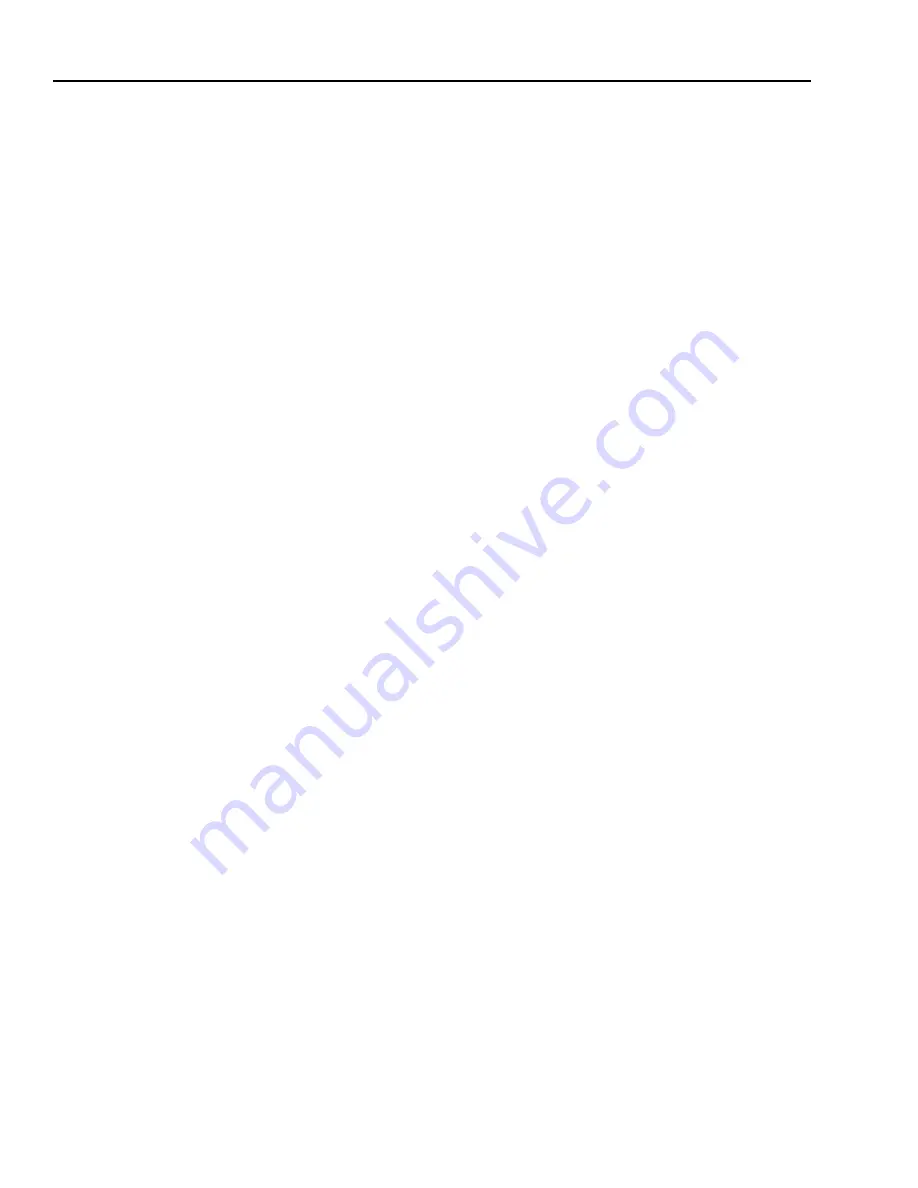
HI 2160RC
PLUS
MANUAL
6-12
•
From the Front Panel Display check the OP% values
while running a batch from the feeder. Calculate REC as
follows:
REC Level
(High OP% - Low OP%) x .01 2
÷
=
•
REC TIME (Seconds) - Rate Exception Control Time used to deter-
mine the time the HI 2160RC
PLUS
must remain in the REC mode to
initiate an alarm condition, energizing the alarm relay.
