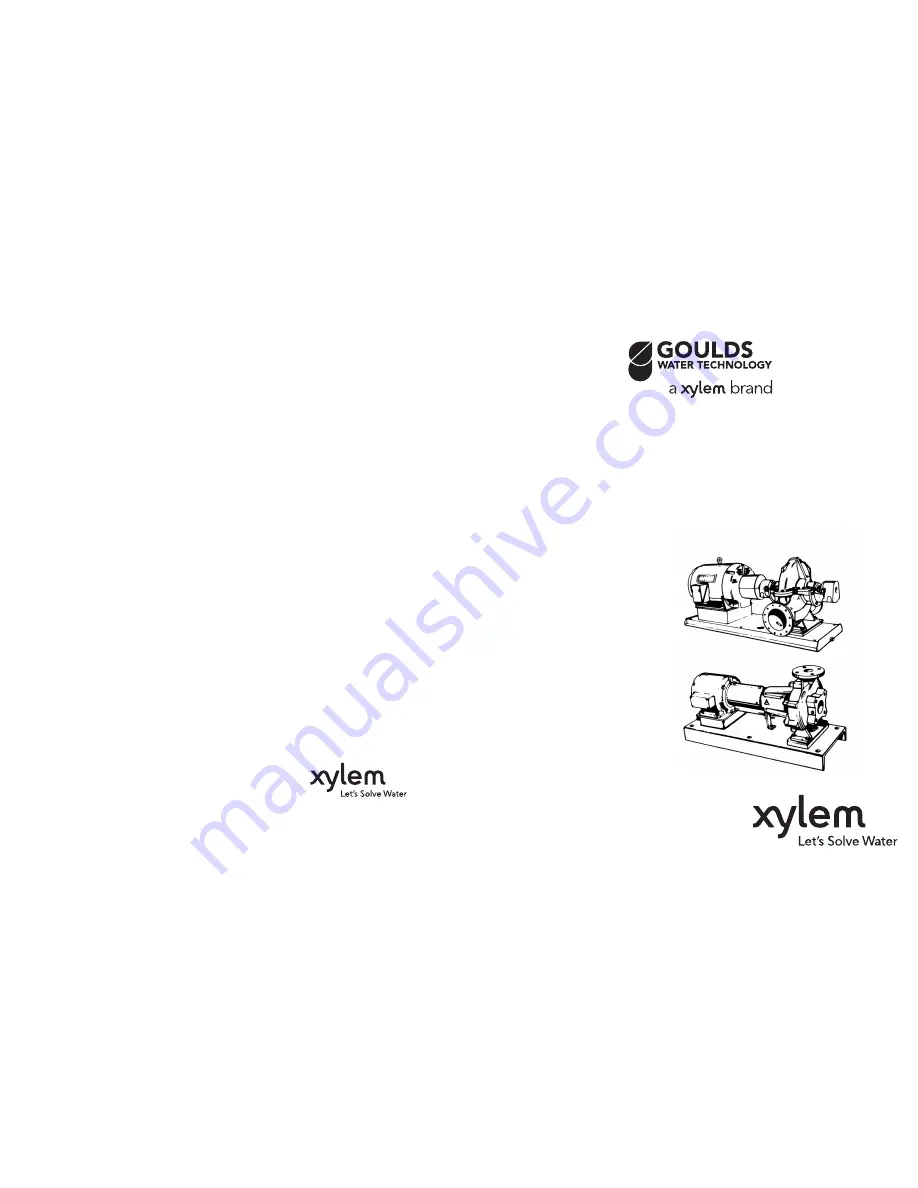
INSTRUCTION MANUAL
AC0921
G&L Pumps Series A-C
ALL HORIZONTAL AND
VERTICAL DRY-PIT PUMPS
Packing Adjustment – Fiber packing should not be tightened to the point of no leak-
age. Without some leakage packing may burn and score shaft or sleeve. With new pack-
ing, gradually take up gland with pump running to control leakage as packing seats. New
metallic packing may smoke during run-in. When seated, metallic packing forms a solid,
bearing-like surface. Adjust gland with pump running, for either type, to provide leakage of
40 to 60 drops per minute. Pipe away all leakage. Never tighten gland with pump is idle.
MECHANICAL SEALS
If pump has mechanical seals, check contract for engineering information as special
provisions may be necessary for pressurization, lubrication, cooling or flushing of seal.
Many seals, however, are ready to run without special attention. Consult nearest A-C Pump
representative if in doubt regarding seal operation.
LUBRICATION
Refer to applicable maintenance manuals for detailed information on lubrication of
driver and pump.
Oil-Lubricated Pumps
1. Maintain oil level as shown by a line in the sight glass or oil level indicator.
2. DO NOT OVER OIL. Over-oiling an cause bearings to run hot.
3. Use approved oil. See maintenance manual. Do not mix oils from different suppliers.
4. Check oil frequently for moisture, dirt or signs of “breakdown”.
In installations with moderate temperature changes, humidity, and dirt, the oil should
be changed after approximately 160 hours of operation. The oil should be inspected at this
time to determine the operating period before the next oil change. Oil change periods may
be increased up to 2000-4000 hours based on an 8000-hour year.
