancing the system at design conditions.
Low flow rates maximize coil efficiency, but require pressure
regulated valves for stable operation.
High temperature change (
Δ
T) is needed to maintain thermal
transfer at low flow rates, and maximizes efficiencies in chillers
and condensing boilers.
In new construction, low flow rates at high
Δ
T reduce the size
requirements for pumps, chillers, boilers, and piping
components. In retrofit applications, lower flow rates reduce
pump energy consumption and peak power requirements.
Pressure regulated control valves work as effectively as
reverse return piping designs, but use less material.
If a system balancing report is required, coil flow must be
verified by measuring pressure drop across the coil, not the
control valve, using the coil manufacturer's specifications.
Bubble-tight close-off will require use of a resilient-seat
butterfly valve in series with the load.
Proper Use
These valves are only for use in cold, warm, and hot water
systems applications with ethylene glycol or propylene glycol
up to 50% concentration. They are designed for a medium
temperature range of from -4°F (-20°C) to 228°F (120°C) at a
maximum pressure of 580 psig (40 bar). VRW2 valves are to
be operated with supplied multi-turn actuators only.
IMPORTANT
Water should be properly filtered, treated and condi-
tioned according to local conditions and the recom-
mendations of the boiler or chiller manufacturers. The
installation of strainers and side-stream filters is
strongly recommended to protect the pressure regula-
tor cartridge
The presence of excessive iron oxide (red rust) in the
system voids the valve warranty. Rust is highly abra-
sive.
EPDM rubber used in this valve absorbs oil. Do not
use petroleum-based additives and thoroughly flush
system to remove petroleum-based cutting oil, solder
flux, etc. Do not use solvents that will dissolve silicon
grease
INSTALLATION
When Installing this Product...
1.
Read these instructions carefully. Failure to follow them
could damage the product or cause a hazardous condi-
tion.
2.
Check ratings given in instructions and on the product to
ensure the product is suitable for your application.
3.
Installer must be a trained, experienced, licensed service
technician.
4.
After installation is complete, check out product opera-
tion as provided in these instructions
Preparation
CAUTION
Equipment Damage Hazard
• Foreign particles like sand and metal chips can
damage valve seals and regulator diaphragm.
• For trouble-free operation of the product, good
installation practice must include initial system
flushing, and chemical water treatment.
• Use of a 50 micron (or finer) system side stream
filter is recommended and in-line Y-strainers are
suggested. Remove all sieves before flushing the
system to avoid trapping dirt in the filters.
• Acceptable antifreeze solutions, with minimum 50%
water dilution, are diethylene glycol, ethylene glycol,
and propylene glycol.
• Do not use boiler additives, solder flux and wetted
materials which are petroleum based or contain
mineral oil, hydrocarbons, or ethylene glycol
acetate. If in doubt, consult an HVAC water
treatment specialist.
• If installing these valves in a new addition, or if
retrofitting an existing building, do not assume that
the fluid in the existing piping meets these criteria.
1.
Clean the lines upstream of particles larger than 1/16 in.
diameter (welding slag, pipe scale and other contami-
nants).
2.
Proceed with installation once the system specifics
(expansion/contraction of the system and its medium as
well as operating pressures) are within tolerances.
3.
Eliminate air from system. Free oxygen will corrode iron
parts.
IMPORTANT
• Ensure that the valve is not in the fully closed position
when filling the system with water. TURN OFF
POWER and open manually if necessary.
• Do not exceed maximum pressure differential control
range for valve.
• Install valve indoors. If valve is installed outdoors,
water tight protection is required for the actuator.
• If the valve is to be installed in vertical pipe on a
chilled water system, ensure that the covered elec-
tronics are upwards above the valve spindle, to pre-
vent condensation from entering the electronics. If
necessary use a socket and ratchet to remove the
brass nut attaching the mounting bracket to the valve
body, re-position the Actuator and replace the brass
nut.
• Even torque on all flange bolts and connecting rods is
critical to pipe seals.
• Flow arrows must point in the direction of the flow for
proper operation.
4.
Stem rotation as viewed from above:
a. Clockwise to close.
b. Counterclockwise to open
5.
Valve must be mounted with the actuator/bracket above
pipe center line. Do not install the valve with the stem
below horizontal or upside down without NEMA 3, 4, or
4X actuator enclosure to prevent actuator damage due
to condensation or leaks. See Fig. 2 and 3.