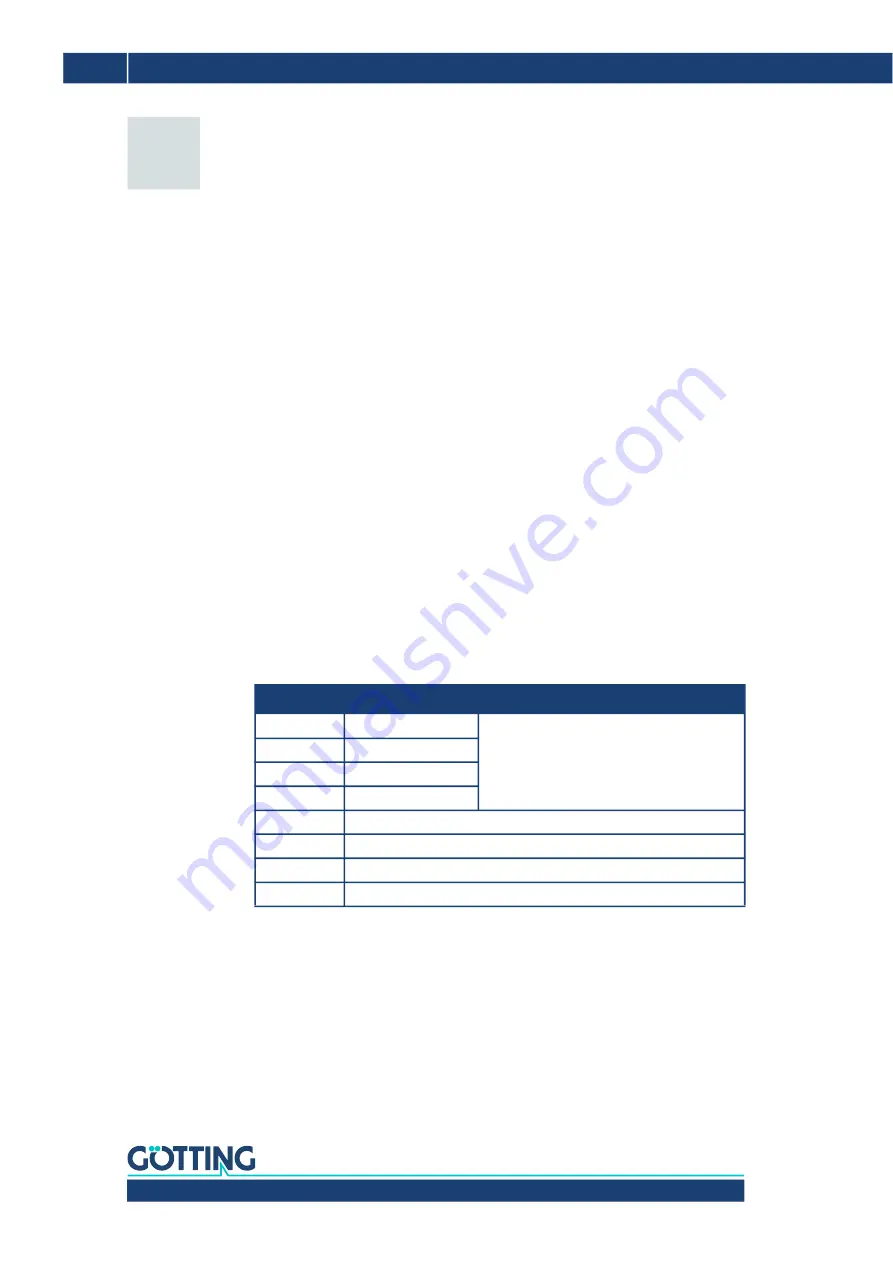
Device Description HG G-84300ZD | English, Revision 10 | Date: 01.06.2022
22
Chapter 7 – CANopen® Interface
The Node-ID and the transmission rate have to be configured with the serial monitor
program as described in section 5.3 on page 15.
The measurements of the system are transmitted via the so-called TxPDO. The de
-
vice is configured via SDOs. The CAN identifiers are derived from the node address
(1 to 127).
7.1 Description of the Process Data Objects (PDOs)
7.1.1 Transmission Objects
The measured values are transmitted at fixed positions inside the PDOs, a dynamic
mapping is not implemented. The PDO operational mode can be set to cyclical, syn
-
chronous or asynchronous mode. In order to avoid a bus load being too high due to
constant changes during asynchronous mode with non-cyclical transmission (Event
time = 0), the so-called Inhibit time can be set in the CAN menu of the serial monitor
(see 5.3 on page 15). A PDO can also be transmitted cyclically, therefore the event
time has to be chosen correspondingly and 0 has to be chosen for inhibit time.
A TPDO can be activated permanently by choosing in the synchronous mode (255)
inhibit time = 0, event_time = 0 and saving of the parameters. Additionally it can be
(de)activated temporarily by setting/deleting the highest bit in the corresponding
PDO-COB identifier, e.g. [1800,01] or [1801,01].
PDO_1 is sent with Identifier Node address. It contains 8 Bytes.
CANopen® Interface
Table 11
CANopen®: Structure of the transmitter box
Byte
Data
1
Byte 1 angle
Floating-Point Number according to IEEE
754, see Figure 13 on page 21
Unit: radian
2
Byte 2 angle
3
Byte 3 angle
4
Byte 4 angle
5
Lowbyte temperature
6
Highbyte temperature
7
System status, see Table 12 on page 23
8
Transmission counter
7