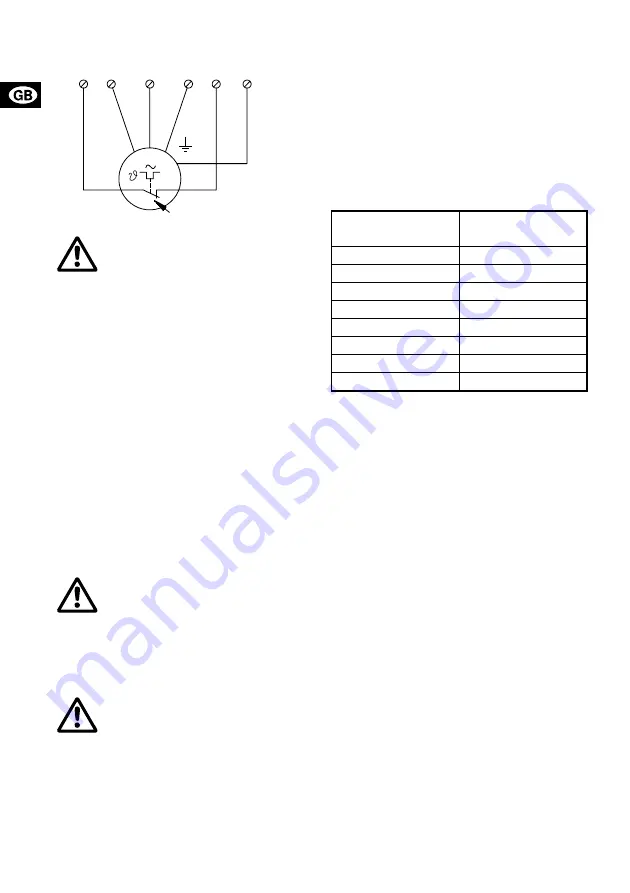
6
Fig. 1
6. Start-up
Do not start up the pump until the system has been
filled with liquid and vented. Make sure that the
pump is submerged in the liquid, open the isolating
valves, if fitted, and check the setting of the level
switches.
Note: The pump may, however, be started for a very
short period without being submerged for checking
of the direction of rotation.
6.1 Direction of rotation
Before starting up three-phase pumps, check the di-
rection of rotation. The direction of rotation should be
clockwise when viewed from above. When starting
up, the pump will jerk in the opposite direction to the
direction of rotation. If the direction of rotation is
wrong, interchange two of the three phases of the
electricity supply.
7. Maintenance and service
Before carrying out maintenance and service, make
sure that the pump has been thoroughly flushed with
clean water. Rinse the pump parts in water after dis-
mantling.
Pumps running normal operation should be in-
spected at least once a year. If the pumped liquid is
very muddy or sandy, inspect the pump at shorter in-
tervals.
When the pump is new or after replacement of the
shaft seals, check the oil level after one week of op-
eration.
For long and trouble-free operation of the pump the
following points should be checked regularly:
• Power consumption
• Oil level and oil condition
The oil becomes greyish white like milk if it con-
tains water. This may be the result of a defective
shaft seal. The oil should be replaced after 3000
hours of operation.
Use Shell Ondina 15 oil or similar type.
Note: Used oil must be disposed of in accordance
with local regulations.
The following table states how much oil the AP
pumps must have in the oil chamber:
Ex = explosion-proof.
• Cable entry
Make sure that the cable entry is watertight and
that the cables are not bent sharply and/or
pinched.
• Pump parts
Check the impeller, pump housing, neck ring, etc.
for possible wear. Replace defective parts.
• Ball bearings
Check the shaft for noisy or heavy operation (turn
the shaft by hand). Replace defective ball bear-
ings.
A general overhaul of the pump is usually required
in case of defective ball bearings or poor motor
function. This work must be carried out by the
manufacturer or a competent workshop.
7.1 Contaminated pumps
Note: If a pump has been used for a liquid which is
injurious to health or toxic, the pump will be classi-
fied as contaminated.
If GRUNDFOS is requested to service the pump,
GRUNDFOS must be contacted with details about
the pumped liquid, etc. before the pump is returned
for service. Otherwise GRUNDFOS can refuse to ac-
cept the pump for service.
Possible costs of returning the pump are paid by the
customer.
However, any application for service (no matter to
whom it may be made) must include details about
the pumped liquid if the pump has been used for liq-
uids which are injurious to health or toxic.
TM
0
0
1
618
0
693
The separate control box/motor starter
must not be installed in explosive environ-
ments.
Before starting work on the pump, make
sure that the electricity supply has been
switched off and that it cannot be acciden-
tally switched on. Furthermore, all rotating
parts must have stopped moving.
When unscrewing the inspection screw of
the oil chamber, please note that pressure
may have built up in the chamber. Do not
remove the screw until the pressure has
been fully relieved.
M
Max. 250V / 2.5 A
T1
U
V
W
T2
PE
Max. 250 V/2.5 A
Pump type
Quantity of oil in
oil chamber
AP70.80.09.3
0.80 l
AP70.80.09.3Ex
0.80 l
AP70.80.13.3
0.80 l
AP70.80.13.3Ex
0.80 l
AP70.80.19.3
1.20 l
AP70.80.19.3Ex
1.20 l
AP70.80.24.3
1.20 l
AP70.80.24.3Ex
1.20 l