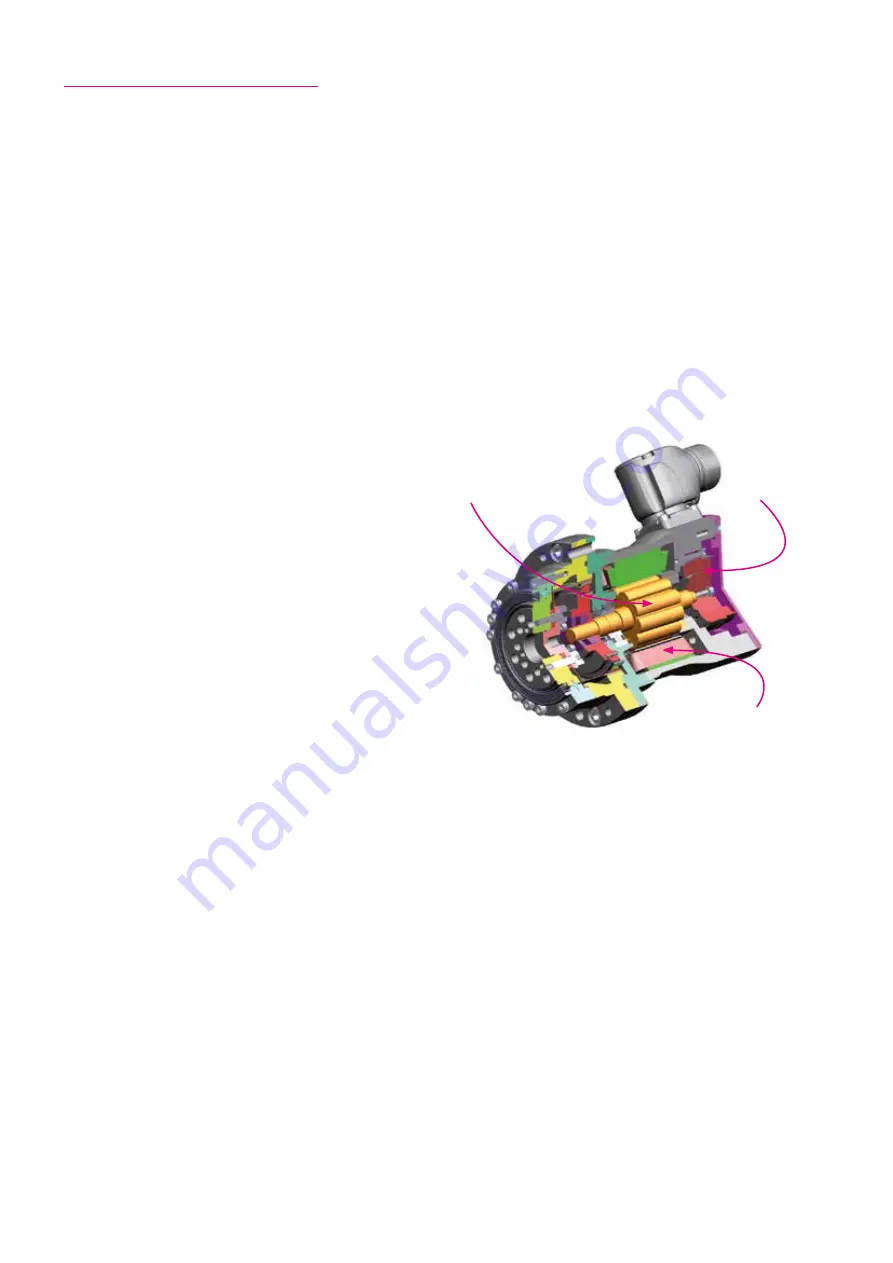
36
1018856
08/2018 V04
6.13 Motor Feedback Systems
Design and Operation
For accurate position setting, the servo motor and its control device are fitted with a measuring device (feedback), which
determines the current position (e.g. the angle of redation set for a starting position) of the motor.
This measurement is effected via a redary encoder, e.g. a resolver, an incremental encoder or an absolute encoder. The
position controller compares the signal from this encoder with the pre-set position value. If there is any deviation, then the
motor is turned in the direction which represents a shorter path to the set value which leads to the deviation being reduced.
The procedure repeats itself until the value lies incrementally or approximately within the tolerance limits. Alternatively, the
motor position can also be digitally recorded and compared by computer to a set value.
Servo motors and actuators from Harmonic Drive AG use various motor feedback systems which are used as position trans-
ducers to fulfil several requirements.
Commutation
Commutation signals or absolute position values provide the
necessary information about the rotor position, in order to
guarantee correct commutation.
Actual Speed
The actual speed is obtained in the servo controller using
the feedback signal, from the cyclical change in position
information.
Actual Position
Incremental encoder
The actual signal value needed for setting the position is for-
med by adding up the incremental position changes. Where
incremental encoders have square wave signals, definition of
the edge evaluation can be quadrupled (quad counting).
Where incremental encoders have SIN / COS signals, then the definition can be increased by interpolation in the control
device.
Absolute encoder
Absolute encoders deliver absolute position information about one (single turn) or several (multi-turn) rotations. This infor-
mation can on the one hand provide the rotor position for commutation and on the other hand possibly a reference of travel.
Where absolute encoders have additional incremental signals, then typically the absolute position information can be read at
power up and the incremental signals then evaluated to determine the rotation and actual position value.
Fully digital absolute encoders as motor feedback systems have such a high definition of the absolute value that there is no
need for additional incremental signals.
Resolution
In conjunction with the Harmonic Drive AG High Precision Gears, the output side position can be recorded via the motor feed-
back system without any additional angle encoders having to be used. The resolution of the motor feedback system can also
be multiplied by gear ratio.
Output Side Angle Measurement Devices
Where applications place higher demands on accuracy or need torsion compensation at high torque load, the actual position
can also be detected by an additional sensor mounted at the gearbox output side. The adaptation of an output side
measurement sytem can be very simply realised for hollow shaft actuators.
Stator
Rotor
Motor feedback