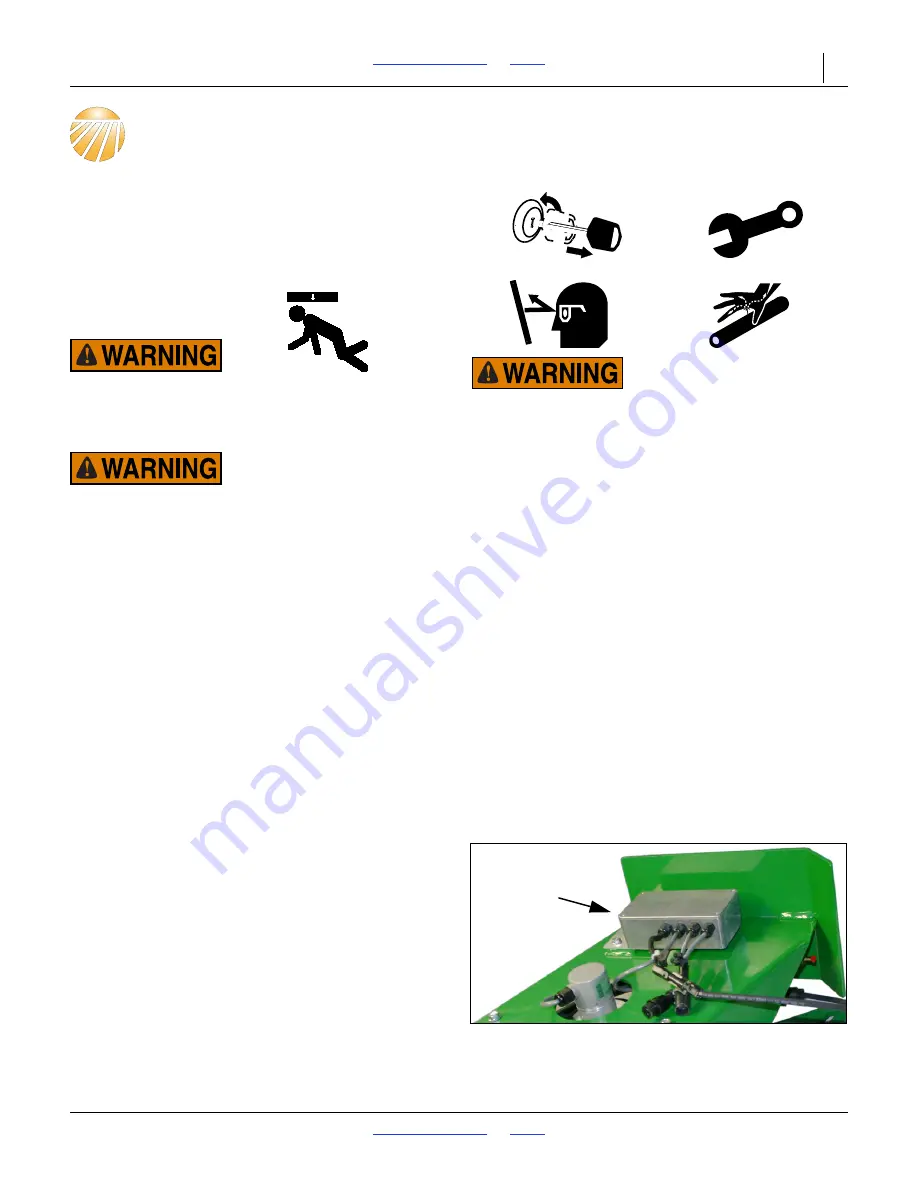
2019-03-08
196-359M
3N-4010F, 3N-4010HDF, and 3N-4020F
Maintenance and Lubrication
99
Maintenance and Lubrication
Proper servicing and maintenance is the key to long
implement life. With careful and systematic inspection,
you can avoid costly maintenance, downtime and repair.
Always turn off and remove the tractor key before
making any adjustments or performing any maintenance.
1. After initially running the drill for several hours, check
all bolts for tightness as specified in “
2. Lubricate point at “
3. Inflate tires per “
4. Replace any worn, damaged or illegible safety
decals. Order new decals from your Great Plains
dealer. “
5. Clean or replace any fittings that will not take grease.
6. Periodically check and secure all bolts, pins, and
fasteners. Tighten as specified on the “
7. Periodically inspect hydraulic hoses for cuts, cracks
and aging. Check fittings and cylinders for evidence
of leaks.
Welding
If electrical welding on the drill is ever necessary, take
these steps:
1. Disconnect all cables and harnesses at the hitch.
2. At the hydraulic drive motor mount, disconnect all
four leads at the VER-21568 Ext. Controller, and
remove this module from the drill.
OFF
Escaping fluid under pressure can have sufficient pressure to
penetrate the skin. Check all hydraulic lines and fittings before
applying pressure. Fluid escaping from a very small hole can
be almost invisible. Use paper or cardboard, not body parts,
and wear heavy gloves to check for suspected leaks. If an
accident occurs, seek immediate medical attention from a
physician familiar with this type of injury.
You may be severely injured or killed by crushing under a
falling drill. Always use transport locks or have frame
sufficiently blocked up when working on, and particularly
under drill.
Coulter and opener disk edges are very sharp. You may injure
Figure 139
VER-21568 Ext. Controller
28328