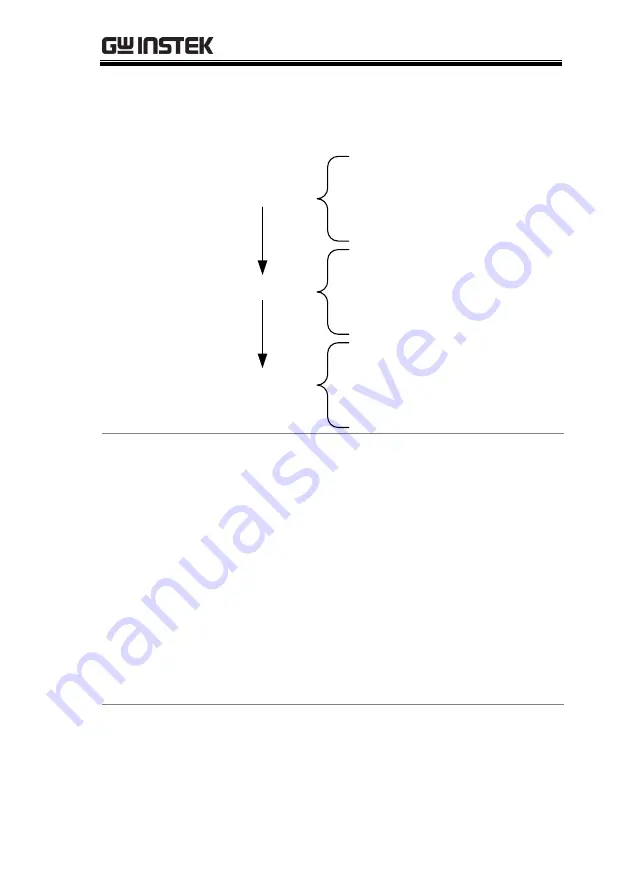
FUNCTION MENU
119
Program chains need not be executed in order.
There are 16 steps to a program.
There are up to 16 programs to a chain.
PROGRAM 1
STEP 01
STEP 02
:
STEP 16
PROGRAM 2
STEP 01
STEP 02
:
STEP 16
PROGRAM 3
STEP 01
STEP 02
:
STEP 16
Setting Overview
A program contains the following settings for each
step:
Memory: the memory location of the load
operation for the selected step (M001-M256).
Run: Designates the run setting for the step
(Auto, Manual, Skip).
On-Time: Sets the run time of the test.
Off-Time: Sets the off time between steps.
P/F-Time: Sets the testing pass/fail delay time
for GoNo Go testing.
Short-Time: Sets the shorting time for the step,
if any.
Timing Diagram
for Single Step
Below is a timing diagram of a single step in a
program.
Содержание PEL-3000 Series
Страница 1: ...DC Electronic Load PEL 3000 H Series USER MANUAL VERSION 2 00 ISO 9001 CERTIFIED MANUFACTURER ...
Страница 24: ...PEL 3000 H User Manual 22 PEL 3111H PEL 3211 Booster Pack PEL 3211H Booster Pack ...
Страница 29: ...GETTING STARTED 27 GRA 413 JIS standard 149 532 5 482 6 GRA 414 E EIA standard 132 382 5 477 6 ...
Страница 41: ...GETTING STARTED 39 Fasteners 2 ...
Страница 207: ...REMOTE CONTROL 205 6 7 8 9 The function check is complete ...
Страница 209: ...FAQ 207 For more information contact your local dealer or GWInstek at www gwinstek com marketing goodwill com ...
Страница 229: ...APPENDIX 227 Operating Area PEL 3021 ...
Страница 230: ...PEL 3000 H User Manual 228 PEL 3041 ...
Страница 231: ...APPENDIX 229 PEL 3111 ...
Страница 232: ...PEL 3000 H User Manual 230 PEL 3211 Booster Pack PEL 3021H ...
Страница 233: ...APPENDIX 231 PEL 3041H ...
Страница 234: ...PEL 3000 H User Manual 232 PEL 3111H PEL 3211H Booster Pack ...
Страница 235: ...APPENDIX 233 ...