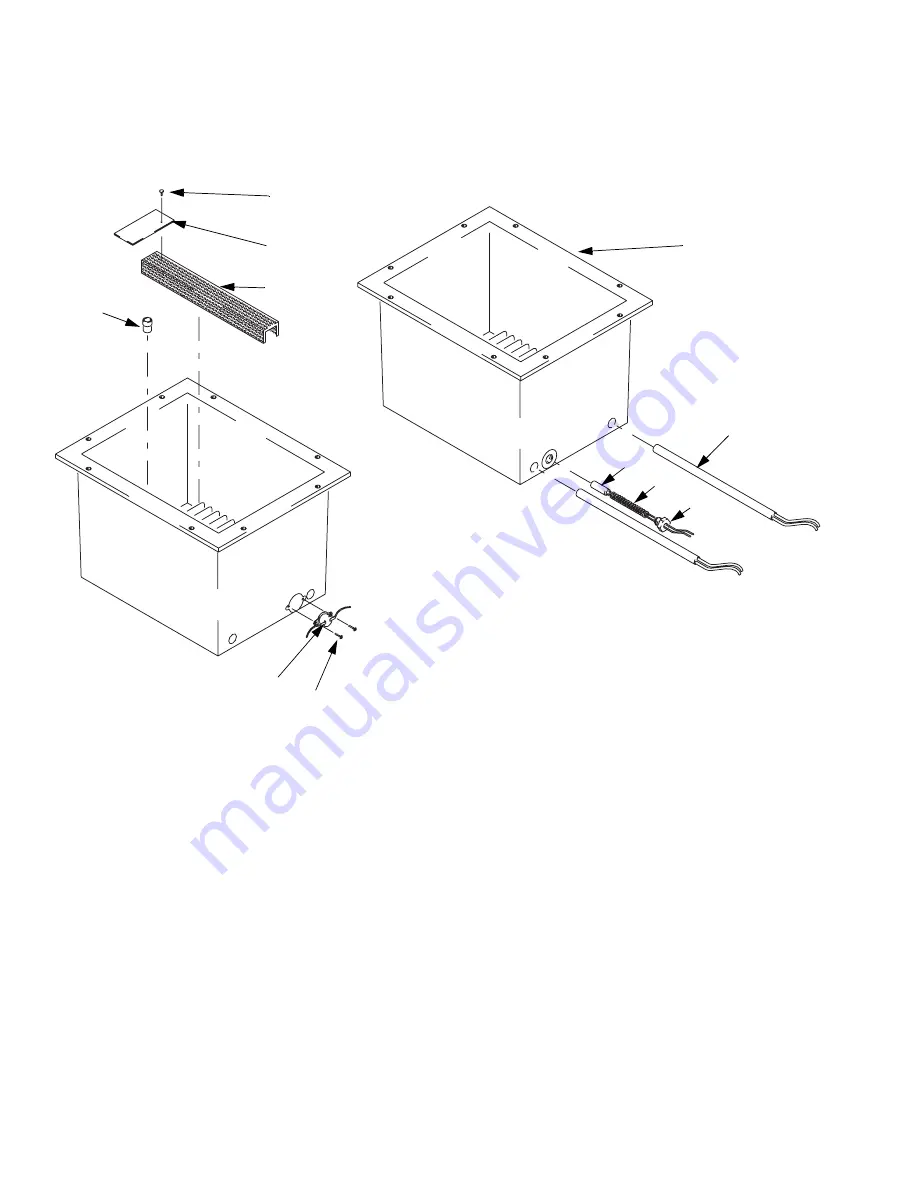
Parts
40
309832D
Tank assembly
Ref.
No.
Part No. Description
Qty.
42
CASTING
1
43
118173 HEATER, tank; 115V
2
118174 HEATER, tank; 230V
2
44
118209 THERMISTOR ASSY. (includes 45
and 46)
1
45
SPRING
1
46
NUT, retainer
1
47
SWTICH ASSY., over temp.
1
48
SCREW, cap #6-32 x 1/2 in.
2
49
FITTING, #14 tank insert
1
50
118211 SCREEN, tank filter; includes items
51 and 52.
1
51
PLATE, deflector
1
52
RIVET, pop; 1/8 x 1/8 in.
1
7$1.%$&.
7$1.)5217
49
42
43
44
46
45
48
51
52
ti5396a
47
50
Содержание THERM-O-FLOW T7 Series
Страница 36: ...Parts 36 309832D Parts Housing assembly 1 2 3 4 5 7 6 8 ti5398a 8 10 9 13 12 11 14 15 16 17 ...
Страница 41: ...Parts 309832D 41 ...
Страница 46: ...Schematics 46 309832D Base wiring ...
Страница 49: ...Technical Data 309832D 49 ...