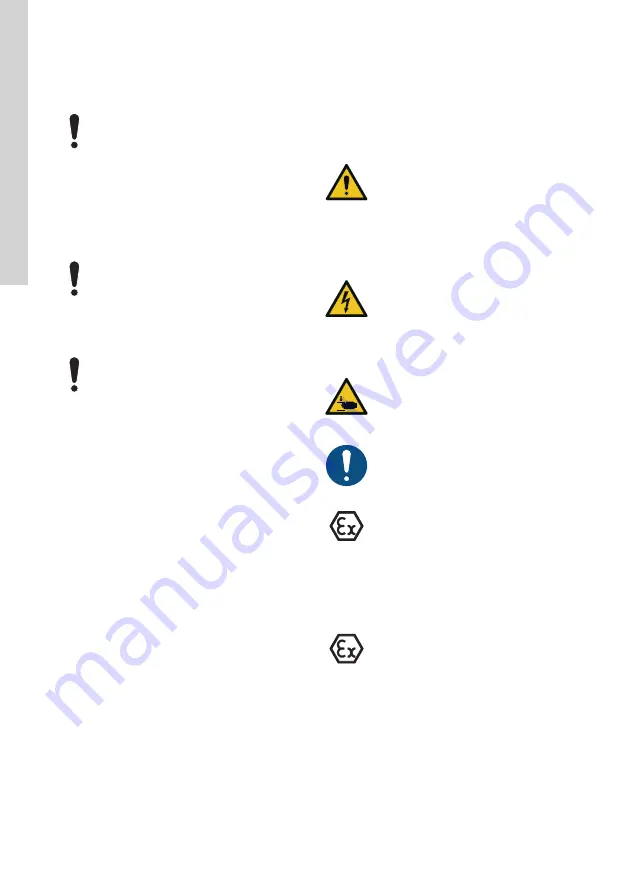
7.2 Storing the product
Leave the cable end protectors and the
control cables on the power until the elec-
trical connection is made. The free cable
ends must never be exposed to moisture
or water.
Neglecting this may cause damage to the
motor.
For long periods of storage (six months or longer), the
pump must be protected against moisture and heat.
If the pump is being stored for more than
two months, turn the impeller by hand at
least every two months to prevent the seal
faces of the lower mechanical shaft seal
from seizing up.
Neglecting this may cause damage to the
shaft seal when the pump is started.
If the impeller cannot be turned by hand,
contact an authorised service workshop.
For dry-installed pumps, make sure the
cooling jacket is empty before storing the
pump.
After a long period of storage (six months or longer),
inspect the pump before putting it into operation.
Make sure that the impeller can rotate freely. Pay
attention to the condition of the shaft seals, O-rings
and cable entries.
8. Servicing and maintaining the
product
8.1 Safety instructions and requirements
DANGER
Crushing hazard
Death or serious personal injury
‐
During maintenance and service, in-
cluding transport to service workshop,
always support the pump by lifting
chains or place it in horizontal position
to secure stability.
DANGER
Electric shock
Death or serious personal injury
‐
Before starting work on the pump,
make sure that the main switch is
locked in position 0. Make sure that the
power supply cannot be switched on
unintentionally.
WARNING
Crushing hazard
Death or serious personal injury
‐
Make sure that all rotating parts have
stopped moving.
Maintenance and service must be carried
out by trained persons.
Compliance with the standards IEC
60079-17 and IEC 60079-19 is a customer
responsibility.
Maintenance and service work on explo-
sion-proof pumps must be carried out by
Grundfos or an authorised service work-
shop.
In case of repairs, always use original
service parts from the manufacturer to en-
sure the correct dimensions of the flame
path gaps.
The bolts used in the motor must be class
A4-80 or A2-80 according to EN/ISO
3506-1. VER 2.
A defective bearing may reduce the Ex
safety.
32
English (GB)
Содержание ST-55-520
Страница 2: ......