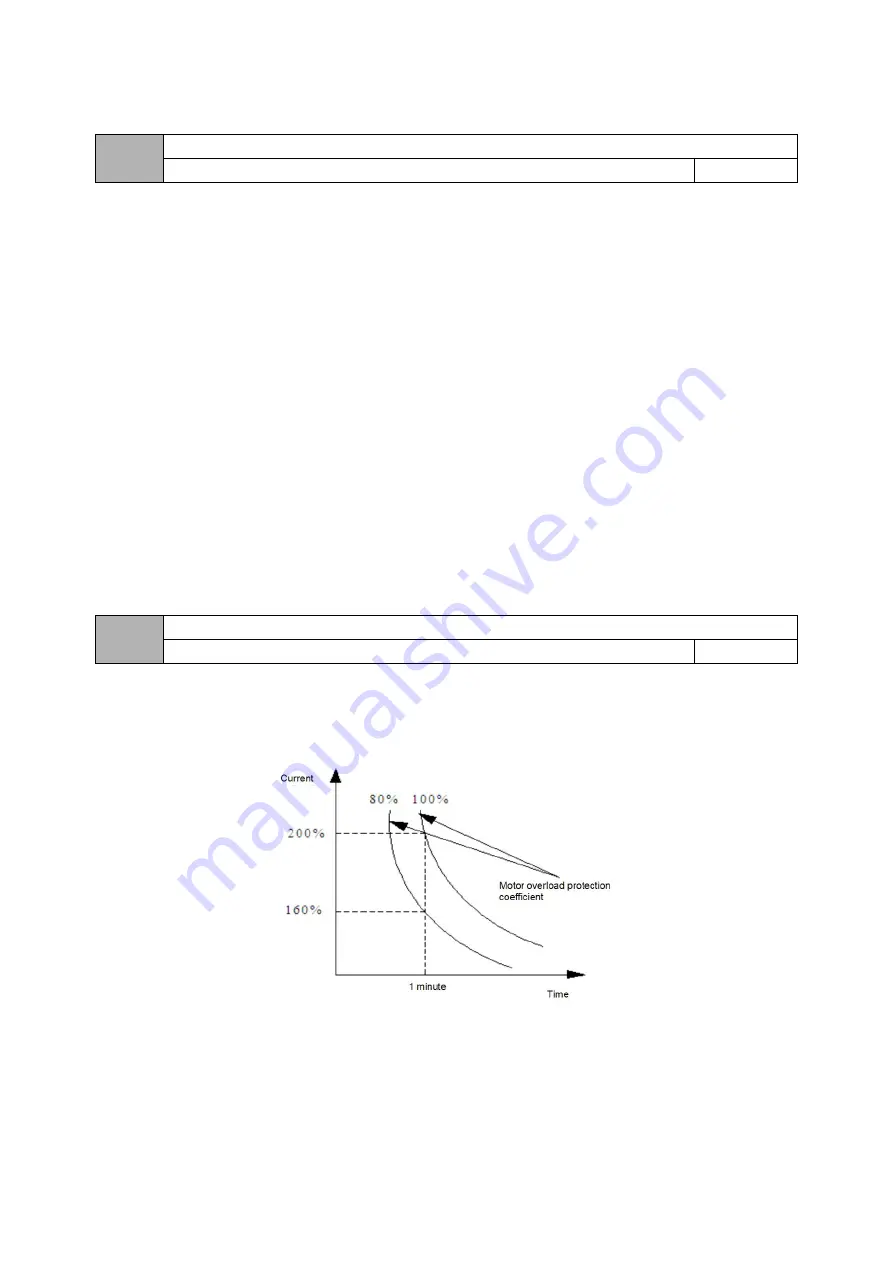
56
05 Group- Protective Function parameters
05.00
Protection settings
0000
~
1211
0001
LED unit: motor overload protection option
0: invalid
There is no motor overload protection (use with caution).
1: Valid
As the heat dissipation effect of ordinary motors becomes worse at low speed, the corresponding motor thermal protection value should also be adjusted
appropriately. The low-speed compensation feature mentioned here is just
It is to lower the overload protection threshold of the motor whose operating frequency is lower than 30Hz.
LED Ten bits: PID feedback disconnection protection
0: invalid
1: protection action and free stop
LED hundred bits: 485 communication failure handling
0: protection action and free stop
1: alarm but maintain the status operation;
2: alarm and stop in the set way
LED thousand bits: Oscillation Suppression
0: invalid
1: valid
When the oscillation suppression is effective, the PWM mode is forced to five-stage.
05.01
Motor overload protection coefficient
30
%~
110
%
100%
In order to implement effective overload protection for different types of load motors, it is necessary to reasonably set the overload protection coefficient of the
motor and limit the maximum current value that the inverter can output. The motor overload protection factor is the percentage of the rated current value of the motor to
the rated output current value of the inverter.
When the inverter drives a motor with a matching power level, the motor overload protection coefficient can be set to 100%. As shown below:
Figure 05-1 Motor overload protection curve
When the capacity of inverter is larger than that of motor, in order to implement valid overload protection for load motors of different specifications, it is necessary to
set the overload protection coefficient of motor reasonably as shown in the following figure: