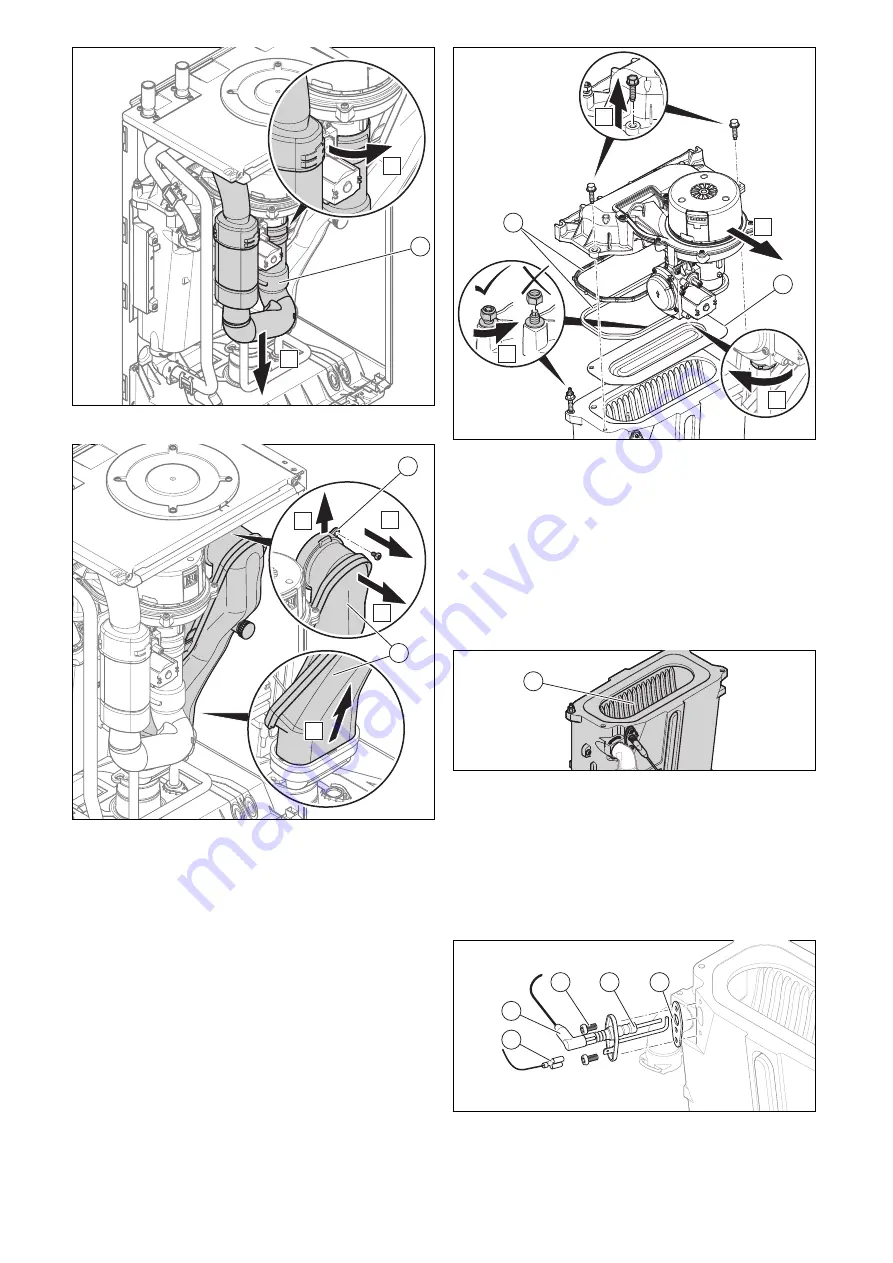
0020239568_03 Ultimate 3 Installation and maintenance instructions
31
A
B
1
4.
Remove the air intake pipe
(1)
.
D
C
B
2
3
A
5.
Remove the screw
(2)
.
6.
Push the clip upwards.
7.
Remove the flue pipe
(3)
.
B
A
D
C
4
5
8.
Remove the plugs from the gas valve assembly and
from the fan.
9.
Remove the gas-air mixture unit .
10. Remove both burner seals from the burner hood.
11. Remove the burner
(4)
.
12.7
Cleaning the heat exchanger
1.
Check the heat exchanger for damage and dirt.
2.
If required, clean and replace the heat exchanger.
3.
Protect the open electronics box from spraying water.
1
4.
Clean the ribs of the heat exchanger
(1)
with water.
◁
The water runs out via the condensate tray.
12.8
Checking the burner
▶
Check the surface of the burner for damage. If you see
any damage, replace the burner.
12.9
Checking the ignition electrode
1
2
3
4
5
1.
Disconnect the connection
(2)
and the earth cable
(1)
.
2.
Remove the fixing screws
(3)
.
Содержание Ultimate 3
Страница 1: ...en Installation and maintenance instructions Ultimate 3 25r A H GB 0020239568_03 31 07 2020...
Страница 49: ......
Страница 50: ......
Страница 51: ......