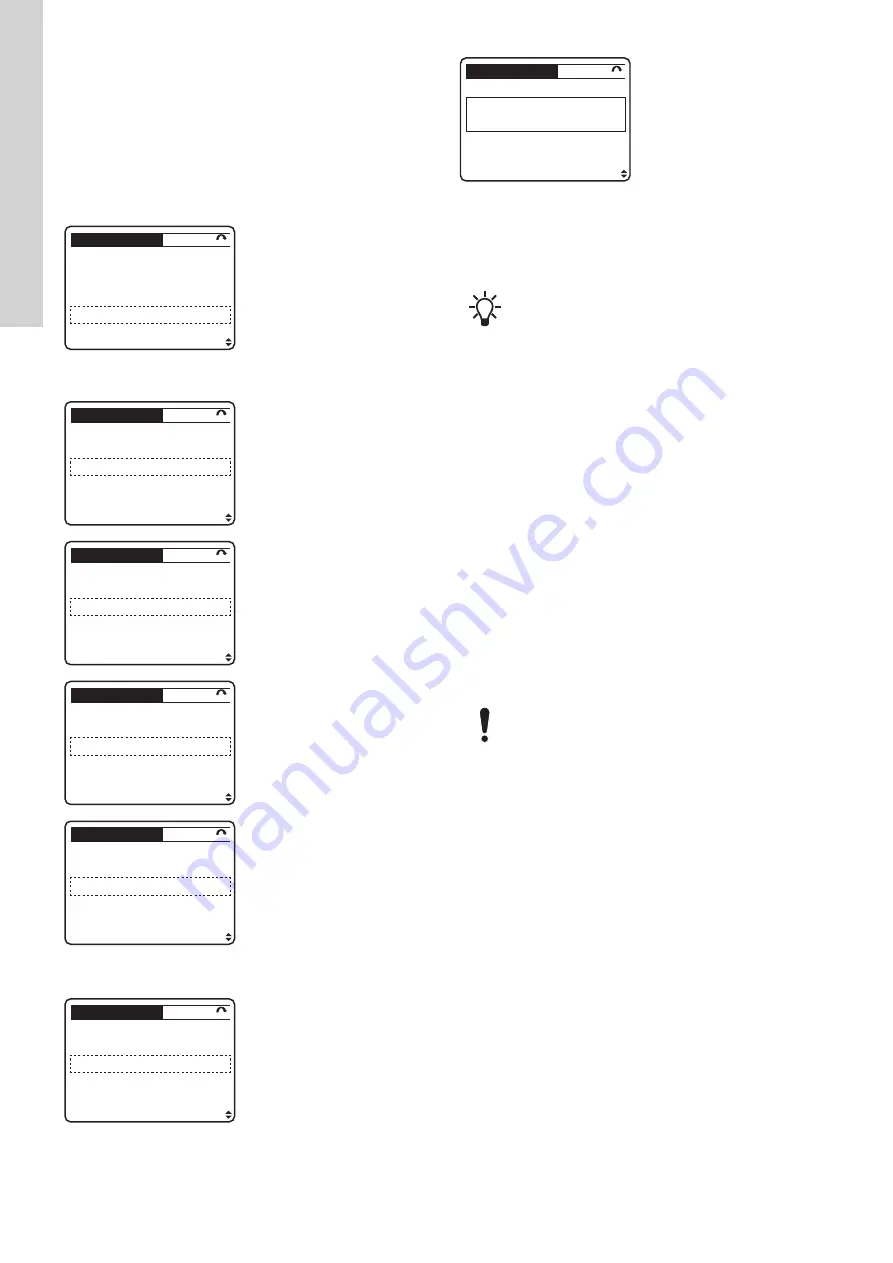
15. Here you can set a multipump system with multiple pumps
connected in parallel.
a. Variable speed pumps only: Alternation, Backup and
Cascade
b. Variable and Fixed speed pumps.
According to configuration No.1 and number of pumps select
one of the following steps for. In case that there are more than 2
pumps needed and MCO101 has been mounted.If
variable and fixed speed is needed, configuration No. 2 needs
to be selected.
1(1)
Setup a multi-pump system
consisting of this pump and
more pumps connected in
parallel?
No
Start-up Guide
TM077553
Multipump configuration via Modbus RTU
1(1)
Number of pumps?
6
Start-up Guide
TM077554
1(1)
Select desired function
Alternation
Start-up Guide
TM077555
1(1)
Select desired function
Backup
Start-up Guide
TM077556
1(1)
Select desired function
Cascade
Start-up Guide
TM077557
16. Enter the setpoint value based on the selected control mode
and feedback sensor.
1(1)
Enter Setpoint
xx.xx bar
Start-up Guide
TM077558
Setpoint
17. By pressing
OK
, the unit is ready to run the pump(s).
1(1)
Basic set-up is
completed!
Start-up Guide
TM077508
Setup completed
9.2 Uploading or downloading data
It is possible to download stored data from one frequency
converter and upload it to another.
You cannot cross platforms between CUE 202 (old model)
and CUE 203 (new model). CUE 203 is not compatible
with the keypad, storing and uploading settings of
CUE202.
1. Navigate to
0-5* Copy/Save
, and press
OK
.
2. Press
OK
to activate
0-50 LCP Copy
.
3. Press [Up] to select
[1] All to LCP
to upload data to the
operating panel, or select
[2] All from LCP
to download data
from the operating panel.
4. Press
OK
. A progress bar shows the uploading or downloading
progress.
9.3 Setting an asynchronous motor
To set an asynchronous motor manually in the [Main menu], enter
the following motor data available on the motor nameplate:
•
1-20 Motor Power [kW]
or
1-21 Motor Power [HP]
•
1-22 Motor Voltage
•
1-23 Motor Frequency
•
1-24 Motor Current
•
1-25 Motor Nominal Speed
•
1-29 Automatic Motor Adaptation (AMA)
.
9.4 Checking the motor rotation direction
There is a risk of damage to the pumps or the
compressors if the motor is running in the wrong direction.
Before starting the frequency converter, check the motor
rotation direction.
1. Navigate to
1-28 Motor Rotation Check
, and press
OK
.
2. Scroll to
[1] Enable
.
The following text appears:
Note! Motor may run in wrong
direction.
1. Press
OK
.
2. Follow the on-screen instructions.
To change the direction of rotation, remove power to the frequency
converter and wait before touching the product. See the waiting
time in the section for installation requirements.
•
Reverse the connection of any two of the three motor cables on
the motor or frequency-converter side of the connection.
Related information
9.5 Setting a permanent-magnet motor
To set a permanent-magnet motor manually in the [Main menu],
enter the motor data available on the motor nameplate.
1. To activate PM motor operation, set
1-10 Motor Construction
to
[1] PM, non salient SPM.
2. Set
0-02 Motor Speed Unit
to
[0] RPM
.
Program the following parameters in the listed order:
1.
1-24 Motor Current
2.
1-26 Motor Cont. Rated Torque
3.
1-25 Motor Nominal Speed
28
English (GB)