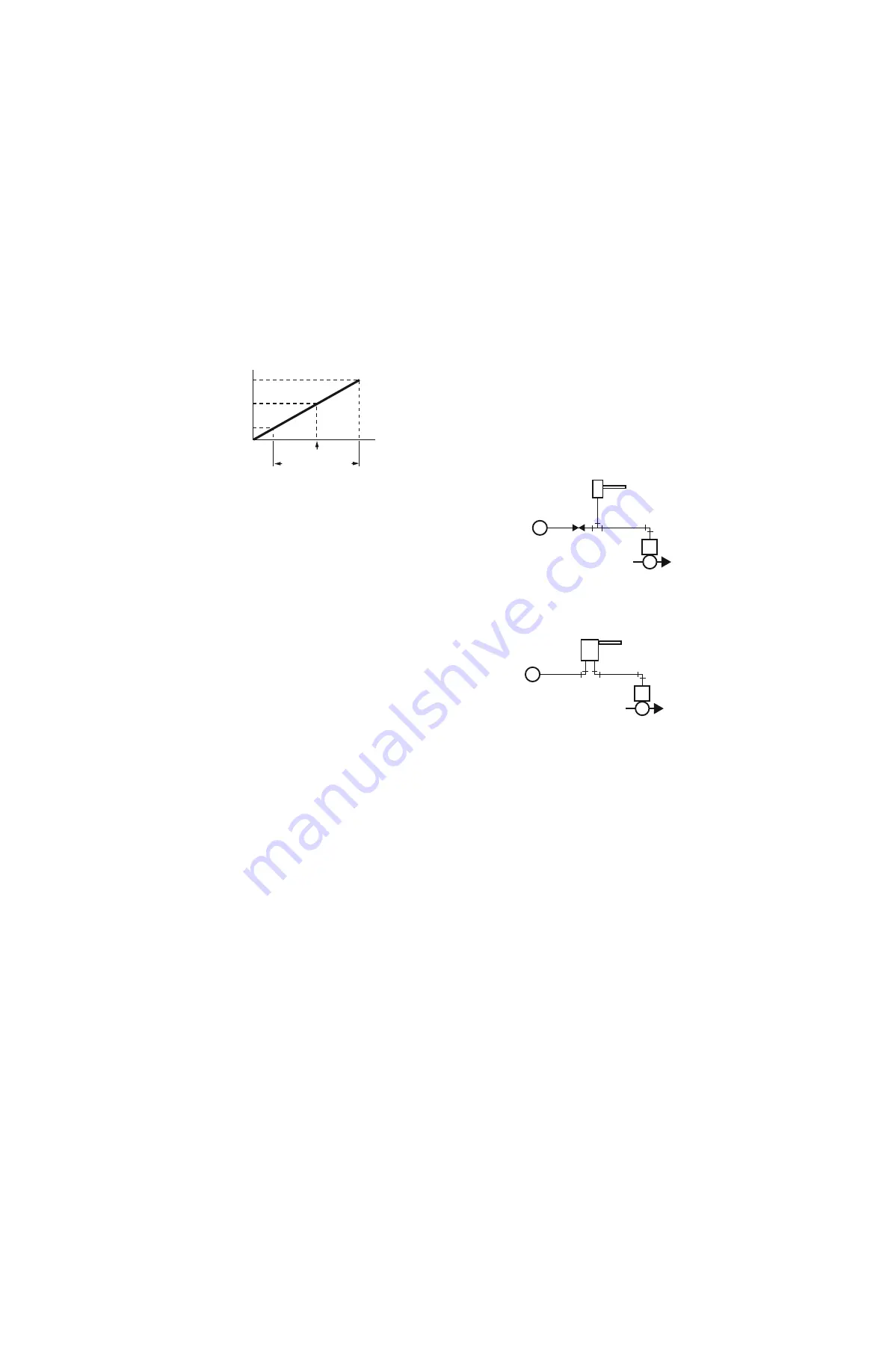
Controllers
134
customer.honeywell.com
70-6925
condition against the nozzle pressure. If the setpoint is
changed, the forces in the lever system are unbalanced and the
room ambient temperature must change in a direction to cause
the bimetal to rebalance the lever system.
