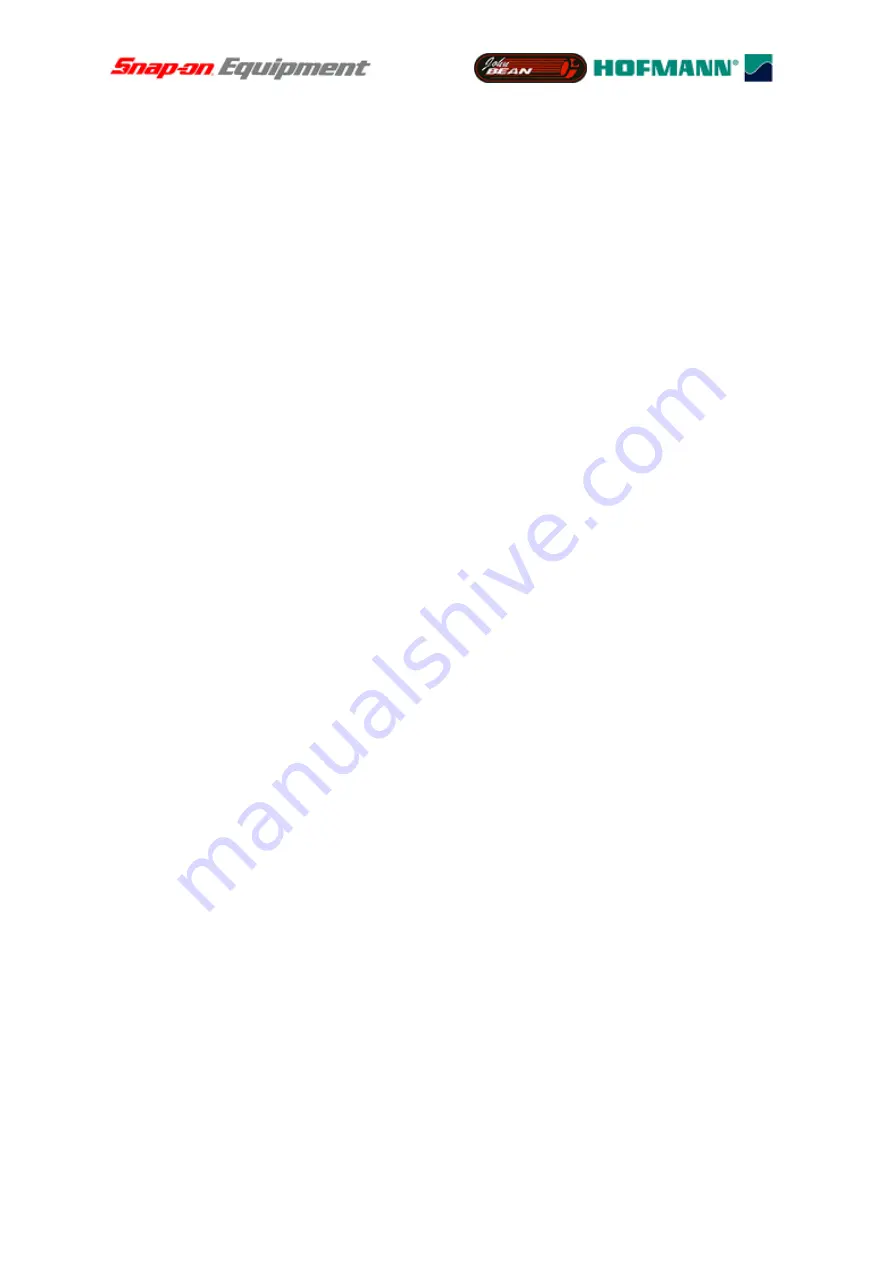
be used for the insulation test.
To obtain and keep good insulation, transducers, cable harness and connector X3 have to be
kept clean. The collars should be positioned vertically below the transducers, to keep dust
from the contacts (6-aclock position).
For disconnecting the wires, the two plugs have to be removed using a pointed device like a
scriber. Insert the scriber in the slot of the collar just above the wire and lift off the plug. To
pull out the wires, take hold of it at both sides of the collar to avoid warping of the terminals.
Keep the plugs with the transducer or as spare parts.
As the transducers take pressure forces only, they are clamped into the vibratory assembly
under mechanical pre-load, which is greater than the maximum forces produced by unbalance.
The forces are conveyed via 8-mm balls to the thrust spreading members, so that lateral
movement does not introduce forces on the piezo disc.
ATTENTION! With an already calibrated balancer, twisting the transducers can adversely
effect plane separation.
Fitting and pre-stressing the transducers
Tools required: Hexagon keys 2.5-mm and 5-mm, open-end wrench 17-mm across the flats.
The transducer attached to wires 11 and 12 of connector X3 is placed in the front; the one
attached to wires 15 and 16 is placed in the rear of the vibratory assembly.
To fit and mechanically pre-load a transducer, carry out the following steps:
a) The two setscrews M10x1x29 (Snap-on P/N EAM0005D07A, HOFMANN Mat-Nr.
1528370) with ball sockets (inverse cones) should be screwed into the vibratory plate
of 20-mm thickness and the rigid support plate welded to the cabinet.
b) Put some stiff grease in the recesses at both ends of the transducer.
Put balls of 8-mm Ø in the recesses (Snap-on P/N 8-1144, HOFMANN Mat-Nr.
1317080).
c) Insert the transducer in the jog of the vibratory plate with one of the balls contacting
the indentation opposite the setscrew. Tighten the setscrew until the transducer is
centred.
d) Screw on the locknut M10x1 (17-mm across the flats), but do not tie up yet. At the
rigid support plate, a nut M10x1 of 5-mm thickness (Snap-on P/N 1-11833,
HOFMANN Mat-Nr. 1556106), at the front with the slightly slant screw; a nut of 8-mm
(Snap-on P/N1-4034, HOFMANN Mat-Nr. 1556101) is used.
e) Adjust the M10x1 screw, so that the transducer is held firmly but can be twisted easily
using two fingers.
Fasten the locknut. To prevent the setscrew to turn, hold it with the hexagon wrench
5-mm inserted.
f)
Put the steel leaf spring on the setscrew M10, with the counterpunch visible. Fasten it
using two countersunk head screws M4.
Drive in the screws M4, so that the leaf spring is in equal distance at both ends but not
bend in the middle.
g) While twisting the transducer with two fingers back and forth, fasten the screws M4
that an effect on slewability is felt.
h) Align the leaf spring to be in parallel to the vibratory plate.
The screws M4 have to be in the middle of the bores behind the leaf springs.
Whatsoever, neither the screws M4 nor the leaf springs should touch the vibratory or
support plate.
i)
Turn the transducer, so that the collar, protecting the cable connection, is pointing
downwards (six a clock position).
Seite 17 von 99
Содержание Snap-on Y2k
Страница 1: ...SERVICE of the Y2k balancing platform Seite 1 von 99 ...
Страница 2: ...The vibratory assemblies of the Y2k balancing platform L R L R S S M Seite 2 von 99 ...
Страница 10: ...S S M Fig 12 Two systems arranged one above the other with a parallel pair of springs Seite 10 von 99 ...
Страница 32: ......
Страница 35: ...Seite 35 von 99 ...
Страница 66: ...Seite 66 von 99 Figure 1 JBEG B9000 B9450 User Interface ...
Страница 67: ...Seite 67 von 99 Figure 2 JBEG B9460 User Interface ...