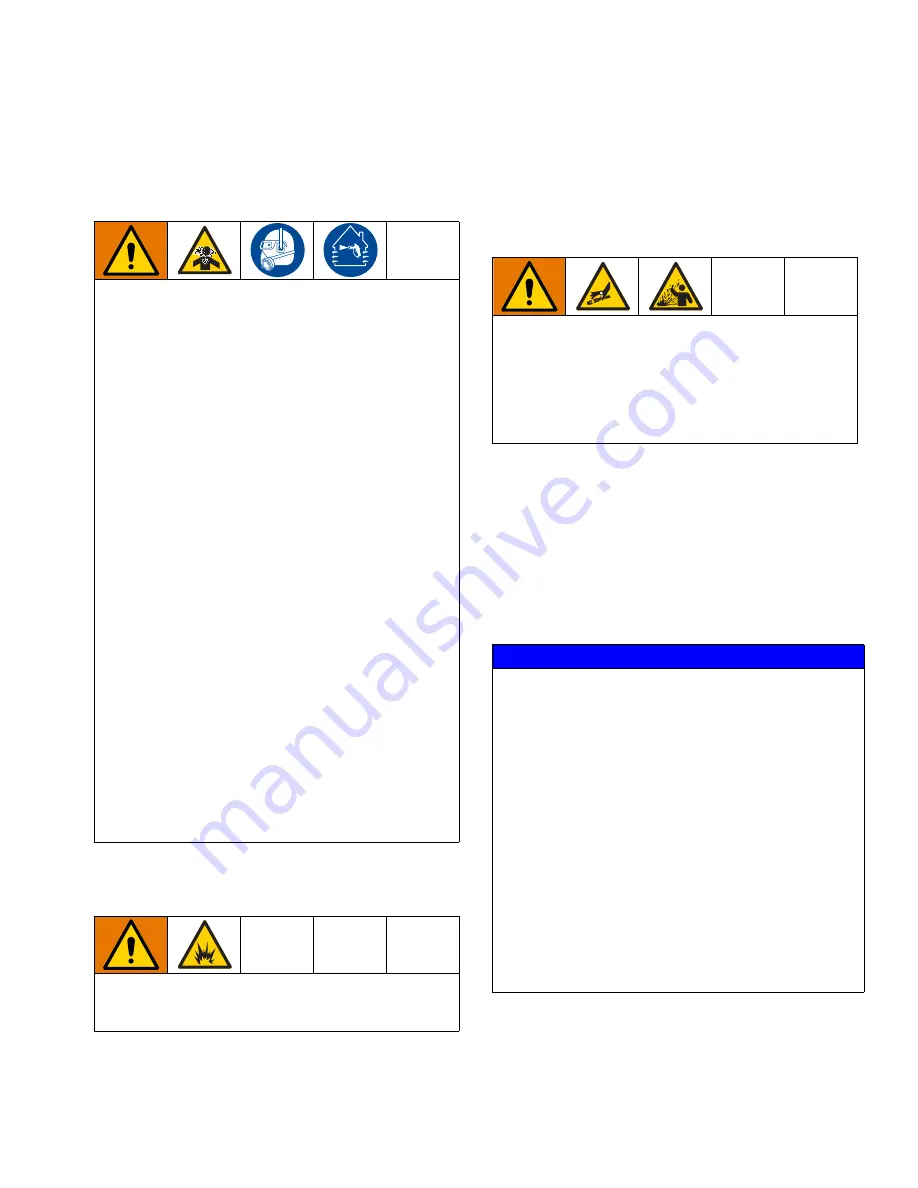
Important Isocyanate (ISO) Information
313566J
5
Important Isocyanate (ISO) Information
Isocyanate Conditions
Material Self-ignition
Keep Components A and B
Separate
Moisture Sensitivity of
Isocyanates
Exposure to moisture (such as humidity) will cause ISO
to partially cure, forming small, hard, abrasive crystal
that become suspended in the fluid. Eventually a film will
form on the surface and the ISO will begin to gel,
increasing in viscosity.
NOTE:
The amount of film formation and rate of crystal-
lization varies depending on the blend of ISO, the
humidity, and the temperature.
Spraying or dispensing fluids that contain isocyanates
creates potentially harmful mists, vapors, and
atomized particulates.
•
Read and understand the fluid manufacturer’s
warnings and Safety Data Sheet (SDS) to know
specific hazards and precautions related to isocy-
anates.
•
Use of isocyanates involves potentially hazardous
procedures. Do not spray with this equipment
unless you are trained, qualified, and have read
and understood the information in this manual and
in the fluid manufacturer’s application instructions
and SDS.
•
Use of incorrectly maintained or mis-adjusted
equipment may result in improperly cured mate-
rial. Equipment must be carefully maintained and
adjusted according to instructions in the manual.
•
To prevent inhalation of isocyanate mists, vapors,
and atomized particulates, everyone in the work
area must wear appropriate respiratory protection.
Always wear a properly fitting respirator, which
may include a supplied-air respirator. Ventilate the
work area according to instructions in the fluid
manufacturer’s SDS.
•
Avoid all skin contact with isocyanates. Everyone
in the work area must wear chemically imperme-
able gloves, protective clothing and foot coverings
as recommended by the fluid manufacturer and
local regulatory authority. Follow all fluid manufac-
turer recommendations, including those regarding
handling of contaminated clothing. After spraying,
wash hands and face before eating or drinking.
Some materials may become self-igniting if applied
too thick. Read material manufacturer’s warnings and
material Safety Data Sheet (SDS).
Cross-contamination can result in cured material in
fluid lines which could cause serious injury or damage
equipment. To prevent cross-contamination:
•
Never interchange component A and component
B wetted parts.
•
Never use solvent on one side if it has been con-
taminated from the other side.
NOTICE
Partially cured ISO will reduce performance and the life
of all wetted parts.
• Always use a sealed container with a desiccant
dryer in the vent, or a nitrogen atmosphere.
Never
store ISO in an open container.
• Keep the ISO pump wet cup or reservoir (if
installed) filled with appropriate lubricant. The
lubricant creates a barrier between the ISO and
the atmosphere.
• Use only moisture-proof hoses compatible with
ISO.
• Never use reclaimed solvents, which may contain
moisture. Always keep solvent containers closed
when not in use.
• Always lubricate threaded parts with an
appropriate lubricant when reassembling.