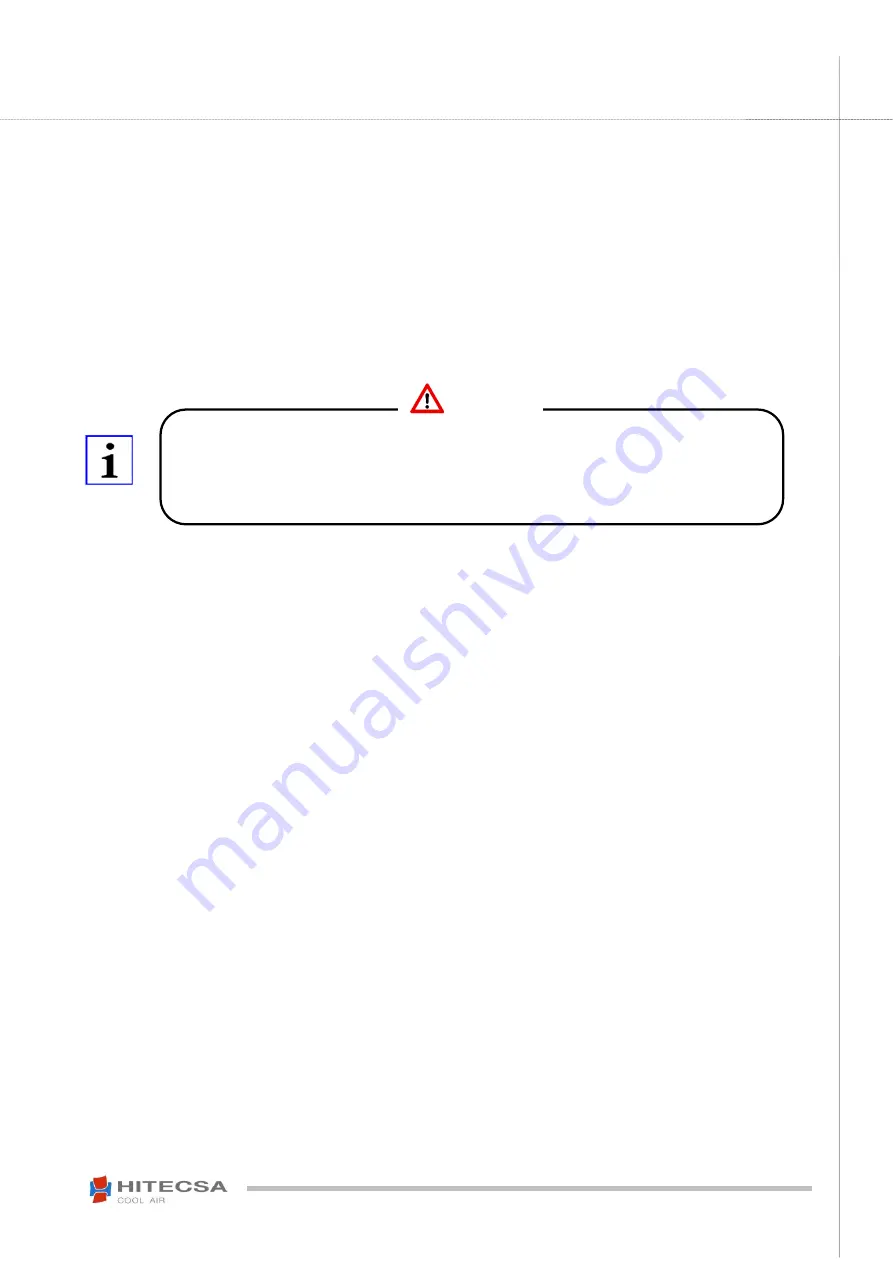
35
IOM_ACVBA-ACVA_351a2402_207958_180109_EN
ACVBA-ACVA
PACKAGED VERTICAL COMPACT UNITS
AIR-AIR
OPTIONAL
EC MOTOR FANS
Rotation caused by an air flow in false direction
When the fan is stopped (no signal, no electrical supply, etc.), the control of the motor does not interfere if the fan rotates
in the wrong direction (due to, for example, an air flow).
If you switch the fan on while it is rotating in the opposite direction, firstly the control will reduce the rotations in a controlled
way until it reaches the ‘0’ value (fan stoppage). Then, the control will make a restart in the correct rotation direction.
The higher the number of turns in the opposite direction, the longer the control will need to reach the fan.
In the event that the fan rotates strongly in the opposite direction, it is possible that the control could not start the fan in the
correct rotation direction.
Information
Maintenance and repairs
Trained specialists only are authorised to carry out repairing works.
Wear safety shoes and gloves for handling.
Please observe the safety regulations and the protection rules of the worker by all maintenance and service work
(EN 50 110, IEC 364).
Before working on the fan, this must be disconnected from the power supply and secured against switching back
on!
Keep the airways of the fan free
– danger because of objects dropping out!
No maintenance work when the fan is running!
Depending on the application and the transfer medium the impeller has a natural wear. Deposits on the impeller
can lead to imbalance and thus to damages (danger of endurance fracture). The impeller can disintegrate!
There is a risk that the impeller could break because of the massive corrosion in case of transporting the product
in highly aggressive environment that could not be appropriate for it. The affected impellers for this type of
corrosion have to be replaced immediately.
Deposits on the motor, especially in the refrigerating wings and motor cavities, block an appropriate refrigeration
causing a premature disconnection of the motor. Therefore they have to be removed on time (cleaning).
Maintenance interval in accordance with the degree of contamination of the impeller!
Check the fan regularly in respect of mechanical vibrations (recommended every 6 months). Keep in mind the
limit values indicated on ISO 14694 and perform correction measures in case of exceeding them (e.g. posterior
balance by trained specialists).
Check the impeller, in particular weld-seams, for possible cracks.
Repair, e.g. by welding is prohibited!
The fan or motor is maintenance-
free due to the use of ball bearings with “life-long lubrication”. At the end of the
grease life (30-40.000h approx.) it is necessary to replace the bearing. Please contact our Service Department in
this case as for all other damage (e.g. to the coil or electronics).
Bolted-on wheels and / or wings can only be replaced by authorized manufacturer staff. The manufacturer shall
not be liable for damage caused by incorrect repair work.
A regular inspection is required together with cleaning if needed to avoid the imbalance and obstruction of the condensation
water evacuation openings due to dirt.
Do not switch off the line voltage so that the braking function can prevent rotation of the
fan in reverse (wrong) direction
!
Safe starting of fans is not guaranteed if it is started in reverse. If the application demands
safe starting, the machine manufacturer or owner must prevent reverse driving rotation by
suitable measures.
WARNING!