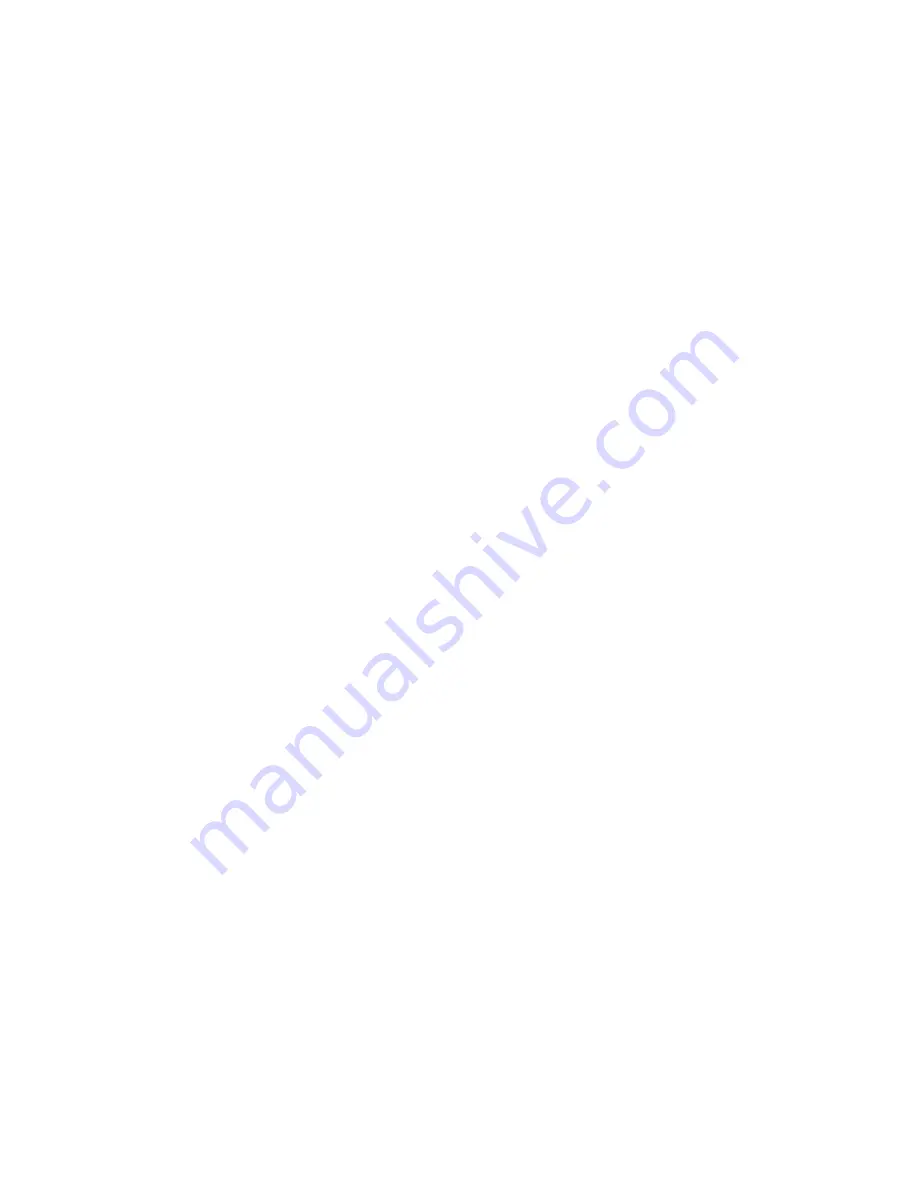
Download Log Files
Note
System configuration setting files and custom
language files can be modified if the files
are in the UPLOAD folder of the USB flash
drive. See System Configuration Settings
File, Custom Language File, and Upload
Procedure sections.
Note
If needed, set the number of days to
download on the Advanced Setup Screen
3–USB in the ADM. USB log frequency can
only be changed before logging occurs.
1. Insert USB flash drive into USB port.
2. The menu bar and USB indicator lights “USB
Busy” to indicate that the USB is downloading
files. USB activity is complete when the “USB
Busy” screen prompt disappears or the flash
drive LED stops flashing.
Note
Normal system spraying can continue
while download is in progress.
3. Remove USB flash drive from USB port.
4. Insert USB flash drive into USB port of computer.
5. The USB flash drive window automatically opens.
If it does not, open USB flash drive from within
Windows® Explorer.
6. Open GRACO folder.
7. Open the system folder. If downloading data
from more than one system, there will be more
than one folder. Each folder is labeled with the
corresponding serial number of the ADM (The
serial number is on the back of the ADM.)
8. Open DOWNLOAD folder.
9. Open DATAxxxx folder.
10. Open DATAxxxx folder labeled with the highest
number. The highest number indicates the most
recent data download.
11. Open log file. Log files open in Microsoft® Excel
by default as long as the program is installed.
However, they can also be opened in any text
editor or Microsoft® Word.
Note
All USB logs are saved in Unicode
(UTF-16) format. If opening the log
file in Microsoft Word, select Unicode
encoding.
Custom Language File
The custom language file name is DISPTEXT.TXT
and is stored in the DOWNLOAD folder.
A custom language file automatically downloads
each time a USB flash drive is inserted into the ADM.
If desired, use this file to create a user-defined set of
custom language strings to be displayed within the
ADM.
The system is able to display the following Unicode
characters. For characters outside of this set,
the system will display the Unicode replacement
character, which appears as a white question mark
inside of a black diamond.
• U+0020 - U+007E (Basic Latin)
• U+00A1 - U+00FF (Latin-1 Supplement)
• U+0100 - U+017F (Latin Extended-A)
• U+0386 - U+03CE (Greek)
• U+0400 - U+045F (Cyrillic)
332636C
79