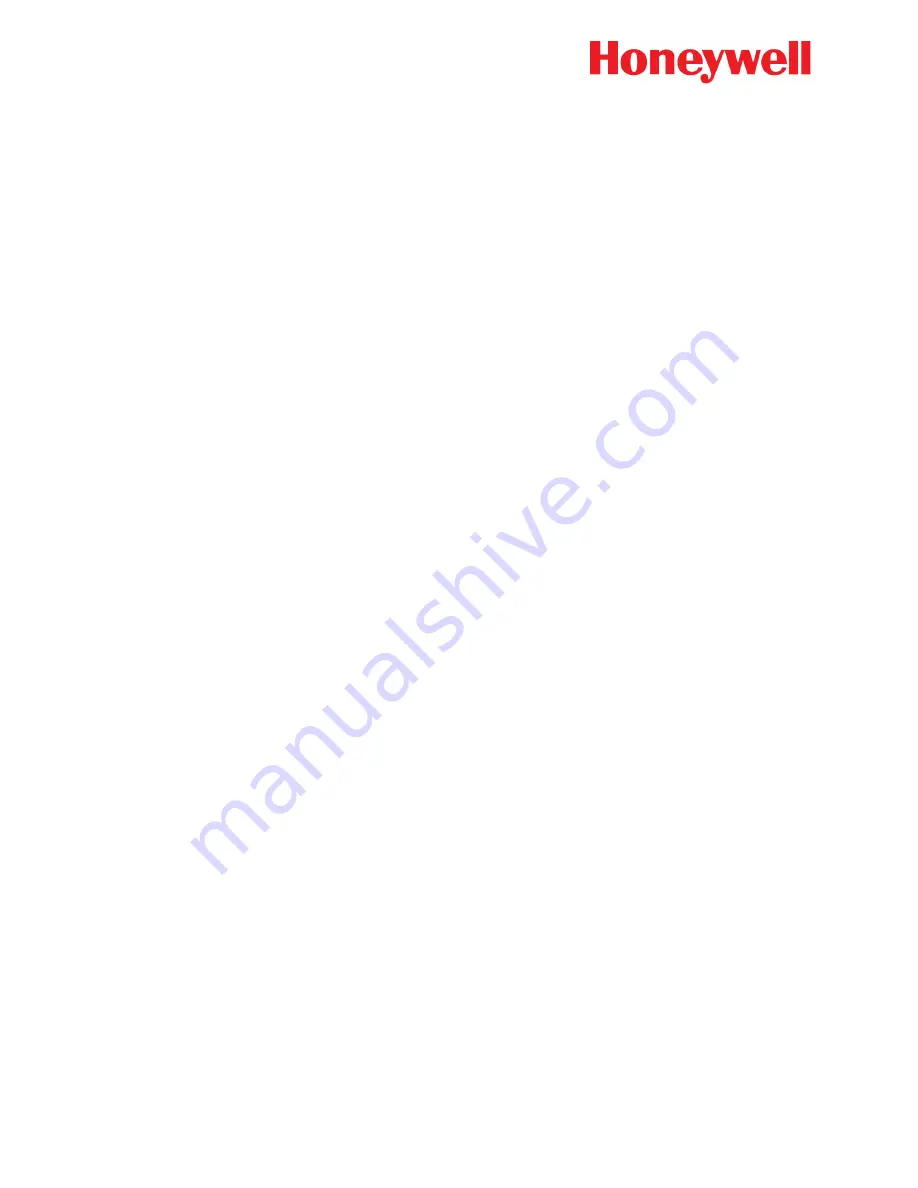
Electrochemical Ammonia (NH
3
) Leak Detector
EC-FX-NH3
Instruction and Installation Manual
Part No. 1998M0872
Revision 1
June 2014
Honeywell Confidential & Proprietary This work contains valuable, confidential, and proprietary information.
Disclosure, use or reproduction outside of Honeywell Inc. is prohibited except as authorized in writing. This
unpublished work is protected by the laws of the United States and other countries.
Содержание EC-FX-NH3
Страница 2: ......
Страница 17: ...OPERATOR MANUAL Figure 3 RS 485 Communication and Power Wiring Diagram 15 ...
Страница 32: ...OPERATOR MANUAL Figure 8 Troubleshooting 30 ...