Fig. 17. Relationship between Setpoint, Branchline
Pressure, and Throttling Range.
For example, if the setpoint of a direct acting thermostat is
increased, the bimetal reduces the force applied to the flapper
and raises the flapper off the nozzle. This movement causes
the branchline pressure to bleed down and a heating valve to
open. Heat enters the space until the temperature at the
thermostat increases and the force of the bimetal is again in
equilibrium with the opposing force of the pressure at the
nozzle. Decreasing the setpoint causes the reverse to occur.
The throttling range adjustment provides the means for
changing the effective length of the cantilever bimetal in the
lever system. When the throttling range adjustment is
positioned directly over the nozzle, the force of the bimetal
increases and a narrow throttling range or very high sensitivity
results. For example, a change in temperature of 1 degree F
could result in a branchline pressure change of 5 psi.
When the throttling range adjustment is moved toward the end
of the bimetal and away from the nozzle, the force of the
bimetal is reduced. This reduction requires a greater
temperature change at the bimetal to throttle the flapper over
the nozzle. The result is a wider throttling range or very low
sensitivity. For example, a temperature change of 1 degree F
could result in a branchline pressure change of only 1 psi.
CONTROLLERS
General
A controller is the same as a thermostat except that it may have
a remote sensing element. A controller typically measures and
controls temperature, humidity, airflow, or pressure. Controllers
can be reverse or direct acting, proportional or two-position,
single or two pressure, and bleed, feed and bleed, or pilot
bleed.
A two-position controller changes branchline pressure rapidly
from minimum to maximum (or from maximum to minimum) in
response to changes in the measured condition, thus providing
ON/OFF operation of the controlled device.
A proportional controller changes branchline pressure
incrementally in response to a change in the measured
condition, thus providing modulating operation of the controlled
device.
A proportional-integral (PI) controller adds to the proportional
controller a component that takes offset into account. The
integral component eliminates the control point offset from the
setpoint.
Bleed-type controllers can be used in one-pipe or two-pipe
configurations. In a one-pipe system (Fig. 18), the main air goes
through a restrictor to the controller and actuator in the most
expeditious routing. In a two-pipe system (Fig. 19), the main air
goes into the controller, through an internal restrictor in the
controller, and out of the controller through a branchline to the
actuator. All pilot-bleed and feed-and-bleed controllers are two
pipe.
Fig. 18. One-Pipe Controller System.
Fig. 19. Two-Pipe Controller System.
Controllers may also be classified as single-pressure or two-
pressure controllers. Single-pressure controllers use a constant
main air pressure. Two-pressure controllers use a main air
pressure that is alternately switched between two pressures,
such as 13 and 18 psi. For example, occupied/unoccupied
controllers automatically change setpoint from a occupied
setting at a mainline pressure of 13 psi to a lowered unoccupied
setting at 18 psi. Heating/cooling controllers change from
reverse acting at mainline air pressure of 13 psi for cooling to
direct acting at 18 psi for heating.
Temperature Controllers
Temperature controllers can be one- or two-pipe. The sensing
element is typically bimetal, liquid filled remote bulb, or liquid
filled averaging capillary tube. Dimensional change of the
element with temperature change results in flapper position
change and therefore, pilot and branch pressure change.
Humidity Controllers
Principles that apply to temperature controllers also apply to
humidity controllers. The primary difference between
temperature and humidity controllers is in the type of sensing
element. The sensing element in a humidistat is usually a band
of moisture-sensitive nylon. The nylon expands and contracts
with changes in the relative humidity of the air.
THROTTLING RANGE
0
3
8
13
SETPOINT
NOTE: SETPOINT IS AT MIDDLE OF
THROTTING
RANGE
BRANCHLINE PRESSURE (PSI)
C1091
C2342
MAIN
BRANCH
VALVE
CONTROLLER
M
C2343
MAIN
BRANCH
VALVE
CONTROLLER
M B
M
Содержание VP525C
Страница 58: ...50 customer honeywell com 70 6925 ...
Страница 120: ...112 customer honeywell com 70 6925 ...
Страница 166: ...158 customer honeywell com 70 6925 ...