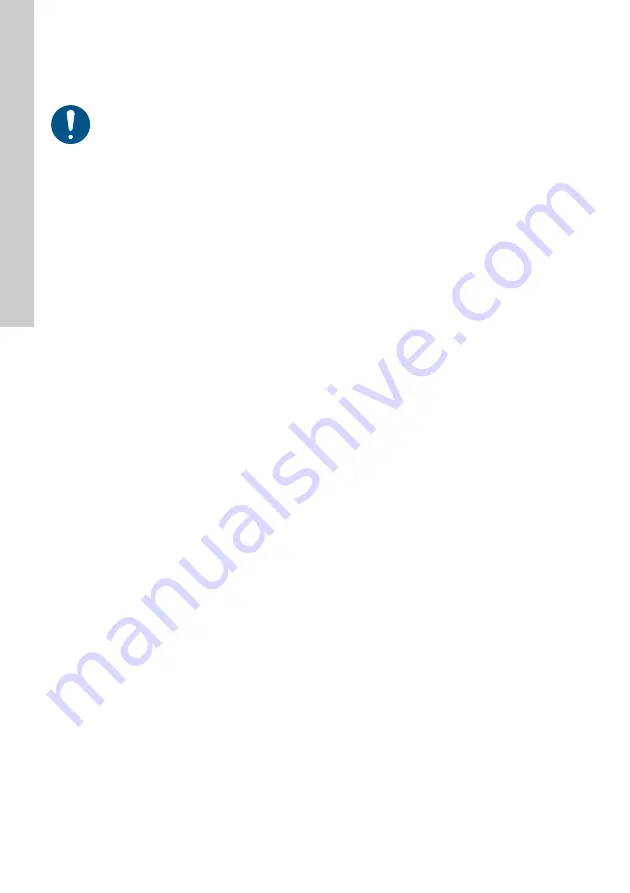
En
gl
is
h (
G
B)
10
3.4.2 Inlet pipes
Place the pump below system liquid level whenever
possible. This will facilitate priming, assure a steady
liquid flow and provide a positive suction head.
You can avoid many NPSH problems if you install the
inlet pipe properly. See section
.
In section
, common
inlet pipe installations are illustrated for two
situations:
•
flooded systems
Closed systems and open systems where the
liquid level is above the pump inlet.
•
suction lift systems
Closed systems and open systems where the
liquid level is below the pump inlet.
3.4.3 Valves in the inlet pipe
If the pump is operating under permanent suction lift
conditions, install a non-return valve in the inlet pipe
to avoid having to prime the pump each time it is
started. The non-return valve must be of the flap type
or a foot-valve with a minimum of pressure loss.
3.4.4 Outlet pipe
The outlet pipe is usually preceded by a non-return
valve and an isolating or throttle valve. The
non-return valve protects the pump against
excessive counterpressure and reverse rotation of
the pump and prevents backflow through the pump in
case of operational stop or failure of the motor.
In order to minimise friction losses and hydraulic
noise in the pipes, flow velocities must not exceed 3
m/s in the outlet pipe (port).
On long horizontal runs, keep the pipe as level as
possible.
Avoid high spots, such as loops, as they will collect
air and throttle the system or lead to uneven
pumping.
3.4.5 Auxiliary pipes
Drains
Install the drain pipes from the pump casing and
stuffing boxes to a convenient disposal point.
Flushing pipes
•
Pumps fitted with stuffing boxes
When the inlet pressure is below the ambient
pressure, supply the stuffing boxes with liquid to
provide lubrication and prevent the ingress of air.
This is normally achieved via a flushing pipe from the
outlet side to the stuffing box. You can fit a control
valve or orifice plate in the flushing pipe to control
the pressure to the stuffing box.
If the pumped liquid is dirty and cannot be used for
flushing the packing rings, we recommend a
separate clean, compatible liquid supply to the
stuffing box at 1 bar above the inlet pressure.
•
Pumps fitted with mechanical seals
Seals requiring recirculation will normally be
provided with a flushing pipe from the pump casing.
3.4.6 Measuring instruments
To ensure continuous monitoring of operation, we
recommend that you install pressure gauges on the
pump inlet and outlet flanges. The pressure gauge
on the inlet side must be capable of measuring
vacuum. The pressure tappings must only be opened
for test purposes. The measuring range of the outlet
side pressure gauge must be minimum 20 % above
the maximum pump outlet pressure.
When measuring with pressure gauges on the pump
flanges, note that a pressure gauge does not register
dynamic pressure (velocity pressure). The diameters
of the inlet and outlet flanges are different, and this
results in different flow velocities in the two flanges.
Consequently, the pressure gauge on the outlet
flange will not show the pressure stated in the
technical documentation, but a value which may be
lower.
The sizing and installation of the inlet pipe
is extremely important.
Содержание LSV Series
Страница 57: ...57 ...