•
REC Shutoff - Rate Exception Control Shutoff. If “yes” is chosen,
the feeder stops if the controller stays in the REC mode for the
amount of time chosen in REC TIME. If “no” is chosen, the feeder
will continue to run in the REC mode with the alarm relay ener-
gized.
•
Pre-Act Corr. - The Pre-Act Correction compensates for in flight
material when the feeder shuts off in batch operations.
•
Save Data - Stores Configuration, Calibration and Setup parameters
in the Secure Memory Module (SMM).
•
Restore Data - Restores data from the Secure Memory Module
(SMM) to the controller’s conventional memory.
Manual
(Calculating
Parameters)
Tuning Control
Process
•
If you feel that the automatically calculated control constants can
be improved, enter your own control constants in the way you
would enter a numerical value in any Sub-Menu. The Manual Tun-
ing Control is a step-by-step process to arrive at the control con-
stants for your specific application. The values calculated
automatically by the instruments provides optimum values for
almost all applications. Because there are any number of variations
from one application to the next there are a few applications when
the HI 2160RC
PLUS
will not provide optimum values to control your
process. Be sure that new control constants are needed before Man-
ual tuning process. Once you determine the new constants, write
them down in a secure location because they will be replaced auto-
matically the next time a rate calibration takes place.
•
Manual tuning control is a process used to calculate the three con-
stants: K(p), K(i), K(d) which is a two step process:
NOTE:
The tuning process is basically trial and error. There are only two values you need to
adjust: Timebase and Averaging. To insure the changes are going in the right direc-
tion, change one parameter at a time and make incremental changes only. For exam-
ple when changing the Timebase Parameter, change it from 4 to 5, check performance
(Increase Timebase if the expected rate is above 100 mass units/time unit). If the per-
formance improves, go from 5 to 6, 6 to 7, and so on until the performance begins to
degrade. At the level where performance begins to degrade, step back one level for
optimal performance level setting. Conversely when changing the Timebase Parame-
ter, change from 5 to 4, check performance. If the performance improves, go from 4 to
3, 3 to 2, and so on until the performance begins to degrade. At the level where per-
formance begins to degrade, step back one level for optimal performance level set-
ting. If performance improves move onto the next parameter. Do the same process for
changing Averages. (Increase Averages if the weight varies 1% of full scale).
Содержание HI 2160RC PLUS
Страница 1: ...HI 2160RCPLUS Rate Controller Operation and Installation Manual ...
Страница 23: ...HI 2160RCPLUS MANUAL 2 6 ...
Страница 32: ...Chapter 3 Installation 3 9 FIG 3 12 FRONT PANEL WITH BRACKETS FROM FACTORY FIG 3 13 BEZEL INSTALLATION DIAGRAM ...
Страница 46: ...Chapter 3 Installation 3 23 Interconnect Wiring Diagram See Fig 3 33 FIG 3 33 INTERCONNECT WIRING DIAGRAM ...
Страница 48: ...Chapter 3 Installation 3 25 FIG 3 35 SECURE MEMORY MODULE FIG 3 36 INSTALLING REMOVING SECURE MEMORY MODULE ...
Страница 49: ...HI 2160RCPLUS MANUAL 3 26 ...
Страница 67: ...HI 2160RCPLUS MANUAL 4 18 ...
Страница 91: ...HI 2160RCPLUS MANUAL 5 24 ...
Страница 151: ...HI 2160RCPLUS MANUAL 7 12 ...
Страница 187: ...HI 2160RCPLUS MANUAL 8 36 ...
Страница 197: ...1 2 3 4 5 6 V V I I VOLTAGE CURRENT HI 2160RCPLUS MANUAL 9 10 FIG 9 5 CONNECTOR WIRING DIAGRAM FOR CONTROL OUTPUT CARD ...
Страница 207: ...HI 2160RCPLUS MANUAL 9 20 ...
Страница 219: ...Data Worksheets WKSHT 6 ...