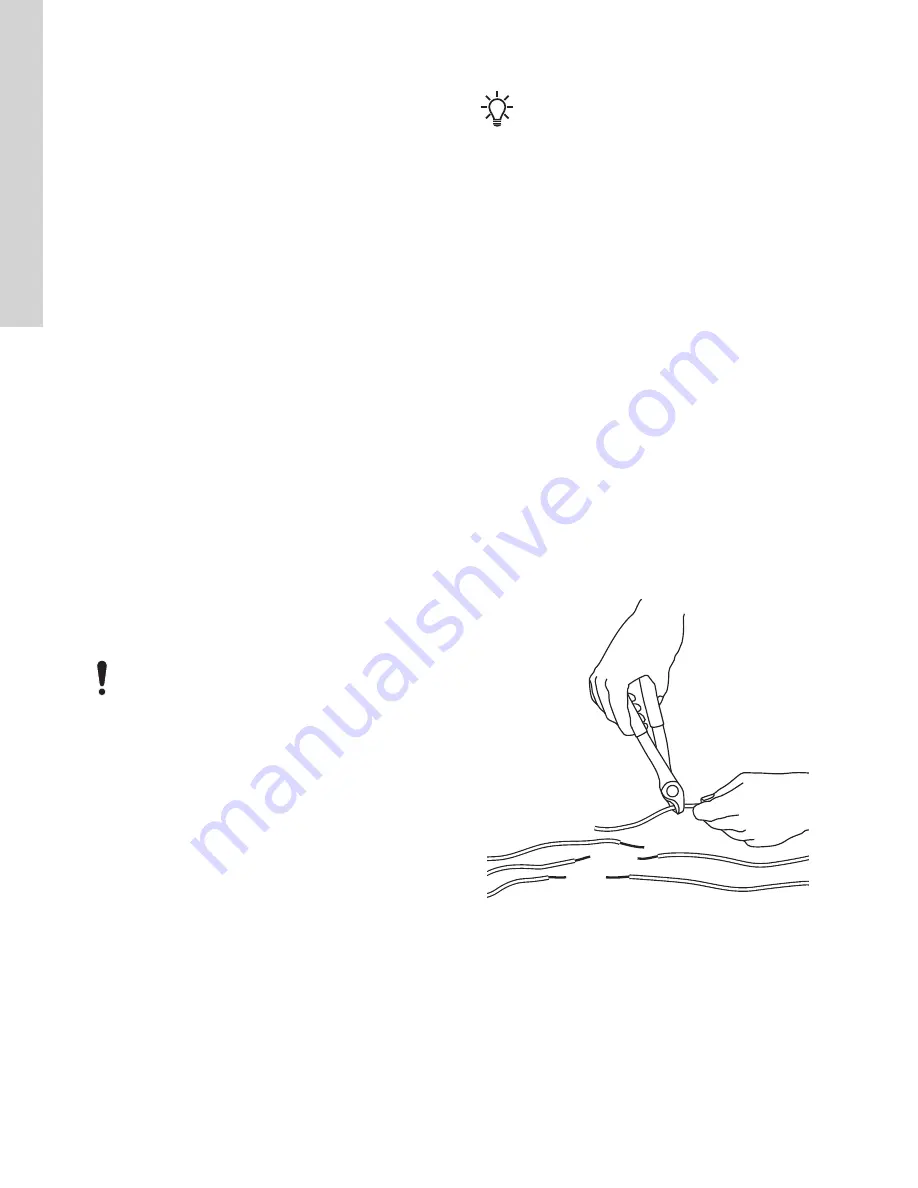
6.3.5 Installation depth
Make sure that the installation depth of the pump is always at least
3 ft (1 m) below the maximum draw-down level of the well. For flow
rates exceeding 100 gpm (22.7 m
3
/h), refer to the performance
curves for recommended minimum submergence.
Never install the pump so that the bottom of the motor is lower than
the top of the well screen or within 5 ft (1.5 m) of the well bottom.
If the pump is to be installed in a lake, pond, tank or large diameter
well, make sure that the water velocity passing over the motor is
sufficient to ensure proper motor cooling. The minimum
recommended water flow rates ensuring proper cooling are listed in
section Maximum water temperature.
Related information
10.1.1 Maximum water temperature - minimum velocity/flow past
the motor
6.3.6 Power supply
Check the motor voltage, phase number and frequency indicated on
the motor nameplate against the actual power supply.
6.3.7 Power cable type
The power cable used between the pump and the control box or
control panel must be approved for submersible pump applications.
Conductors may be solid or stranded. The cable may consist of
individually insulated conductors twisted together, insulated
conductors molded side by side in one flat cable or insulated
conductors with a round overall jacket.
The conductor insulation must be type RW, RUW, TW, TWU or
equivalent and must be suitable for use with submersible pumps.
An equivalent Canadian Standards Association (CSA) certified
cable may also be used.
Related information
10.4 Submersible drop cable selection charts (60 Hz)
6.4 Removing and fitting the cable guard
If the cable guard is attached with screws, remove the screws to
loosen it. To fit the cable guard on the pump, tighten the screws to
fit it securely to the pump. See Appendix A for further details.
Make sure that the pump chambers are aligned when the
cable guard has been fitted.
6.5 Splicing the motor cable
A good cable splice is critical to proper operation of the
pump.
If the splice is carefully made, it works as well as any other portion
of the cable, and is completely watertight. Use a heat shrink splice
kit. Make the splice in accordance with the kit manufacturer's
instructions. Typically a heat shrink splice can be made as follows:
1. Check the motor - and the submersible drop cables for damage.
2. Cut the motor leads off in a staggered manner. Cut the ends of
the drop cable so that the ends match up with the motor leads.
See the figure Cutting and stripping the motor leads below. On
single-phase motors, make sure to match the colors.
3. Strip back and trim off 1/2 inch of insulation from each lead,
making sure to scrape the wire bare to obtain a good
connection. Be careful not to damage the copper conductor
when stripping off the insulation.
4. Slide the heat shrink tubing on to each lead. Insert a properly
sized "Sta-Kon" type connector on each lead, making sure that
lead colors are matched. Using "Sta-Kon" crimping pliers, indent
the lugs. See the figure Crimping the connectors below. Make
sure to squeeze hard on the pliers, particularly in the case of a
large cable.
5. Center the heat shrink tubing over the connector. Using a
propane torch, lighter, or electric heat gun, uniformly heat the
tubing starting first in the center working towards the ends. See
the figure Applying heat to the connector below.
6. Continue to apply the heat to the tubing. Make sure not to let the
flame directly contact the tubing. When the tubing shrinks and
the sealant flows from the ends of the tubing, the splice is
complete. See the figure Completed splices below.
TM050032_061
1
Cutting and stripping the motor leads
12
English (US)
Содержание SP 1100S
Страница 2: ......