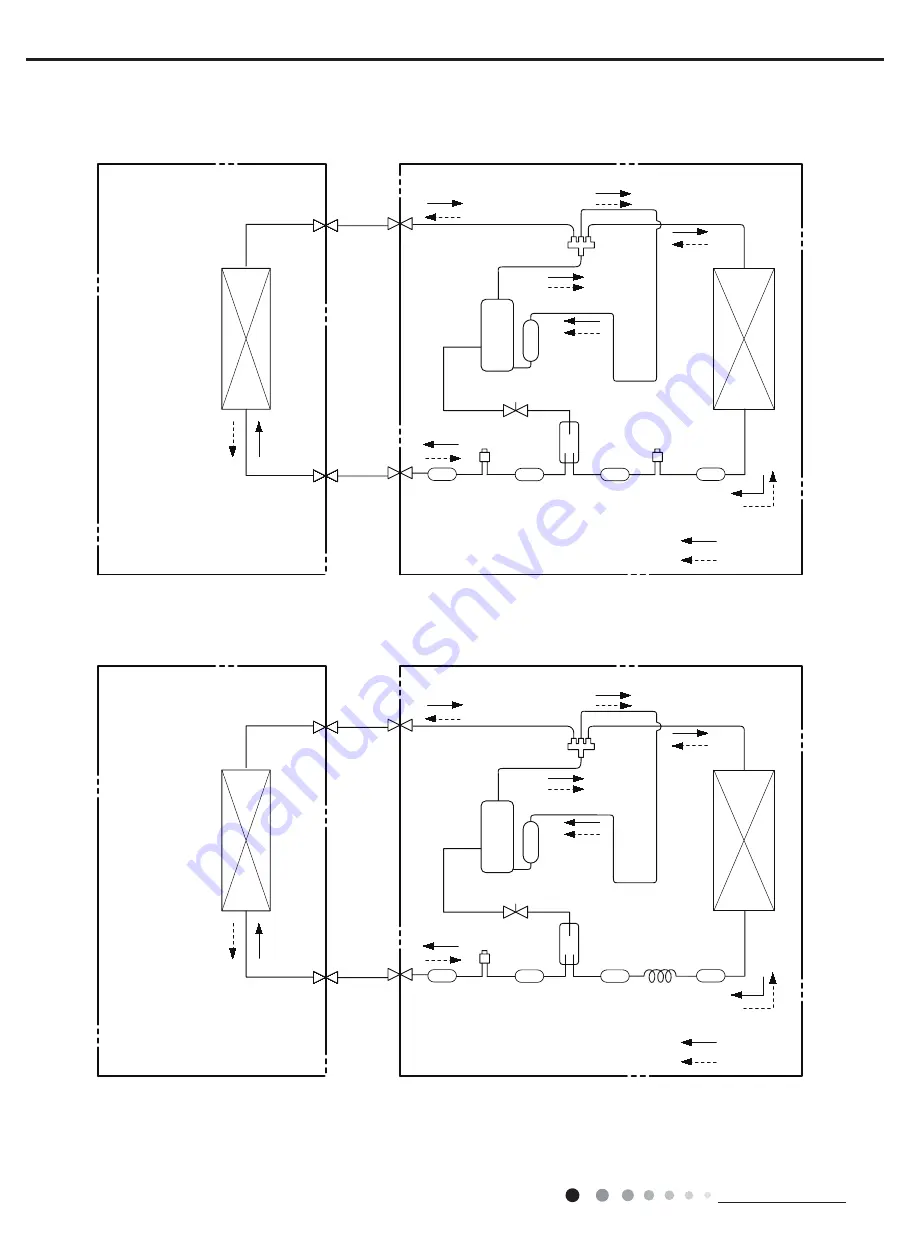
12
Technical Information
Service Manual
4. Refrigerant System Diagram
Connection pipe specification:
Liquid : 1/4" (6mm)
Gas pipe
: 3/8" (9.52mm)09/12K
Gas pipe: 1/2" (12mm)
18K
INDOOR UNIT
OUTDOOR UNIT
HEAT
EXCHANGE
(EVAPORATOR)
HEAT
EXCHANGE
(CONDENSER)
COMPRESSOR
GAS SIDE
3-WAY VALVE
LIQUID SIDE
2-WAY VALVE
COOLING
HEATING
Accumlator
Discharge
Suction
4-Way valve
Electron
Strainer
Strainer
expansion
valve
Electron
expansion
valve
Strainer
D
Strainer
Intercooler
INDOOR UNIT
OUTDOOR UNIT
HEAT
EXCHANGE
(EVAPORATOR)
HEAT
EXCHANGE
(CONDENSER)
COMPRESSOR
GAS SIDE
3-WAY VALVE
LIQUID SIDE
2-WAY VALVE
COOLING
HEATING
Accumlator
Discharge
Suction
4-Way valve
Electron
Strainer
Strainer
expansion
valve
Strainer
Capillary
D
Strainer
Intercooler
18K
09/12K