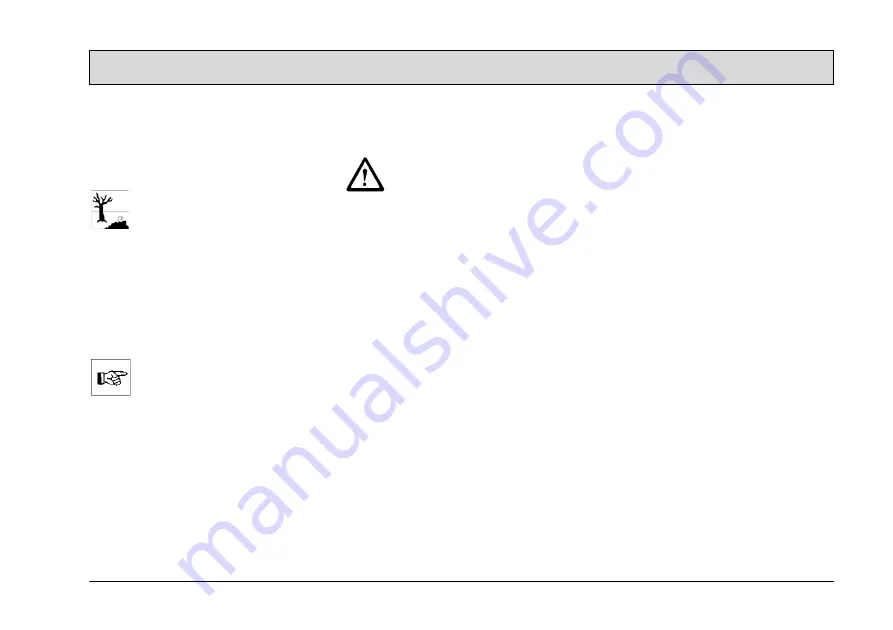
85
Maintenance and Service
5.11
Cleaning the vehicle
• Clean the vehicle on a weekly basis,
refer to Section 5.3.1.
• Park the vehicle in an appropriate
washing area.
Observe the applicable laws
and local regulations when dis-
posing of water containing
cleaning agents and dirt!
• Switch the vehicle off and remove
the key.
• The vehicle may only be cleaned
using a water hose (operating pres-
sure approx. 5 to 6 bar) and only
from top to bottom.
It is not permitted to clean the
vehicle with a pressure washer
or steam blaster.
• Do not aim the jet of water directly at
openings, slits, electronic compon-
ents, operating panels or seals.
• It is not permitted to use aggressive
and corrosive cleaning agents.
• Allow the vehicle to dry after
cleaning. It is preferable to allow the
vehicle to dry over a longer period of
time, e.g. the weekend.
5.12
Transporting and towing
Loading
Check the load bearing capaci-
ty of the loading platform prior
to loading.
• Dead weight of the Hakomatic
B 1050 W without battery, without
options and without driver: 710 kg
• Total weight of the Hakomatic
B 1050 W with battery and filled so-
lution tank, with cab safety roof and
side scrubbing unit, without driver:
1520 kg
• When loading onto a truck or
something similar by means of a loa-
ding ramp, the ramp angle must not
exceed 20%.
• The squeegee and brush head must
be raised.
Transporting the vehicle
• When transporting the vehicle using
lifting gear to the site of use, the
squeegee and rotary brush head
must be raised.
• When the vehicle is to be transpor-
ted on another vehicle or trailer, it
must be secured against rolling
away. Lash the vehicle down secure-
ly.
• There are attachment points for this
on the left as well as on the right: At
the rear on the frame and at the si-
des near the entry point.
• The attachment points are bolts
(Fig. 37/1+2) which can be pulled out
from the sides of the frame. The bolts
are locked in their projecting position
by turning them.
• The bolts also serve for loading by a
crane.