Grease-Lubricated Pumps
1. Examine grease in bearings at regular intervals. Watch for discoloration and con-
tamination which indicate need for flushing and regreasing.
2. Add grease every 3 to 6 months and flush yearly – or more often under adverse
conditions. Use lithium based NLGI-2 grade grease.
3. DO NOT OVER GREASE. Over-greased bearings may show signs of gailing. Under-
greased bearings may show signs of pitting. Bearing balls should roll, not slide.
4. After grease has been added to bearings, remove drain plug (where applicable) on
bottom of bearing housing for half an hour while pump is running.
Coupling Lubrication – check type of coupling used. Many couplings do not require
lubrication.
For additional information, refer to pump and driver maintenance manuals, which are avail-
able upon request.
Starting –
1. Close discharge valve.
2. Open fully all valves in suction line.
3. Turn on seal water to stuffing box (for external-injection). If pumped liquid is
dirty or if inleakage of air is to be prevented, this line should always be left open.
4. Prime the pump. If pump does not prime properly, or loses prime during start-
up, shut down and correct condition before repeating procedure.
5. For pump moving high temperature liquids, open warm-up valve to circulate
liquid for preheating. Close valve after pump is warm.
6. Start the pump driver. (Turbines and engines require warming up – consult
manufacturer’s instructions.)
7. When pump is operating at full speed, open discharge valve slowly. Damage
will result from overheating if pump operates with valve closed.
8. Adjust seal-liquid valves per stuffing box instructions.
Running
– Periodically inspect pump while running, but especially after first start,
and following repair.
1. Check pump and piping for leaks. Repair immediately.
2. Record pressure gage reading for future reference.
3. Record driver data.
4. Check pump bearing for lubrication and temperature.
5. Check and adjust stuffing box for correct operation. Check sealing water lines
and valves.
6. Adjust pump output (capacity) only with discharge valve. DO NOT throttle
suction line.
Shutdown
1. Close discharge valve slowly, unless system is automatically controlled..
2. Shut down driver promptly.
3. Close seal-liquid valves (for packed pumps). (If pumped liquid is dirty or if
inleakage is to be prevented, these external lines should always be left open.)
4. Open drain valves as required.
5. Close suction line valves, to retain prime or to isolate pump.
Freezing Protection – Protect pumps shut down during freezing conditions by
one of the following methods:
1. Drain pump, remove all liquid from the casing.
2. Keep fluid moving in pump and insulate or heat the pump to prevent freezing.
Do not use excessive heat – only enough to keep pump from freezing
3. Fill pump completely with antifreeze solution.
CAUTION: IF HEAT IS USED TO KEEP THE PUMP FROM FREEZING, DO NOT LET
THE TEMPERATURE OF THE PUMP OR LIQUID CONTAINED RISE ABOVE 150° F
MAINTENANCE
Operating conditions vary so widely that to recommend one schedule of preven-
tative maintenance for all centrifugal pumps is not possible. Yet some sort of regular
inspection must be planned and followed. We suggest a permanent record be kept of
the periodic inspections and maintenance performed on your pump. This recognition
of maintenance procedure will keep your pump in good working condition, and prevent
costly breakdowns.
One of the best rules to follow in the proper maintenance of your centrifugal pump
is to keep a record of actual operating hours. Then, after a predetermined period of
operation has elapsed, the pump should be given a thorough inspection. The length of
this operating period will vary with different applications, and can only be determined
from experience. New equipment, however, should be examined after a relatively short
period of operation. The next inspection period can be lengthened somewhat. This
system can be followed until a maximum period of operation is reached which should
be considered the operating schedule between inspections.
Periodic Inspection – Each month measure bearing temperature by thermometer.
If hot, inspect for excess lubricant and misalignments. See lubrication instructions.
NOTE: A bearing frame which feels hot to the touch of the hand is not necessarily
running at too high a temperature. Check with an accurate temperature measuring
device to be sure.
Every 6 months check packing, shaft or shaft sleeve for scoring, and alignment of
piping with pump.
Every year remove rotating element to inspect and clean thoroughly. Clean stuffing
box passages or external piping. Inspect, clean and check foot valves.
Cleaning – Remove oil, dust, dirt, water, chemicals from exterior of driver and
pump. Refer to applicable driver maintenance manual for cleaning procedures. If neces-
sary, use high pressure clean-out water (up to 80 psi maximum) to flush out any matter
clogging impeller or liquid passage. Be sure suction valve is closed during cleaning.
SAFETY FIRST – BE CAREFUL WHEN WORKING ON ANY OPERATING
MACHINERY. REPLACE COUPLING GUARD BEFORE STARTING PUMP.
RECHECK ROTATION.
G&L Pumps is a trademark of Xylem, Inc. or one of its subsidiaries.
Goulds is a trademark of Goulds Pumps, Inc. and is used under license.
© 2013 Xylem Inc. AC-0921 August 2013
Xylem Inc.
8200 N. Austin Avenue
Morton Grove, Illinois 60053
Phone: (847) 966-3700
Fax: (847) 965-8379
www.xyleminc.com/brands/gouldswatertechnology