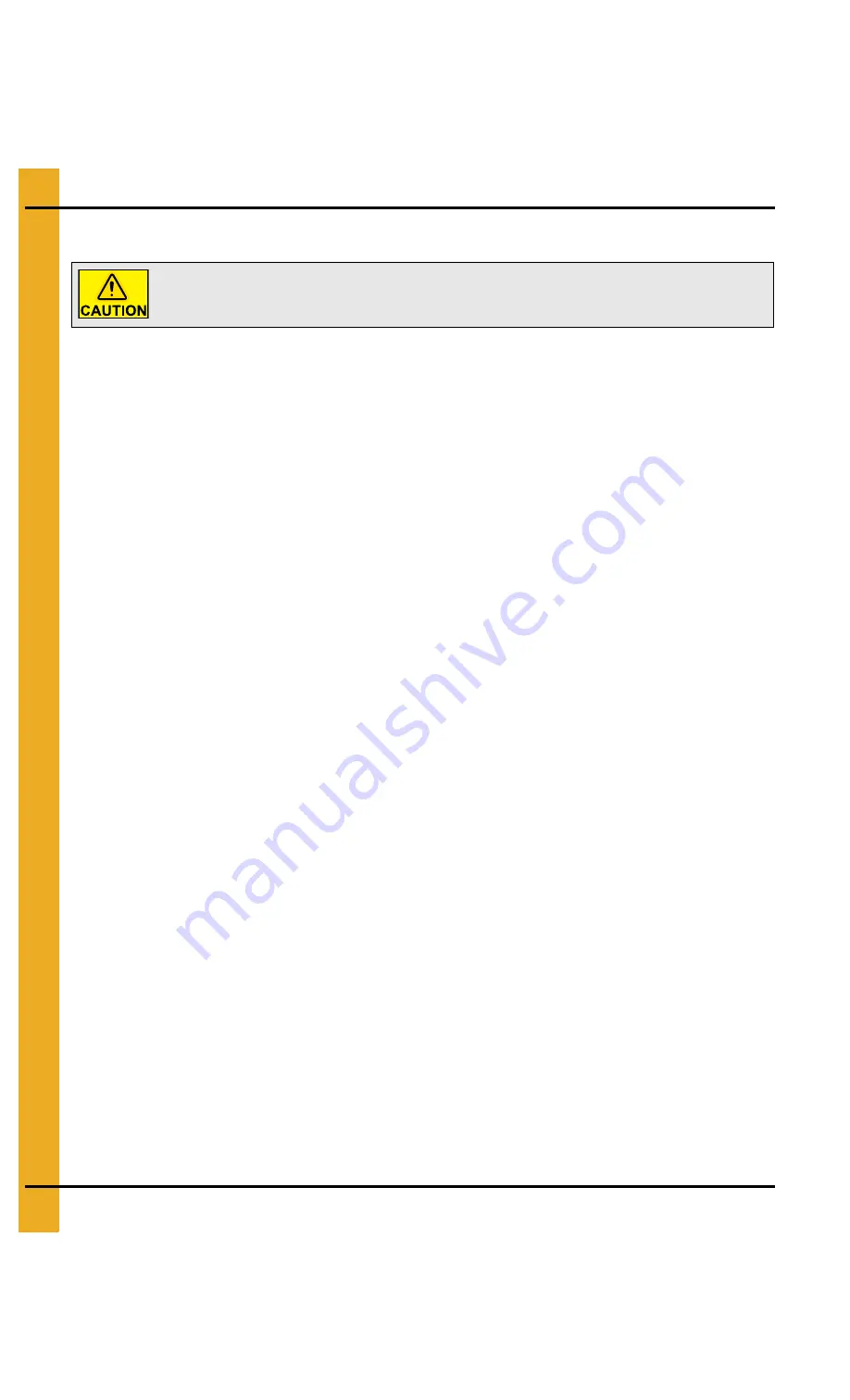
7. Maintenance and Repair
28
PNEG-2174
Sampler - Model GRA
Draining and Servicing the Filter
Drain the accumulated fluid whenever the fluid level in the reservoir (quiet-zone) rises to the lower baffle.
Filters have either a screw-type drain or a push-type drain. If the filter requires frequent draining, consider
installing an automatic drain or an air drying system. Periodically, the bowl may need to be removed to
clean out accumulated moisture and contaminants.
1. Shut off and lock out the air supply.
2. Operate a valve or loosen an airline connection to relieve all pressure downstream from the
filter/regulator.
3. Remove and clean the bowl, various types of clamp rings or threaded collars are used to retain bowls.
NOTE:
The bowls of filter/regulators can not be removed while pressurized. Internal pressure
prevents the clamp ring or threaded collar from turning.
4. Clean or replace the filter element.
5. If the bowl seal is damaged or brittle replace it. In any event lightly coat the seal with petroleum-based
grease to help hold it in position.
6. Re-install the bowl. Turn ON pressure and make sure the bowl is seated and sealed.
Mechanical Repair Procedures
Sample Cutter Blade Replacement
When following the instructions below, refer to the applicable drawing of the sampler. Reference the
section drawings of the samplers
and the certified drawing(s).
1. Shut off and lock out all power (electrical and pneumatic).
2. Shut down conveying line and remove the large inspection cover on the sampler housing.
3. Move the sample pelican to the middle of its travel.
4. Remove the 1/4''-20 UNC hex head bolts fastening the sample cutter to the sample pelican.
5. Using a utility knife, cut the caulking seal around the bottom of the cutter blade and remove.
6. Note the taper of the cutter blade opening. Install the new cutter blade on the sample pelican with
narrow part nearest the drive shaft.
7. Re-install the 1/4''-20 UNC hex head bolts fastening the sample cutter to the sample pelican.
8. Re-caulk the joint between the cutter blade and the sample pelican to ensure a tight seal.
9. Move the sample pelican to its home position on each side and check to see that the cutter fits snugly
under the pelican seals.
10. Re-install the inspection cover on the housing.
11. Restore power to the sampler and operate it through several collection cycles.
Escape of pressurized air, fluids and contaminants at high velocity can cause injury
to unprotected eyes. Always wear eye protection when draining a filter.